How Much Does Sand Casting Cost?
Sand casting is a versatile and widely-used manufacturing process that allows for the production of intricate metal parts and components. This method involves creating a mold from a sand mixture that can then be filled with molten metal. While sand casting is often celebrated for its flexibility and the ability to produce complex shapes, one of the most pressing questions for manufacturers and consumers alike is, “How much does sand casting cost?”
Factors Influencing the Cost of Sand Casting
The cost of sand casting can vary significantly based on several factors
1. Material Costs The type of metal being cast plays a crucial role in determining overall costs. Common materials include aluminum, iron, and bronze, each with differing prices. Aluminum tends to be more economical compared to other metals, while specialty alloys may drive costs higher.
2. Mold Creation The creation of the mold is one of the most significant expenses in the sand casting process. The complexity of the part dictates the design of the mold, which can be a one-piece or two-piece mold. Typically, more complex molds require more time and material to create, thereby increasing the overall cost.
3. Production Volume The cost per unit tends to decrease with higher production volumes. For large-scale manufacturing, the initial cost of creating molds can be amortized over a larger number of parts, resulting in a lower cost per unit. Conversely, small production runs may not benefit from these economies of scale, leading to higher per-unit costs.
4. Surface Finish and Tolerances The required surface finish and dimensional tolerances can greatly impact the cost. Higher precision and a finer surface finish need additional processes, such as machining or polishing, which can increase labor and material costs.
how much does sand casting cost
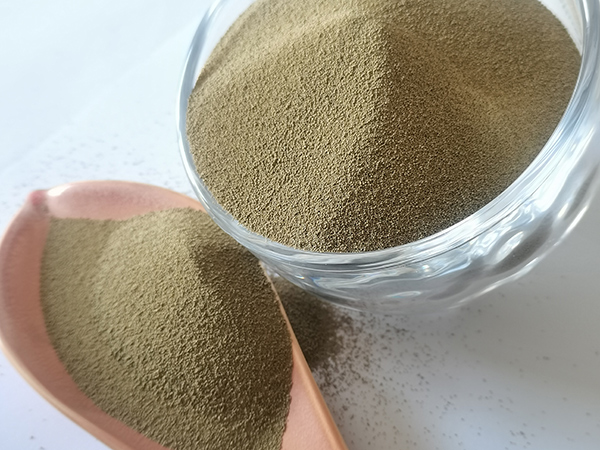
5. Labor Costs The location and skill level of the labor force can influence costs. Regions with higher wages will naturally see an increase in overall prices. Skilled labor, which is often required for intricate designs, can also add to costs.
6. Lead Time Quick turnaround times can increase costs, as expedited services often come with premium pricing. Standard production times may be less expensive, but they do require advanced planning.
Estimated Cost Breakdown
While it’s challenging to provide a one-size-fits-all answer to the cost of sand casting, some general estimates can help guide expectations.
- Setup Costs The initial setup for sand casting, including mold creation, can range from $500 to several thousand dollars, depending on complexity. - Cost per Unit For small to medium-sized components, the cost per unit can range from $20 to $500. Larger items or those requiring extensive machining may push costs significantly higher. - Finishing Costs Additional processes, such as machining, painting, or heat treating, can add $10 to $100 per unit to the overall cost, depending on the specifications.
Conclusion
In summary, the cost of sand casting is influenced by various factors including material choice, mold complexity, production volume, surface finish requirements, labor costs, and lead time. While the initial expense of setup can be considerable, the long-term benefits of sand casting—such as the ability to produce complex shapes and the flexibility of material options—often outweigh the costs. Understanding these factors will help manufacturers and consumers make informed decisions when considering sand casting for their projects. Whether you are looking for cost-effective solutions for large runs or intricate designs requiring precision, sand casting remains a valuable option in the manufacturing landscape.
Post time:නොවැ. . 07, 2024 21:46
Next:Sand Casting Manufacturing Facility for Precision Metal Components