Foundry Sand Properties An Overview
Foundry sand plays a pivotal role in the metal casting industry, providing a crucial medium for shaping and forming various metallic components. The properties of foundry sand significantly influence the quality of the final product, the efficiency of the casting process, and the overall effectiveness of the foundry operations. Understanding the essential properties of foundry sand is vital for both foundry engineers and metallurgists looking to optimize their materials and processes.
Chemical Composition
The chemical composition of foundry sand primarily consists of silica, with varying amounts of clay, silt, and moisture. Silica sand, specifically, is favored for its high melting point and strength, making it an ideal choice for metal casting. The purity of the silica is paramount; impurities like iron oxides can affect the quality of castings. The presence of clay acts as a binder, providing cohesion and enabling the sand to retain its shape during the pouring of molten metal.
Grain Size Distribution
Grain size and distribution are critical factors that influence the flowability of the sand, its packing density, and the surface finish of the casting. Foundry sand typically has a grain size ranging from 40 to 100 mesh. Coarser sands allow for better molding and easier removal of the casting, while finer sands can produce a smoother surface finish. Achieving the right balance in grain size is essential for producing high-quality castings with minimal defects.
Permeability
Permeability is the ability of foundry sand to allow gases generated during the pouring of molten metal to escape. This property is crucial, as insufficient permeability can lead to defects such as gas porosity in the castings. Good foundry sand should exhibit adequate permeability to prevent any build-up of gas, which can otherwise lead to casting defects. Typically, the permeability of foundry sand is influenced by its grain size, shape, and moisture content.
Moisture Content
foundry sand properties
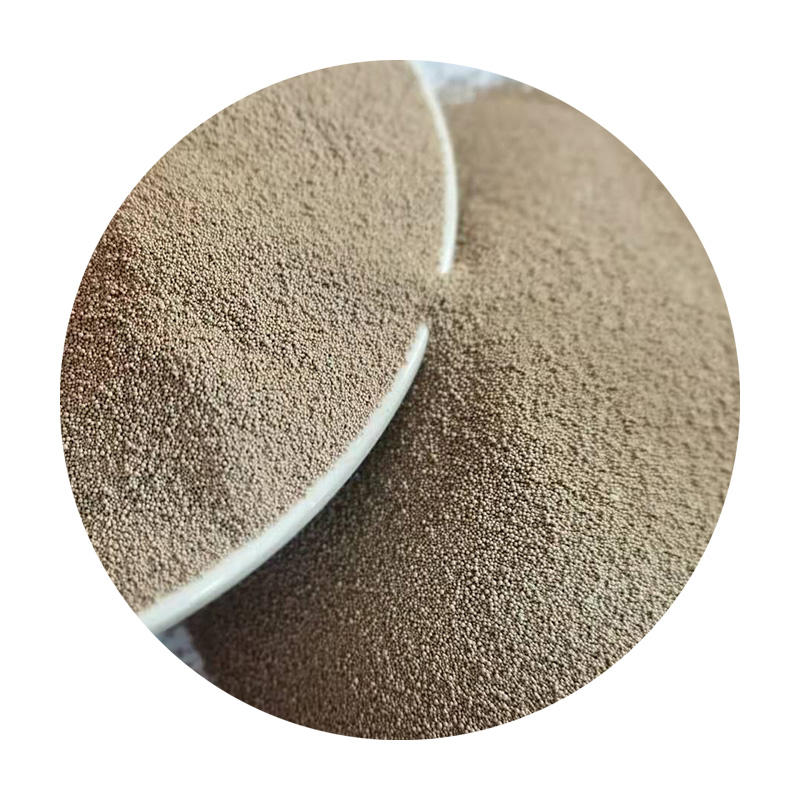
The moisture content in foundry sand affects its binding characteristics and stability. An optimal moisture level is necessary to achieve the right amount of adhesion between sand grains, which provides strength to the sand mold. However, excessive moisture can lead to steam generation during casting, causing explosion risks and compromising the integrity of the mold. On the other hand, insufficient moisture can result in poor mold strength and collapsibility during the pouring process.
Mold Strength
Mold strength is a critical property that determines the capability of the sand mix to withstand the liquid metal’s pressure without deforming. The strength of a sand mold is influenced by its composition, moisture level, and the presence of additives. A strong mold will ensure dimensional accuracy, reduce metal penetration, and minimize surface defects.
Core and Mold Design
The properties of the foundry sand also significantly impact core and mold design. Different casting processes, such as green sand molding or resin-bonded sand, require specific sand properties to optimize performance. For example, resin-bonded sands often exhibit higher strength and versatility than traditional green sands, making them suitable for more complex geometries and demanding applications.
Reusability
Another important aspect of foundry sand properties is its reusability. After a casting operation, sand can often be reclaimed and reused in subsequent casting processes. The durability of the sand affects its reusability, with proper treatment and conditioning required to maintain performance standards over multiple uses. Reducing waste through reclamation not only lowers operational costs but also promotes sustainability in the foundry industry.
Conclusion
In conclusion, the properties of foundry sand are integral to the quality and efficiency of metal casting processes. Factors such as chemical composition, grain size, permeability, moisture content, mold strength, and reusability must be carefully controlled and optimized. A thorough understanding of these properties enables foundries to enhance their operations and produce high-quality castings that meet industry standards. As the foundry industry continues to evolve, ongoing research into sand properties will be essential for advancing casting technologies and practices.
Post time:ඔක්. . 22, 2024 06:53
Next:ceramsite foundry sand