Understanding Foundry Sand Importance, Types, and Environmental Impact
Foundry sand is a critical material used in the metal casting process, serving as a mold and core component to shape molten metal into desired forms. This resource plays a significant role in industries such as automotive, aerospace, and manufacturing. The importance of foundry sand stems from its ability to withstand high temperatures and provide excellent surface finishes for casted products.
Types of Foundry Sand
There are several types of sand used in foundries, with the most common being silica sand. Silica sand is favored for its effective thermal resistance and ability to form fine molds. It is composed primarily of silicon dioxide and is abundant, making it a cost-effective choice for many applications.
Another type is olivine sand, which is composed of magnesium iron silicate. It has a high melting point and lower thermal expansion compared to silica. This type of sand is often preferred for specific foundry applications that require superior mold strength at elevated temperatures.
Additionally, there is chromite sand, which is derived from chromium ore. Chromite sand has excellent resistance to thermal shock and is less prone to fusion, making it suitable for casting high-temperature stainless steel and iron alloys. Moreover, there's also green sand, which is a mixture of silica sand, clay, and water, traditionally used in the foundry process due to its easy handling and reusability.
The Role of Foundry Sand in Metal Casting
foundry sand pdf
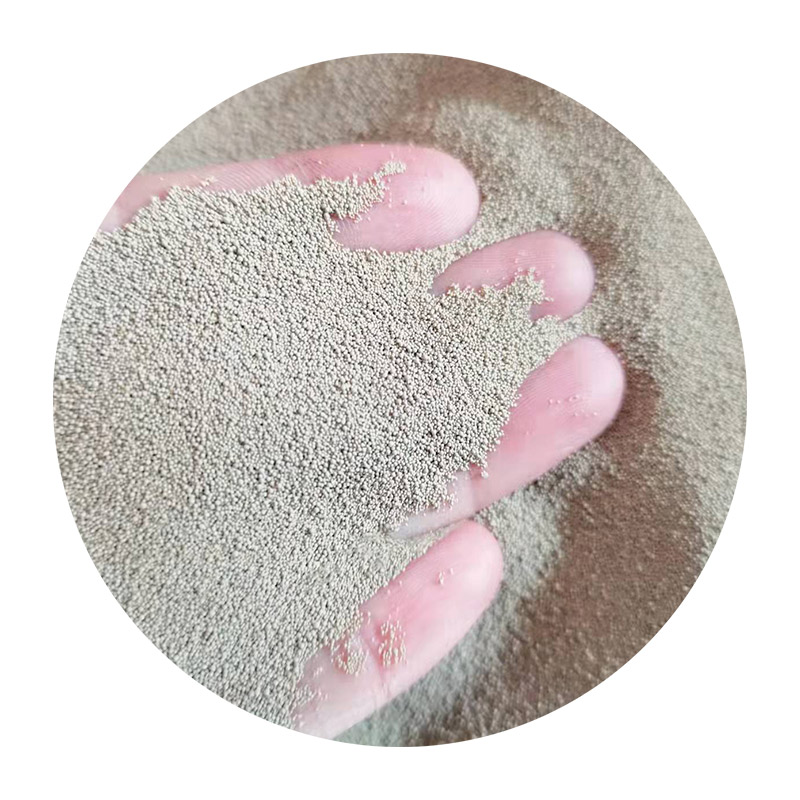
During the casting process, foundry sand is shaped into molds that comprise the external form of the desired product. The sand's grains hold together to create intricate designs that allow for detailed mold patterns. Subsequently, molten metal is poured into these molds. As the metal cools and solidifies, it takes the shape of the mold, resulting in a final product that may only require minimal finishing.
The performance of foundry sand is vital in determining the quality of the final cast product. Variables such as grain size, clay content, and moisture content can significantly influence the melting process, mold strength, and surface quality of the cast item. For this reason, foundry operators must closely monitor and adjust these parameters to maintain production efficiency and product quality.
Environmental Impact and Recycling of Foundry Sand
The extraction and use of foundry sand pose environmental challenges, particularly concerning the sustainability of natural sand resources. Consequently, the foundry industry has made strides toward recycling used sand. This practice not only reduces waste but also lessens the demand for raw materials. Used foundry sand can be reprocessed and blended with new sand, allowing for a reduction in the environmental footprint.
Moreover, research is ongoing to explore innovative techniques for repurposing waste foundry sand in other applications, such as in construction, landfill cover, or as an additive in cement production. These steps are essential in promoting a circular economy in the casting industry.
Conclusion
Foundry sand plays a pivotal role in metal casting, offering the necessary properties to create complex molds and high-quality castings. Understanding the different types of foundry sand, its applications, and the environmental implications of its use is crucial for industry stakeholders. By focusing on sustainable practices and recycling, the foundry industry can continue to enhance its operational efficiency while minimizing its ecological impact. The future of foundry sand lies in balancing industrial needs with environmental stewardship, ensuring that this vital resource is used responsibly and efficiently.
Post time:ජන. . 02, 2025 09:07
Next:casting sand