Facing Sand in Foundry An Essential Element for Quality Casting
In the realm of metal casting, the choice of materials plays a crucial role in determining the quality of the final product. One such indispensable material is facing sand, which is a critical component used in the foundry industry. Facing sand is a specially formulated sand mixture applied to the surface of the mold cavity, and its role is pivotal in defining the characteristics of the cast surface.
The Purpose of Facing Sand
The primary function of facing sand is to create a smooth and accurate mold surface, which directly impacts the quality of the casting. When molten metal is poured into the mold, it can sometimes react with the sand, leading to defects such as sand inclusions or irregular surfaces. Facing sand helps mitigate these issues by forming a protective layer that enhances the finishing properties of the casting, ensuring a more precise shape and surface finish.
Composition of Facing Sand
Typically, facing sand is composed of silica sand along with various additives, depending on the specific requirements of the casting process. Common additives include clay, which provides plasticity and strength, and various chemicals that can improve the thermal stability of the sand. The right mixture of sand grains and additives ensures that the facing sand can withstand the high temperatures of molten metal without breaking down or compromising the mold's integrity.
Types of Facing Sands
facing sand in foundry
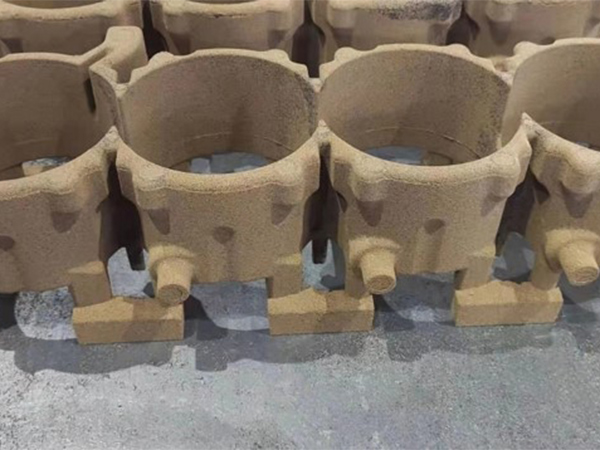
Different types of facing sands are utilized depending on the specific casting requirements and processes. For instance, in ferrous metallurgy, zircon sand might be chosen due to its high melting point and resistance to thermal shock. This choice helps in yielding a smooth cast surface while minimizing metal penetration into the sand. On the other hand, for non-ferrous metals, smoother sands with finer grain sizes, such as talc or olivine, can be used to achieve even finer finish results.
Impact on Casting Quality
Using high-quality facing sand has a measurable impact on the quality of castings. It not only influences the surface finish but also affects the mechanical properties of the final product. Properly formulated facial sands can enhance the tensile strength of the cast metal, thus contributing to a longer lifespan of the components. In addition, it aids in reducing defects, such as blowholes or pinholes, which can compromise the structural integrity of metal components.
Conclusion
The role of facing sand in foundry applications cannot be overstated. It serves as a barrier between the molten metal and the mold material, ensuring a smooth finish and preserving the quality of the casting. For foundries aiming to produce high-quality metal components, investing in the right type of facing sand is crucial. By understanding its properties and utilizing appropriate mixing techniques, foundries can consistently deliver superior cast products that meet stringent industry standards. As technology advances, so will the formulations and applications of facing sand, but its fundamental importance in ensuring quality casting will remain unchanged.
To remain competitive in the foundry industry, understanding the nuances of facing sand, including its selection and application, is vital. As foundries continue to innovate and improve their processes, facing sand will undoubtedly remain a cornerstone of successful casting operations.
Post time:දෙසැ. . 07, 2024 14:23
Next:3D Printed Sanding Machines for Precision Engineering and Custom Components