The Sand Casting Process An In-Depth Overview
Sand casting is one of the oldest and most versatile metal forming techniques used across various industries, from automotive to aerospace. This traditional method has evolved over centuries, primarily due to its simplicity, cost-effectiveness, and ability to create intricate shapes. In this article, we will explore the sand casting process, its key components, advantages, and applications.
What is Sand Casting?
Sand casting, also known as sand mold casting, involves creating a mold from a mixture of sand, clay, and water. This mold serves as the negative impression of the desired object. Once the mold is prepared, molten metal is poured into it to create the final product. After the metal cools and solidifies, the sand mold is removed, revealing the casted item.
Key Components of the Sand Casting Process
1. Pattern Creation The first step in sand casting is creating a pattern that reflects the final object. Patterns are typically made of metal, wood, or plastic and are designed slightly larger to account for shrinkage during cooling. Patterns can be single-use or reusable and are essential for determining the shape and dimensions of the cast.
2. Mold Making The pattern is then used to make the sand mold. The mold consists of two halves the cope (top half) and the drag (bottom half). The pattern is pressed into a mixture of sand and a bonding agent—usually clay—creating an imprint. Once both halves are prepared, they are assembled, and key features like gates and risers are added. Gates allow the molten metal to enter the mold, while risers help manage the flow and allow for any potential air pockets.
3. Melting the Metal The next step involves melting the chosen metal, which can range from aluminum to ferrous alloys. This is done in a furnace, where the metal is heated to its liquid state. The suitability of the metal for sand casting depends on various factors, including its melting point and fluidity.
4. Pouring Once the metal is molten and at the appropriate temperature, it’s poured carefully into the mold through the gate. Timing and technique are crucial during this phase to minimize turbulence and ensure that the mold is filled uniformly.
describe sand casting process
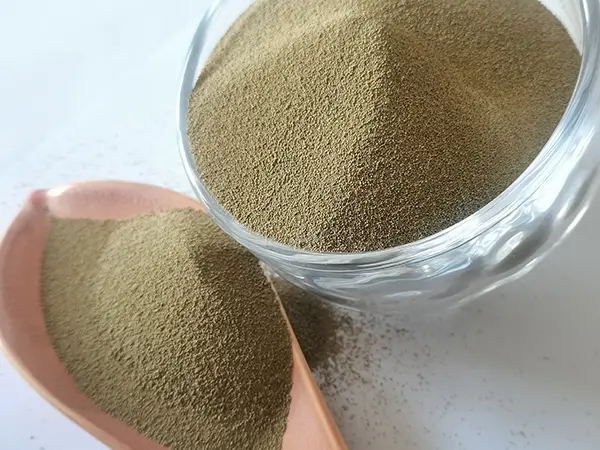
5. Cooling and Solidification After pouring, the metal needs time to cool and solidify. This process can take anywhere from a few minutes to several hours, depending on the size and thickness of the part. Heat treatment may also be applied post-casting to enhance the material properties of the metal.
6. Mold Removal Once the metal has cooled, the sand mold is broken apart to retrieve the final casting. This is often facilitated by shaking or vibrating equipment that dislodges the sand. Any sand that is still attached is removed through sand blasting or other cleaning processes.
7. Finishing The final step involves finishing operations such as machining, grinding, or polishing to achieve the desired surface finish and dimensional accuracy. Additional processes like heat treatment may also be applied to improve the mechanical properties of the casting.
Advantages of Sand Casting
- Versatility Sand casting can be used to produce various shapes and sizes, making it suitable for small and large production runs. - Cost-Effective The materials used in sand casting are relatively inexpensive, and the process requires less investment in tooling compared to other casting methods. - Ability to Handle Complex Designs The sand mold can capture intricate details, allowing for the production of complex geometries that might be challenging with other methods. - Easily Scalable Sand casting can easily accommodate production modifications, making it ideal for prototypes and large scale manufacturing.
Applications of Sand Casting
Sand casting finds application in various industries. It is widely used in automotive manufacturing to produce engine blocks and cylinder heads. In the aerospace sector, components such as turbine blades are also often created using sand casting. Other applications include machinery parts, sculptures, and art pieces.
Conclusion
In summary, the sand casting process is a time-tested method of metal casting that combines simple materials with intricate design capabilities. Its flexibility and cost-efficiency make it an appealing choice for a vast array of industries, continuing to play a significant role in modern manufacturing. Whether creating complex mechanical components or artistic sculptures, sand casting remains a fundamental technique in the engineer’s toolkit.
Post time:ඔක්. . 11, 2024 07:14
Next:rapid sand casting