An Overview of Sand Casting
Sand casting is one of the oldest and most widely used metal casting processes. It involves creating a mold from a mixture of sand, clay, and water, into which molten metal is poured to create a desired shape. This technique offers numerous advantages, making it a popular choice across various industries.
The Sand Casting Process
The sand casting process begins with the creation of a pattern, which is a replica of the final product. The pattern is typically made from metal, plastic, or wood and serves as a template for the sand mold. The next step involves preparing the sand mold. This is achieved by mixing sand with a binder, often clay, and water to improve the sand’s cohesiveness. The resulting mixture is packed tightly around the pattern to form a mold cavity.
After the mold is formed, the pattern is removed, leaving a negative impression of the desired shape. The two halves of the mold are then assembled, ensuring that they align correctly to prevent any misalignment during the pouring phase. Before pouring the molten metal, the mold is often heated to reduce thermal stress during the casting process.
Once everything is prepared, molten metal is poured into the mold cavity. The heat from the molten metal prevents the sand from igniting, but careful control of temperature is essential to avoid defects. After the metal solidifies, the mold is broken apart, revealing the cast piece. This is often followed by cleaning the castings to remove any sand and excess material.
Advantages of Sand Casting
describe sand casting
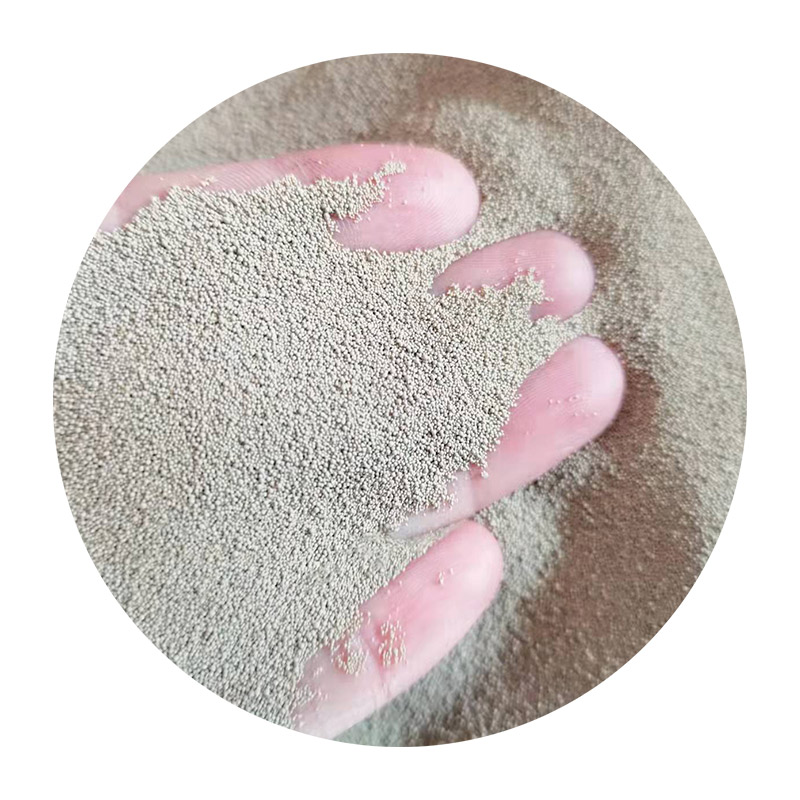
One of the primary advantages of sand casting is its versatility. This process can accommodate a wide range of metals, including iron, aluminum, and bronze, which allows manufacturers to choose materials suited to specific applications. Additionally, sand casting is capable of producing complex shapes and large-sized components that would be difficult or impossible to achieve with other casting methods.
Cost-effectiveness is another significant benefit. The materials used in sand casting are relatively inexpensive, and the process can be quickly set up for small production runs. This makes it an ideal choice for prototype development and low-volume manufacturing. Furthermore, the sand molds are reusable, contributing to reduced material waste.
Sand casting also allows for excellent surface finish and dimensional accuracy. By using high-quality sand and precise patterns, manufacturers can achieve a good surface finish, which may reduce the need for further machining operations. Moreover, the method's flexibility means that adjustments can easily be made to patterns for subsequent runs, providing adaptability in production.
Applications of Sand Casting
Sand casting has a broad range of applications across different industries. It is widely used in automotive manufacturing for engine blocks, flywheels, and transmission cases. In the aerospace sector, it is employed for producing complex components that require lightweight materials. Additionally, sand casting finds its place in the production of various industrial parts, artistic sculptures, and decorative items.
In conclusion, sand casting is a time-honored technique that continues to be relevant in today’s manufacturing landscape. With its ability to produce intricate shapes, cost-effective materials, and versatility across various metals, sand casting remains a crucial process in metalworking. As technology advances, further innovations in sand casting techniques could enhance its efficiency and application, solidifying its place in the future of manufacturing.
Post time:සැප්. . 30, 2024 21:37
Next:Löydä oikea hiekka valmistukseen ja sen käyttötavat