Components of Sand Casting
Sand casting is one of the oldest and most versatile manufacturing processes. It involves creating metal parts by pouring molten metal into a mold made of sand. The success of the sand casting process relies on several key components that work together to produce high-quality castings suitable for a wide range of applications.
One of the primary components of sand casting is the mold, which is typically composed of a mixture of sand, clay, and water
. This mixture is crucial as it provides the necessary strength and flexibility to withstand the heat of molten metal. The sand grain size and shape also play a significant role in determining the surface finish and dimensional accuracy of the final cast.Another essential component is the pattern, which is a replica of the final product to be cast. Patterns are usually made from materials such as wood, metal, or plastic. They are designed to create an impression in the sand mold, allowing for the shape of the casting to be formed. Patterns can be single-use or reusable, depending on the production volume and complexity of the design.
components of sand casting
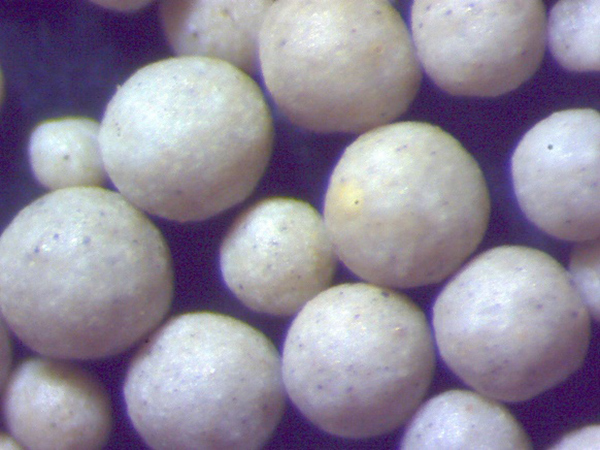
The pouring system, which includes the sprue, runner, and gates, is vital for directing molten metal into the mold cavity. The sprue is the vertical channel through which the metal enters the mold, while the runner connects the sprue to the mold cavity. Gates are the entry points where molten metal flows from the runner into the mold, ensuring a uniform filling that minimizes defects.
Once the metal is poured, cooling and solidification occur. The cooling rate can greatly affect the mechanical properties of the casting. Thus, controlling the temperature and cooling environment is essential to avoid issues such as warping or shrinkage.
After the metal has solidified, the mold is removed, and the casting is extracted. This stage often requires additional components such as shaking machines or hammers to dislodge the mold. The final casting may then undergo secondary processes, such as cleaning, machining, or heat treatment, to achieve the desired specifications.
In conclusion, the components of sand casting, including the mold, patterns, pouring systems, and cooling processes, are integral to producing high-quality castings. This traditional manufacturing technique remains widely used due to its cost-effectiveness and the ability to create complex shapes, making it an essential method in industries ranging from automotive to aerospace. Understanding these components allows manufacturers to optimize the sand casting process for improved efficiency and quality.
Post time:නොවැ. . 03, 2024 05:22
Next:sanding resin