The Role of Ceramsite Foundry Sand in Modern Casting Processes
In the realm of metal casting, the materials used in the molding and core-making processes play a pivotal role in determining the quality and efficiency of the final products. One such material that has gained significant traction in recent years is ceramsite foundry sand. This innovative material, distinguished by its unique properties, offers a myriad of advantages over traditional casting sands, making it a preferred choice in various foundry applications.
What is Ceramsite Foundry Sand?
Ceramsite foundry sand is a type of artificial sand derived from the finely processed clay and other additives, which are heated to high temperatures and then cooled to form lightweight, low-density aggregates. The production process involves a meticulous combination of materials that results in granules with uniform shapes and sizes, ensuring optimal flowability and packing density. This engineered material stands out for its superior thermal properties and mechanical strength, which are essential for effective casting.
Advantages of Ceramsite Foundry Sand
1. Improved Surface Finish One of the standout features of ceramsite foundry sand is its smooth surface texture. Unlike traditional sands, ceramsite offers a finer grain structure that significantly reduces defects such as sand inclusions and surface irregularities on cast products. This results in a superior finish, often eliminating the need for extensive post-casting machining.
2. Thermal Conductivity Ceramsite foundry sand exhibits excellent thermal properties, allowing it to withstand high temperatures without degrading. This is vital during casting processes where molten metals are poured into molds. The sand can maintain its integrity, thereby preventing the formation of cracks or other defects that could compromise the casting quality.
ceramsite foundry sand
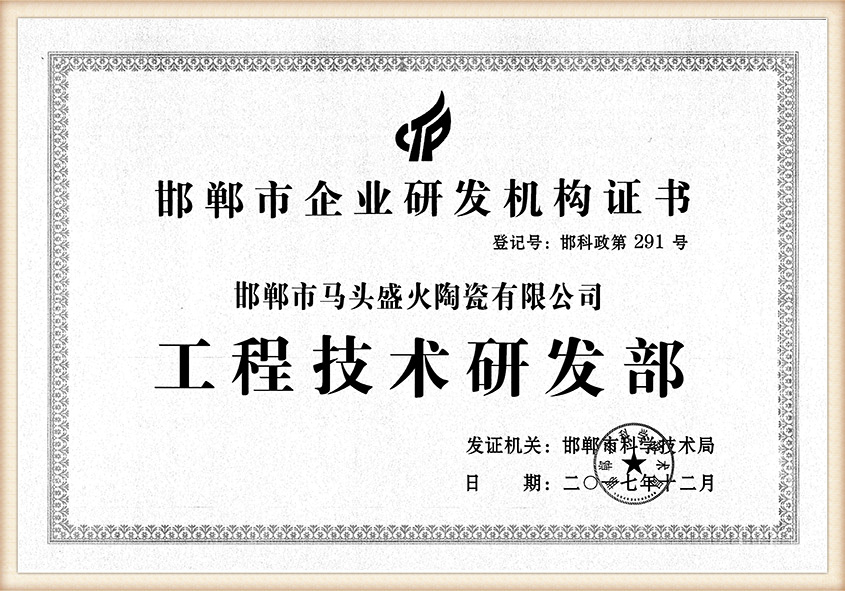
3. Recyclability Environmental concerns are paramount in today's industrial landscape. Ceramsite foundry sand is highly recyclable, which means it can be reused multiple times without losing its effectiveness. This feature not only lowers the cost of production but also minimizes waste and contributes to sustainable practices within the foundry industry.
4. Lowering Moisture Absorption Compared to traditional sands, ceramsite foundry sand has a lower moisture absorption rate. This property helps in maintaining the ideal moisture level in molds, reducing the likelihood of defects associated with excessive moisture, such as sand sticking to the mold or insufficient casting.
5. Enhanced Productivity The utilization of ceramsite foundry sand can lead to improved productivity in foundries. Its flowability allows for faster filling of molds, while its quick setup time translates into shorter cycle times. As a result, foundries can produce more castings with the same equipment, leading to increased efficiency and profitability.
Challenges and Considerations
While ceramsite foundry sand offers numerous benefits, it is essential to consider the initial investment involved in switching from traditional sands to ceramsite. Foundries may need to adapt their existing processes and training accordingly. Additionally, as with any material, the specific needs of the casting process should guide the decision on whether to incorporate ceramsite foundry sand.
Conclusion
In conclusion, ceramsite foundry sand represents a significant advancement in the field of metal casting. Its superior properties offer a range of advantages, including improved surface finishes, excellent thermal stability, and environmental sustainability through recyclability. As the casting industry continues to evolve, the adoption of innovative materials like ceramsite foundry sand will be crucial in meeting the growing demands for high-quality and efficient production processes. Foundries that invest in such advanced materials are likely to gain a competitive edge in a challenging market, paving the way for future innovations in casting technologies.
Post time:ඔක්. . 15, 2024 02:51
Next:halaman ng buhangin na nakasuot ng resin