Advantages of Lost Foam Casting
Lost foam casting (LFC) is an innovative manufacturing process that has gained significant attention in recent years due to its numerous advantages over traditional casting techniques. It is particularly valuable in the production of complex parts, including those required in automotive, aerospace, and industrial applications. This article will explore the key benefits of lost foam casting and why it is becoming a preferred method for many manufacturers.
1. Complexity of Design
One of the most notable advantages of lost foam casting is its ability to create highly complex geometries. The process involves creating a foam pattern, which is then coated with a ceramic material and surrounded by sand. Unlike traditional sand casting, which often requires extensive machining to achieve intricate shapes, lost foam casting can directly produce components with complex features, undercuts, and fine details. This allows designers more freedom in their creativity and leads to lighter, more efficient parts.
2. Reduced Material Waste
LFC significantly minimizes material waste, which is a critical factor in today’s environmentally conscious manufacturing landscape. Traditional casting methods often result in a substantial amount of scrap material due to the need for machining and reworking. In lost foam casting, the foam pattern evaporates during the pouring of molten metal, leaving behind an exact cavity in which the metal solidifies. This method ensures that nearly all the material used is transformed into the final product, resulting in a more sustainable process.
3. Improved Surface Finish
The adaptability of the lost foam casting process allows for an improved surface finish on cast parts. The smooth surface of the foam pattern is directly replicated in the final cast product, resulting in reduced or even eliminated need for secondary finishing processes. This not only saves time and labor costs but also enhances the overall aesthetic and functional quality of the parts produced.
4. Faster Production Cycle
advantages of lost foam casting
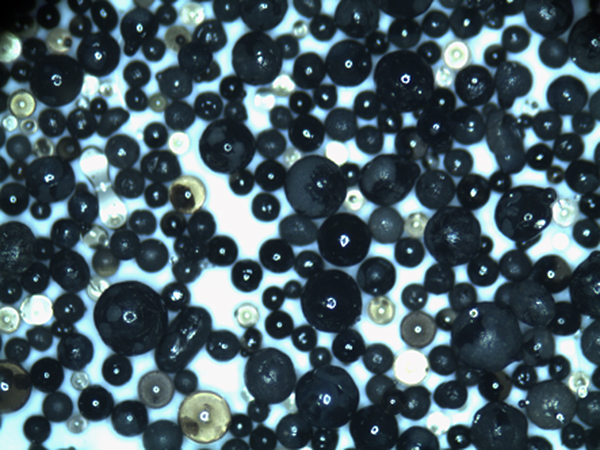
Lost foam casting significantly speeds up the production cycle compared to traditional methods. The simplicity of the process, where no permanent mold is required, accelerates the pattern-making phase. Additionally, the ability to cast multiple parts simultaneously within a single pouring cycle translates to higher throughput and reduced lead times. This is particularly advantageous for industries that require rapid prototyping or have seasonal demands.
5. Cost-Effectiveness
While the initial setup costs for lost foam casting may be higher due to pattern-making and the need for specialized equipment, the overall cost-effectiveness of the process is worth noting. Reduced material waste, less machining, and shorter production times all contribute to lower operational costs. As manufacturers aim to optimize their budgets without compromising quality, LFC offers a viable solution.
6. Versatile Material Compatibility
Lost foam casting is compatible with various metal alloys, making it a versatile option for different applications. From aluminum and iron to complex alloys, the process can be adapted to create parts suitable for diverse environments, including high-temperature applications in the aerospace sector. This flexibility allows manufacturers to choose the most appropriate materials for their specific needs while taking advantage of the lost foam casting technique.
7. Enhanced Mechanical Properties
Lastly, products made using lost foam casting can exhibit superior mechanical properties. The method allows for refined control over the metal cooling process, leading to more uniform grain structures and improved durability in the final product. In demanding applications, this strength and resilience can be a crucial factor, providing a competitive edge to manufacturers.
In conclusion, lost foam casting presents a multitude of advantages that make it an attractive alternative to traditional casting methods. Its ability to produce complex designs, reduce waste, improve surface finish, accelerate production times, and provide versatile material compatibility positions it as a valuable technique in modern manufacturing. As industries continue to innovate, the adoption of lost foam casting is likely to increase, paving the way for more efficient and sustainable production practices.
Post time:දෙසැ. . 15, 2024 05:45
Next:sanding block 3d print