3D Printing for Sand Casting Revolutionizing Manufacturing Processes
In the ever-evolving landscape of manufacturing, technology continues to reshape traditional practices, enhancing efficiency and precision. One of the most compelling advancements in recent years is the integration of 3D printing in sand casting. This innovative fusion represents an evolutionary leap in how castings are produced, enhancing customization, reducing time and costs, and improving overall product quality.
Understanding Sand Casting
Sand casting is a widely used metal casting process that involves creating a mold from sand. The process generally requires a pattern, typically made from metal, wood, or plastic, which is used to form the mold cavity in the sand. Once the pattern is removed, molten metal is poured into the mold to create the final product. This method is favored for its simplicity, cost-effectiveness, and suitability for large-scale productions.
The Role of 3D Printing in Sand Casting
3D printing technology has made significant inroads into various industries, including automotive, aerospace, and consumer goods. When applied to sand casting, it offers a solution to several common challenges. Traditionally, manufacturing patterns can be time-consuming and expensive to produce, particularly for complex designs. However, with 3D printing, manufacturers can create intricate patterns rapidly, allowing for quicker turnaround times and enhanced design flexibility.
One of the most notable benefits of 3D printing in the context of sand casting is the ability to produce complex geometries that are often impossible or prohibitively expensive to achieve using traditional methods. For instance, internal cooling channels in automotive components can be designed with precision using 3D-printed sand molds, leading to improved cooling efficiencies and enhanced performances.
Cost Efficiency and Resource Management
3d printing for sand casting
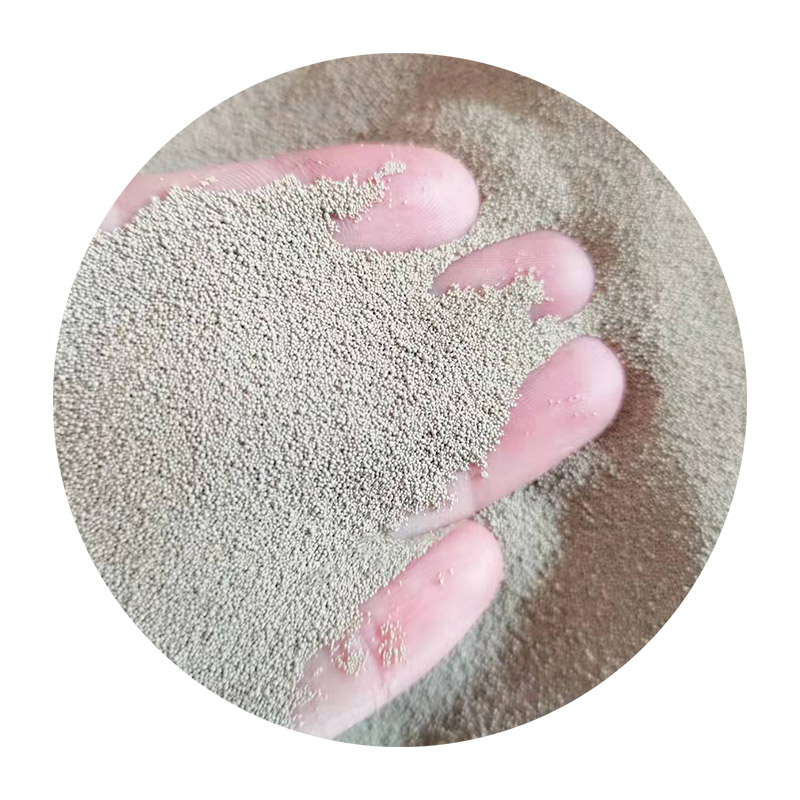
The traditional sand casting process often leads to material wastage, primarily due to the need to create multiple patterns for different castings. 3D printing significantly reduces waste by only using the necessary amount of material to create the mold. Furthermore, the ability to quickly modify designs in software before production allows manufacturers to test multiple iterations without incurring high costs associated with making new physical patterns every time a design needs adjustment.
Additionally, 3D printing enables on-demand production, which eliminates the need for large inventories of patterns. This shift towards lean manufacturing not only reduces storage costs but also promotes a more sustainable production process by minimizing the use of energy and materials.
Quality Improvement
The incorporation of 3D-printed molds in sand casting can lead to superior quality in castings. The high precision of 3D printing minimizes defects typically associated with traditional molds, such as inconsistencies in dimensions and surface finish. Moreover, the ability to create complex, optimized designs leads to stronger and more lightweight castings, which are crucial in industries where material performance is paramount.
The improvement in quality also extends to the reduction of post-processing requirements. With better initial accuracy, castings require fewer adjustments and less machining, saving both time and labor costs.
Future Prospects
As the demand for complex, high-quality components grows across various sectors, the adoption of 3D printing in sand casting is expected to increase significantly. Ongoing advancements in 3D printing technology, particularly in materials that can withstand the rigors of modern manufacturing, will further enhance its viability in sand casting applications.
In conclusion, the intersection of 3D printing and sand casting is poised to revolutionize the manufacturing industry. By offering increased design flexibility, cost savings, resource efficiency, and improved quality, this innovative approach holds the potential to redefine traditional casting processes, making them more adaptable to the ever-changing needs of the market. As technology continues to advance, the future of manufacturing looks not only promising but also uniquely transformative.
Post time:සැප්. . 28, 2024 17:51
Next:cast of sand castles 2014