Types of Sand Casting Process
Sand casting is a widely used manufacturing process that involves creating metal parts by pouring molten metal into a mold made of sand. This method is advantageous due to its cost-effectiveness and the ability to produce complex shapes. The sand casting process is versatile, with various types and techniques tailored to different applications and requirements. In this article, we will explore the primary types of sand casting processes, their characteristics, and their applications.
1. Green Sand Casting
Green sand casting is the most common type of sand casting process. This technique uses a mixture of sand, clay, and water to create molds that can retain their shape under the pressure of molten metal. The term green refers to the fact that the sand is used in its moist state. The advantages of green sand casting include its cost-effectiveness, ease of use, and ability to produce molds relatively quickly. This method is especially popular in foundries that produce large quantities of metal parts, making it suitable for industries like automotive, aerospace, and general manufacturing.
2. Resin Sand Casting
Resin sand casting utilizes a mixture of sand and a thermosetting resin binder. This combination allows for greater precision and strength in the molds compared to green sand casting. The molds produced in this process are harder and can withstand higher temperatures, making them suitable for casting metals like aluminum and iron. Resin sand casting is ideal for producing complex contours and finer details in metal parts, which is advantageous in industries where tight tolerances are critical, such as in the production of engine components or intricate machinery parts.
3
. Sodium Silicate Sand Castingtypes of sand casting process
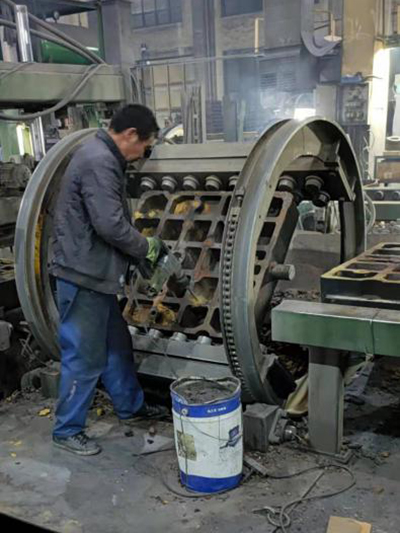
Sodium silicate sand casting is another variation that uses sodium silicate as a binder. This process typically combines sand with sodium silicate and then hardens the mixture through a process called gas curing. The advantage of this method is that it creates molds that are strong and can withstand high temperatures, allowing for complex shapes while retaining the fine details of the original design. Sodium silicate sand casting is often employed in the production of large, heavy metal components needed in construction or heavy machinery.
4. Shell Mold Casting
Shell mold casting is a more advanced sand casting process that uses a thin shell of sand and resin. In this method, a heated metal pattern is used to form a thin shell of sand on the pattern's surface. After the shell hardens, the mold is assembled and filled with molten metal. This technique offers higher accuracy and better surface finishes than conventional sand casting methods. Shell mold casting is often used for medium-sized production runs and is particularly useful in industries that require high precision, such as in the production of pump housings, automotive parts, and small fixtures.
5. Lost Foam Casting
Lost foam casting is a unique sand casting process that involves creating a foam pattern that is coated with sand. The foam pattern is encased in sand, and when molten metal is poured into the mold, the foam evaporates, leaving behind a cavity filled with metal. This method allows for an extremely detailed reproduction of the original shape and eliminates the need for draft angles usually required in traditional patterns. Lost foam casting is an excellent choice for complex parts, particularly in the automotive and aerospace sectors, where weight reduction and intricate designs are critical.
Conclusion
Sand casting is a versatile manufacturing process with various techniques, each offering unique benefits suited for different applications. From green sand casting's cost-effectiveness to the precision of shell mold casting and the innovation of lost foam casting, each type serves a vital role in producing high-quality metal parts. Understanding these different sand casting processes allows manufacturers to select the most suitable method for their specific needs, ensuring efficiency and effectiveness in metal production. As industries continue to evolve, the adaptability and advancements in sand casting will play a significant role in meeting the growing demand for complex, precise components across various sectors.
Post time:Dec . 30, 2024 11:13
Next:foundry sand specifications