Sand Used in Sand Casting
Sand casting is a traditional metal casting process that has stood the test of time due to its versatility, economic feasibility, and effectiveness. Among the various components of this process, sand plays a pivotal role. The type and quality of sand used directly influence the final product's characteristics, including its surface finish, dimensional accuracy, and overall strength. In this article, we will delve into the types of sand commonly used in sand casting, their properties, and the advantages they offer.
Types of Sand in Sand Casting
1. Silica Sand Silica sand is the most widely used sand in sand casting. Comprised primarily of silicon dioxide (SiO2), this sand is abundant, cost-effective, and possesses excellent thermal properties. It can withstand high temperatures without deforming, making it ideal for metal casting processes. The grain size of silica sand can vary, allowing for the production of finer or coarser molds depending on the casting requirements.
2. Green Sand Green sand is a mixture of silica sand, clay, and water. It is called green because it is used in a moist state and has not yet been heated. The clay acts as a binder that holds the grains of sand together, providing the necessary strength and integrity to the mold. Green sand casting is widely used for producing ferrous and non-ferrous castings, and it is known for its ease of use and fine surface finish.
3. Resin-Bonded Sand This type of sand utilizes a resin binder that cures at room temperature or through the application of heat. Resin-bonded sands, such as phenolic resin sand, are designed to produce durable and high-quality molds with excellent dimensional accuracy. The main advantage of this sand is its ability to produce intricate and complex shapes, making it a favorite in industries requiring detailed components.
4. Shell Sand Shell sand is a mixture of sand and thermosetting resin or phenolic resin. This casting method involves creating a thin shell around a pattern using heat. The primary advantage of shell sand is its ability to produce high-strength molds that can withstand high metal pouring temperatures. Additionally, shell sand casts have excellent surface finishes, making them suitable for components where surface appearance is critical.
Properties of Casting Sand
The properties of the sand used in casting have a significant impact on the final casting's performance
. Some essential properties includesand used in sand casting
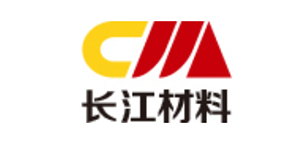
- Grain Shape and Size The shape and uniformity of the sand grains affect mold strength, permeability, and surface finish. Angular grains interlock better, providing strength, while rounded grains offer better flow characteristics.
- Permeability This property allows gases generated during the casting process to escape, preventing defects in the final product. A well-designed sand mixture will balance permeability with strength.
- Moisture Content The correct amount of moisture in the sand mixture is crucial for mold strength and flexibility. Too much moisture may lead to steam explosions, while too little can cause cracking.
- Thermal Conductivity The ability of sand to absorb and dissipate heat affects the cooling rate of molten metal, which influences the final properties of the cast product.
Advantages of Sand Casting
One of the main advantages of sand casting is its cost-effectiveness. The materials required are inexpensive and readily available. Additionally, sand casting allows for the production of large-scale parts as well as small, intricate components. The process is also relatively quick, enabling faster turnaround times compared to other casting methods.
Moreover, sand casting can accommodate a variety of metals, including aluminum, iron, copper, and their alloys. This versatility makes it suitable for various industries, from automotive to aerospace.
In conclusion, the type of sand utilized in sand casting significantly impacts the quality and performance of the final products. The combination of different types of sand and the careful control of their properties allows manufacturers to produce a wide range of components that meet specific requirements. Understanding the role of sand in this timeless casting method continues to be crucial for enhancing efficiency and quality in metal casting processes.
Post time:Oct . 19, 2024 17:13
Next:Kum kası süreci