Metal Sand Casting An Overview
Metal sand casting is one of the most traditional and widely used methods in the metalworking industry. It involves pouring molten metal into a mold made from sand, allowing it to cool and solidify into the desired shape. This technique has a rich history, dating back thousands of years, and continues to be an essential process in various industries, including automotive, aerospace, and art casting. This article explores the fundamental aspects of metal sand casting, its advantages, and its applications.
The Sand Casting Process
The sand casting process starts with the creation of a mold. The mold is typically made from a mixture of sand, clay, and water, which gives the mixture its binding properties. The first step involves creating a pattern, usually made from metal or plastic, which is a replica of the final product. This pattern is then embedded in sand to create a mold cavity.
After the pattern is removed, the mold is formed, consisting of two halves known as the cope (top half) and the drag (bottom half). The two halves are then assembled, and molten metal is poured into the cavity created by the pattern. Once the metal cools and solidifies, the mold is broken apart to reveal the casting. The sand mold can be reused multiple times, making this process cost-effective and efficient.
Advantages of Metal Sand Casting
One of the primary advantages of sand casting is its versatility. It can accommodate a wide range of metals, including iron, aluminum, bronze, and magnesium. Additionally, it can produce intricate shapes and large components, making it ideal for various applications.
Another significant advantage is the ability to create complex geometries. Sand casting allows for better design flexibility compared to other processes like die casting. This flexibility often results in less machining and finishing work, subsequently reducing lead times and costs.
Furthermore, sand casting is ideal for low to medium production volumes. For businesses that do not require mass production, this method can significantly reduce the expense associated with tooling and setup.
metal sand casting
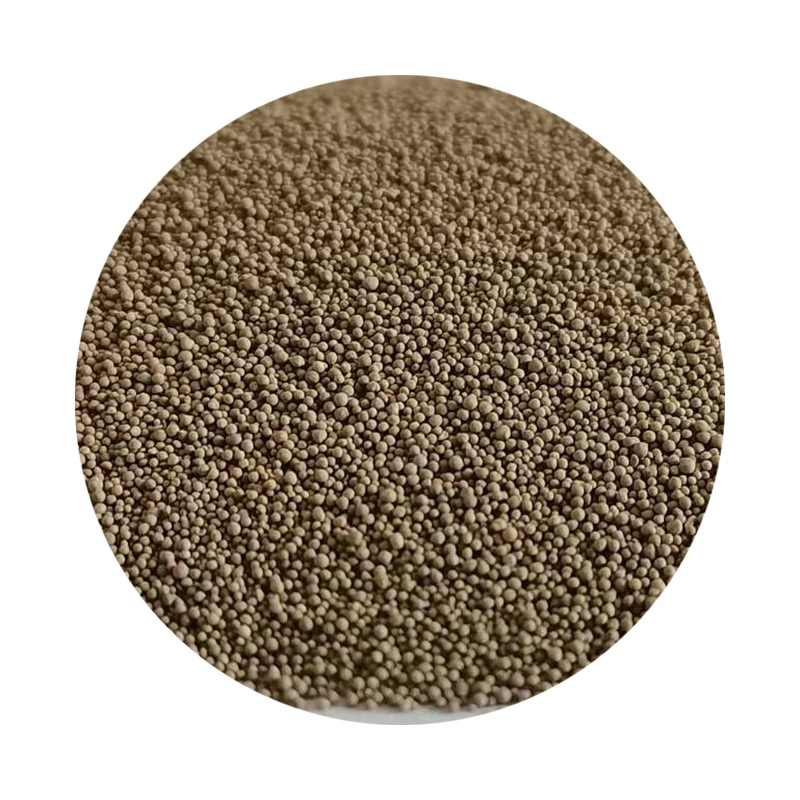
Challenges in Metal Sand Casting
Despite its many advantages, sand casting is not without its challenges. One of the most common issues is achieving dimensional accuracy. Due to the nature of the sand mold and the cooling process, castings can sometimes experience shrinkage or warping. This necessitates additional machining to achieve the required tolerances, which can add time and cost to the production process.
Another challenge is the quality of the surface finish. Castings produced by sand casting may require further surface treatment to improve their finish. This can include processes such as grinding, shot blasting, or coating, which adds to the overall production complexity.
Moreover, the sand used in casting can degrade over time, leading to inconsistencies in mold quality and potential defects in the final product. Regular monitoring and control of the sand mixture are essential to maintain the quality of the molds.
Applications of Metal Sand Casting
Metal sand casting is widely used across different industries for various applications. In the automotive industry, it is essential for producing engine blocks, transmission cases, and other essential components. The aerospace sector also utilizes sand casting for producing turbine casings and structural components that demand high strength and lightweight characteristics.
Moreover, sand casting plays a critical role in the manufacturing of decorative items and sculptures in the art world. Many artists utilize this method to create unique and intricate designs that would be difficult to achieve through other means.
Conclusion
Metal sand casting remains a fundamental process in modern manufacturing despite the advancements in technology and casting methods. Its ability to produce complex shapes, coupled with cost-effectiveness for low to medium production runs, makes it a valuable technique in various industries. While there are challenges to overcome, the continuing refinement of processes and materials will ensure that sand casting holds its place as a cornerstone of metalworking for years to come. Whether in high-tech aerospace components or artistic sculptures, the legacy of metal sand casting endures, illustrating the blend of tradition and innovation in the manufacturing landscape.
Post time:Dec . 22, 2024 22:12
Next:Výroba pískového odlitku krok za krokem