Advantages and Disadvantages of the Sand Casting Process
Sand casting, one of the oldest and most versatile manufacturing processes, involves pouring molten metal into a sand mold to create a desired shape. While it has been a favored method in various industries, understanding its advantages and disadvantages is essential for making informed decisions in metal fabrication.
Advantages of Sand Casting
1. Cost-Effectiveness One of the most significant advantages of sand casting is its cost-effectiveness. The materials used in sand molds, especially sand itself, are relatively cheap and readily available. This makes the initial setup payment lower than alternative processes like investment casting or die casting.
2. Versatility Sand casting is highly adaptable, capable of producing a wide variety of metal parts. This process can accommodate different materials, including aluminium, brass, iron, and steel, making it suitable for countless industrial applications from automotive components to artistic pieces.
3. Complex Shapes Sand casting can create complex geometries that may be challenging for other manufacturing methods. The pliable nature of sand allows for intricate designs with varying wall thicknesses and cavities, making it an excellent choice for engineering applications.
4. Large Size Capability This process can produce large components that might be impractical or impossible to create using other methods. Large metal parts, such as engine blocks or base plates, are frequently produced using sand casting, which can be a significant advantage when size matters.
5. Ease of Production The sand casting process is relatively straightforward and does not require elaborate tooling or machinery. This simplicity allows for quicker adjustments to designs, which is particularly beneficial in prototyping and small batch productions.
6. Good Surface Finish Although the surface finish of castings can vary depending on the quality of the mold, sand casting can achieve an acceptable finish that often requires minimal additional machining. This can reduce further processing times and costs in manufacturing.
advantages and disadvantages of sand casting process
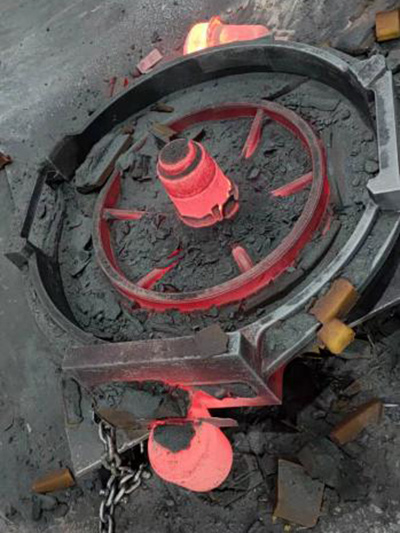
Disadvantages of Sand Casting
1. Limited Dimensional Accuracy While sand casting can produce complex shapes, the dimensional accuracy may not be as high as that achieved with other methods, such as precision investment casting. As a result, parts may require additional machining to meet strict tolerances, thus increasing production time and costs.
2. Surface Finish Quality Although good surface finishes can be achieved, sand casting typically cannot match the smoothness and detail levels seen in other casting processes. Surface defects may occur, requiring post-processing treatments such as grinding or polishing, which can extend lead times.
3. High Labor Intensity Sand casting can be labor-intensive, particularly when creating large and complex molds. The process often requires skilled labor to prepare the molds and manage the pouring of molten metal, resulting in higher labor costs compared to automated processes.
4. Environmental Considerations The use of sand in casting introduces environmental concerns. Silica sand dust generated during cleaning and recycling can pose health hazards to workers. Additionally, spent sand from casting may require careful disposal or treatment to mitigate environmental impacts.
5. Production Speed Although the initial setup is relatively quick, the overall production speed of sand casting is slower than that of other manufacturing processes for high-volume production. Each mold must be created individually, making it less ideal for mass production runs that require rapid manufacturing.
6. Limited Material Choice for Certain Specs Although sand casting can be performed with various metals, some alloys may not perform well in sand casting due to their properties, such as high alloying elements leading to shrinkage issues, making the process unsuitable for specific material applications.
Conclusion
In conclusion, while sand casting remains a popular choice in many engineering sectors due to its cost-effectiveness, versatility, and ability to create complex shapes, it is essential to weigh these benefits against its limitations. Dimensional accuracy, surface finish quality, and environmental considerations are significant factors that should be accounted for when deciding whether sand casting is the appropriate process for a given application. Understanding both the advantages and disadvantages will empower manufacturers to make informed decisions in their production processes, thereby optimizing outcomes for both efficiency and quality.
Post time:Nov . 14, 2024 13:19
Next:sand casting cast iron