Why Sand Casting is Widely Used A Comprehensive Overview
Sand casting, also known as sand mold casting, is one of the oldest and most versatile methods of metal casting. Its enduring popularity can be attributed to a variety of factors, making it a preferred choice for manufacturers across numerous industries. In this article, we will delve into the reasons why sand casting is so widely used, examining its advantages, applications, and the process involved.
Cost-Effectiveness
One of the most significant reasons for the widespread use of sand casting is its cost-effectiveness. The materials required for this process are relatively inexpensive. Sand, which is abundantly available, serves as the primary mold material. This low-cost material enables manufacturers to produce castings at a competitive price point. Furthermore, the process does not typically require expensive machinery or complex tooling, contributing further to its affordability.
Versatility
Sand casting is incredibly versatile. It can accommodate a wide range of metals, including iron, aluminum, bronze, and magnesium, making it suitable for diverse applications. Additionally, it supports the creation of both simple and complex shapes. With the right mold design, manufacturers can produce intricate components that would be difficult or impossible to achieve using other casting methods. This adaptability is crucial in industries such as automotive, aerospace, and art foundries, where varying specifications are common.
Large Scale Production
Sand casting is well-suited for large-scale production runs. It allows for the creation of multiple molds, enabling manufacturers to produce various parts in a single batch. This scalability is particularly advantageous for companies that require high volumes of specific components. Moreover, the use of reusable sand molds can further reduce production costs and time, making it an attractive option for large-scale operations.
Ease of Modification
why is sand casting used
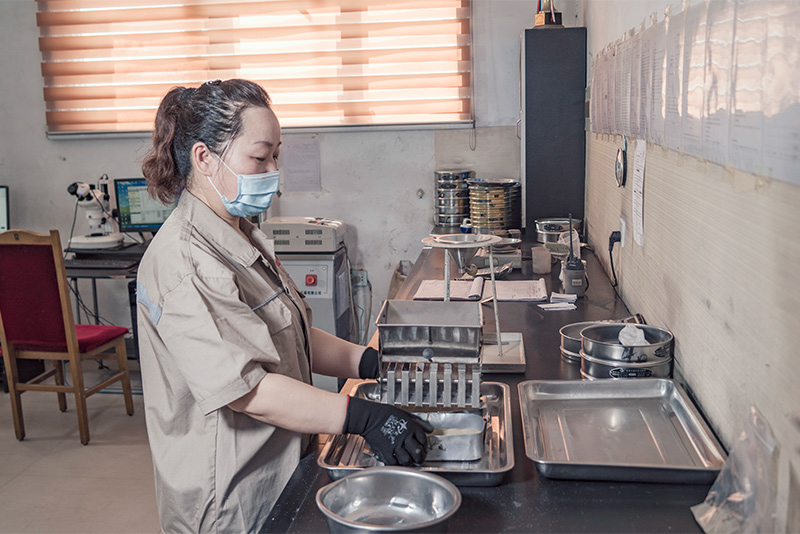
The sand casting process allows for easy modification and flexibility in design. If a design needs to be altered, adjustments can be made relatively quickly and without significant additional cost, unlike permanent molds used in other casting methods. This flexibility is crucial in industries that frequently update their product designs to meet market demands or technological advancements.
Excellent Surface Finish and Tolerance
While sand casting may not provide the same surface finish as some other manufacturing processes, advances in sand casting techniques and materials have significantly improved the quality of the final products. Moreover, with proper preparation and investment in quality raw materials, sand cast products can achieve acceptable surface finishes and tolerances for many applications. This balance between cost and quality makes sand casting a popular choice for both functional and aesthetic components.
Sustainability
Sustainability and environmental considerations are becoming increasingly important in manufacturing processes. Sand casting has a relatively low environmental impact compared to other casting methods, as it generates less waste and allows for the recycling of sand. Additionally, advancements in green sand technologies have further minimized the ecological footprint of sand casting.
Historical Significance and Experience
The long history of sand casting has led to a wealth of knowledge and expertise within the field. The techniques and best practices developed over generations provide manufacturers with confidence in the method’s reliability. New technologies, including computer simulations and 3D printing, continue to enhance sand casting processes, ensuring it remains relevant and efficient in modern manufacturing environments.
Conclusion
In conclusion, the widespread use of sand casting can be attributed to its cost-effectiveness, versatility, ease of modification, and suitability for large-scale production. Its ability to produce both simple and complex shapes while maintaining acceptable quality makes it a preferred choice in various industries. Moreover, as manufacturers increasingly focus on sustainability, sand casting offers an environmentally friendly option that aligns with contemporary manufacturing practices. The combination of historical significance and ongoing technological advancements ensures that sand casting will remain a vital technique in the world of metal fabrication for years to come.
Post time:Дек . 12, 2024 15:08
Next:Innovative Lightweight Aggregates for Sustainable Construction Solutions