Sintering Sand A Key Component in Modern Engineering
Sintering is a vital industrial process that has gained significant attention in recent years, especially in the fields of materials science and engineering. One of the crucial elements in sintering applications is sintering sand, which plays a fundamental role in the production of various engineered products, particularly in metal forming and casting. This article explores the characteristics, applications, and benefits of sintering sand, providing a comprehensive overview of its significance in contemporary manufacturing.
Sintering is the process where powdered materials are compacted and heated to a temperature below their melting point, allowing particles to fuse together. This process enhances the strength and structural integrity of the material, making it suitable for various applications. Sintering sand, primarily composed of silica, is often used as a mold material for metal casting, providing a thermally stable and chemically resistant environment during the sintering process.
One of the primary characteristics of sintering sand is its high melting point and thermal stability. This makes it ideal for high-temperature applications, where traditional materials may fail. Sintering sand is also known for its grain size and distribution, which can be engineered to achieve desired properties such as permeability and flowability. The ability to customize the sand’s characteristics allows engineers to optimize the sintering process, producing higher quality components with improved mechanical properties.
The applications of sintering sand are extensive. It is predominantly used in the foundry industry for casting metals like aluminum, bronze, and iron. During the casting process, sintering sand forms molds that capture the intricate details of the desired final product. Once the molten metal is poured into these molds, the sand supports the shape while allowing gases to escape, preventing defects such as porosity and brittleness in the final casting.
sintering sand
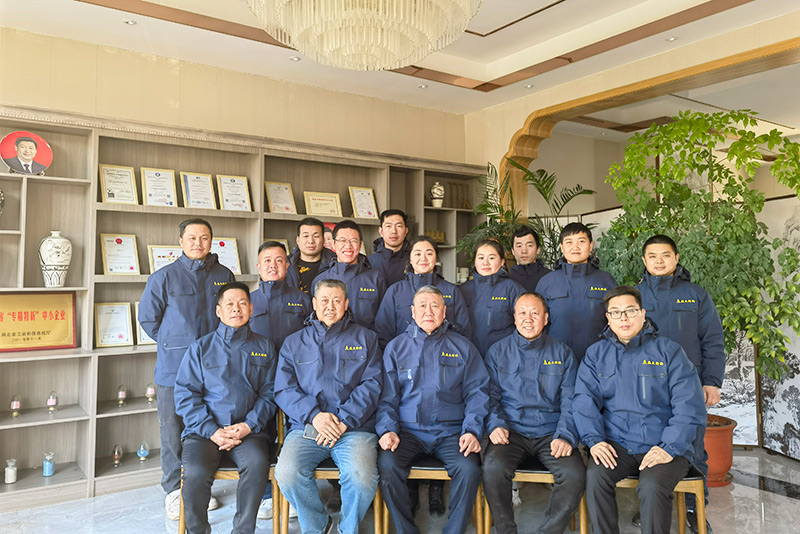
In addition to its use in metal casting, sintering sand has found applications in the production of ceramics and glass. The controlled heating and cooling cycles involved in these processes allow for the precise shaping and fusing of materials, leading to high-quality ceramic tiles, glass products, and other applications. Moreover, sintering sand is also utilized in the production of advanced materials such as composites and biomaterials, which are increasingly used in aerospace and medical applications.
One of the significant benefits of using sintering sand in manufacturing is its recyclability. After the casting process, the sand can be reclaimed, cleaned, and reused for subsequent metal castings. This not only reduces waste but also lowers production costs, making it an economically viable choice for manufacturers. In addition, the ability to reuse sintering sand enhances the sustainability of the manufacturing process, aligning with current environmental standards and practices.
Another advantage of sintering sand is its versatility. By modifying the sand's chemical composition and grain structure, manufacturers can tailor the material’s properties to meet specific needs. This adaptability allows for innovations in manufacturing techniques, enabling engineers to develop new materials and products that may have been deemed impractical previously.
In conclusion, sintering sand is a crucial component in the sintering process, playing a pivotal role in modern engineering and manufacturing. Its unique properties and extensive applications make it indispensable in metal casting, ceramics production, and advanced materials development. As industries continue to seek more efficient and sustainable manufacturing practices, the importance of sintering sand will only continue to grow. With advancements in material science, the future of sintering sand holds the promise of even greater innovations, further enhancing its value in the industrial landscape.
Post time:Дек . 14, 2024 00:30
Next:Innovative Techniques for Using Sand in Resin Crafts and Projects