Sand in Casting A Key Element in Foundry Technology
Casting is a crucial manufacturing process that transforms raw materials into final products through the use of molds. Among various casting methods, sand casting stands out as one of the most widely used techniques in the metalworking industry. This process involves the use of sand as the primary mold material, making it a cost-effective and versatile option for producing metal castings of diverse shapes and sizes. Understanding the role of sand in casting is essential for optimizing production efficiency and ensuring high-quality outcomes.
The Role of Sand in Casting
Sand is primarily used because of its unique properties, which include heat resistance, shape retention, and excellent mold-making characteristics. The most common type of sand utilized in casting is silica sand, which is composed mainly of quartz. Silica sand has a high melting point, which allows it to withstand the tremendous heat generated during the pouring of molten metal without deforming.
The process begins with the creation of a mold. Sand is mixed with a binder, often clay or resin, which helps the sand grains adhere to each other. This mixture is then compacted around a pattern that shapes the interior of the mold. Once the mold is created, the pattern is removed, leaving a cavity that mirrors the desired product's shape. This cavity, along with the sand’s ability to form intricate details, is fundamental in achieving the required accuracy and finish in the final casting.
Advantages of Sand Casting
The advantages of using sand in casting are numerous
1. Cost-Effectiveness Sand casting is less expensive compared to other casting methods. The materials used, primarily sand and binder, are relatively inexpensive, and the process requires minimal setup costs.
2. Versatility Sand casting can accommodate a wide range of materials, including ferrous and non-ferrous metals, making it suitable for various industries. This versatility allows manufacturers to utilize sand casting for everything from small components to large industrial parts.
sand in cast
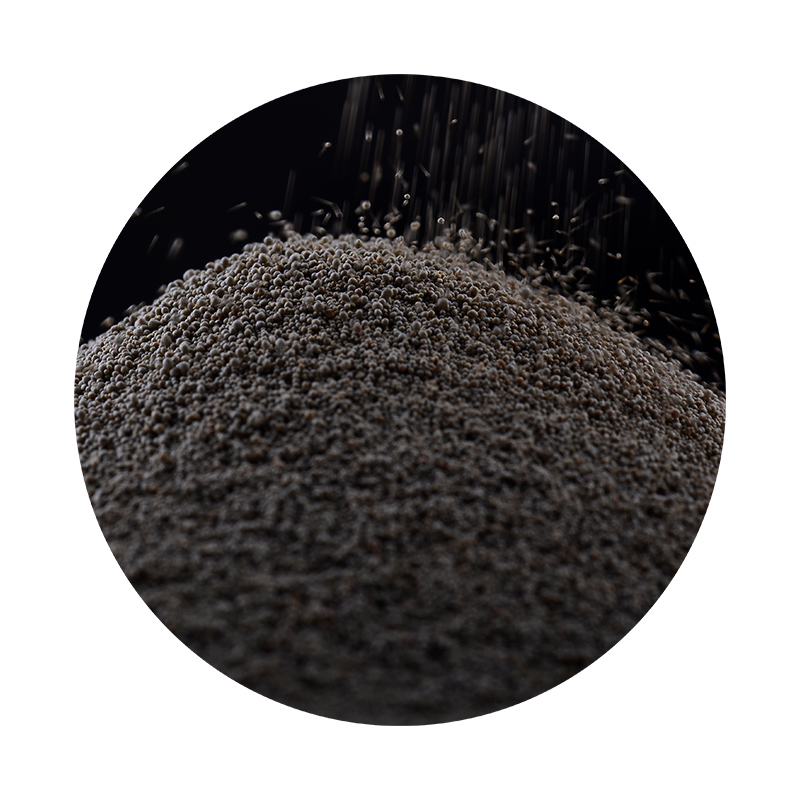
3. Complex Geometries The fluidity of sand allows the production of complex shapes and intricate details that would be challenging to achieve with other materials.
4. Easy to Mold Sand molds can be created relatively quickly, enabling faster production times and more efficient workflows.
5. Reusability While some sand may be lost in the process, used sand can often be reclaimed and reused, making the process more sustainable and environmentally friendly.
Challenges and Considerations
Despite its numerous benefits, sand casting is not without challenges. One of the primary issues is the potential for defects in the final product, such as sand inclusions, surface roughness, or dimensional inaccuracies. Careful control of the sand-to-binder ratio, moisture content, and compaction technique is essential to minimize these defects.
Additionally, the quality of sand plays a significant role in the outcome of the casting process. Factors such as grain size, shape, and purity can influence the final casting’s mechanical properties and surface finish. Therefore, foundries must invest in high-quality materials and rigorous testing to ensure consistency.
Conclusion
In conclusion, sand serves as a fundamental element in the casting process, providing the necessary characteristics to create molds that are both efficient and effective in metalforming. Its cost-effectiveness, versatility, and ability to reproduce complex designs have solidified its position as a preferred choice in the foundry industry. By addressing the challenges associated with sand casting, manufacturers can enhance product quality and production efficiency, ultimately leading to greater innovation and advancement in manufacturing technologies. With ongoing developments in materials science and casting techniques, the future of sand casting looks promising, continuing to play a pivotal role in shaping the products of tomorrow.
Post time:Окт . 12, 2024 14:18
Next:spherical sand