The Art and Science of Sand Castings
Sand casting is one of the oldest and most versatile metal fabrication processes known to humanity. This method, which dates back over 5,000 years, has remained a critical component of modern manufacturing, particularly in the production of complex shapes and large parts. The beauty of sand casting lies in its simplicity, cost-effectiveness, and ability to create intricate designs that other methods might struggle to replicate.
At its core, sand casting involves creating a mold from sand, which is then filled with molten metal to form a desired shape. The process starts with the creation of a pattern, usually made from metal, wood, or plastic, which represents the final part. The pattern is placed in a box, and sand mixed with a binding agent is packed around it. The sand must be compacted tightly to support the weight of the molten metal and to ensure fine detail.
The Art and Science of Sand Castings
The next step in the sand casting process is the melting of metal. Various metals can be used for casting, including aluminum, bronze, and iron, depending on the application's strength and durability requirements. The metal is heated in a furnace until it reaches a liquid state and is then poured into the mold cavity. The temperature and pouring technique are critical, as they influence the final material properties and surface finish.
sand castings
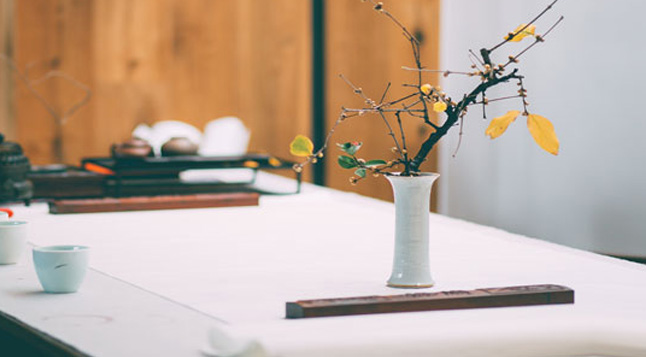
Cooling is the next phase, where the molten metal solidifies within the mold. The cooling rate can significantly impact the microstructure of the metal, affecting its strength and hardness. Typically, thicker sections cool slower than thinner sections, leading to potential defects such as porosity or uneven grain structure. Therefore, careful control of the cooling process is essential.
After the metal has solidified, the mold is broken apart to reveal the casting. This is often done with brute force, though more sophisticated methods exist, like vibration or mechanical means. Once the casting is extracted, it typically requires some finishing work. This can include grinding, sandblasting, or machining to achieve the desired surface finish and dimensions. The finishing process is crucial as it can affect the performance and aesthetics of the final product.
One of the key advantages of sand casting is its adaptability. The method is suitable for low to high production volumes, making it an ideal choice for prototypes and small batch productions, as well as larger-scale manufacturing. The ability to work with a variety of metals and create complex geometries further enhances its versatility. Moreover, sand casting is often more economical than other methods, such as die casting, especially when it comes to producing large parts or lower volumes.
However, the sand casting process also comes with its share of challenges. Sand casting may produce a rough surface finish compared to other casting methods, and it is more prone to defects such as inclusions or air pockets. Additionally, achieving tight tolerances can be more difficult, which sometimes necessitates additional machining processes.
In conclusion, sand casting remains a fundamental technique in the world of manufacturing, blending both art and science. It offers a unique combination of flexibility, cost-effectiveness, and capability that meets diverse industrial needs. Whether for creating intricate parts in the automotive sector or crafting artistic sculptures, sand casting is a process that not only opens doors for innovation but also honors the craftsmanship developed over millennia. As technology advances and new materials are continuously developed, one thing remains certain the legacy of sand casting will endure, evolving alongside modern manufacturing practices while continuing to serve as a cornerstone of metal fabrication.
Post time:Ноя . 12, 2024 13:28
Next:how to wet sand 3d prints