The Art and Science of Sand Cast Foundry
Sand casting, one of the oldest and most versatile metal casting processes, has been a fundamental method for shaping materials since ancient times. The process involves creating a mold from sand to produce metal components, showcasing a seamless blend of artistry and engineering. In this article, we will explore the intricacies of sand cast foundry, its advantages, applications, and the future of this enduring craft.
At the heart of sand casting lies the creation of a mold. The process starts with the preparation of sand, usually mixed with a binding agent such as clay or resin. The sand mixture is then compacted into a pattern, which serves as a template for the mold. Patterns can be made from various materials, including wood, metal, or plastic, and can be designed to reflect both intricate details and larger, simple shapes.
Once the mold is formed, molten metal—often aluminum, iron, or bronze—is poured into the cavity created by the pattern. The metal cools and solidifies, taking the shape of the mold. After cooling, the sand mold is broken away to reveal the final cast metal piece. This method allows for high volumes of production while accommodating complex geometries that other casting processes may struggle to replicate.
One of the primary advantages of sand casting is its versatility. It can accommodate a wide range of metals and alloys, making it suitable for various applications. Industries such as automotive, aerospace, and construction have long relied on sand cast foundries to produce parts ranging from simple brackets to intricate engine components. Additionally, sand casting can be employed for both small-scale production and large-scale manufacturing, allowing businesses to cater to diverse market demands.
sand cast foundry
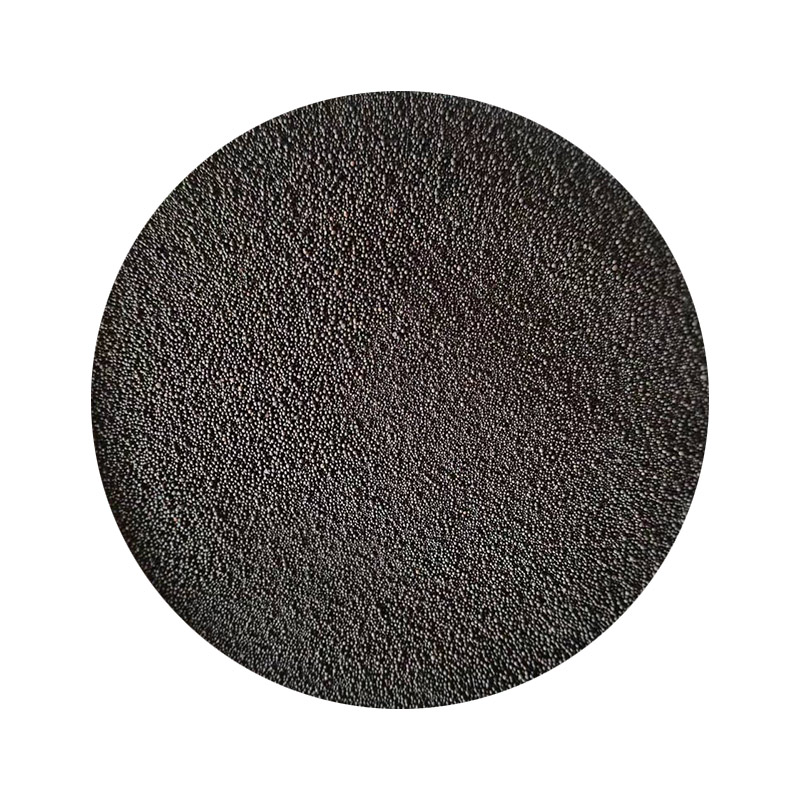
Another notable benefit of sand casting is its cost-effectiveness. The materials used in the process—primarily sand and metal—are relatively inexpensive and widely available. Furthermore, the process itself does not require elaborate machinery or tooling, making it accessible to small businesses and artisans alike. This ease of access has contributed to the ongoing popularity of sand casting as a means of creating custom parts and prototypes.
However, sand casting is not without its challenges. The quality of the finished product can be influenced by the consistency of the sand mixture, the design of the mold, and the pouring technique. Additionally, surface finish is often less smooth compared to other casting methods, which may require further machining or finishing. Nonetheless, many modern foundries have implemented advanced technologies and practices to enhance mold quality, reduce defects, and improve overall efficiency.
Looking ahead, the future of sand cast foundry appears promising. Innovations in materials science, such as the development of synthetic sands and advanced binders, are poised to improve mold performance and longevity. Moreover, the integration of digital technologies, including computer-aided design (CAD) and 3D printing, is transforming the way molds are created and optimized, leading to better precision and faster production cycles.
In conclusion, sand cast foundry remains a vital component of the manufacturing landscape, drawing on its rich history while embracing modern techniques. As industries continue to evolve, the adaptability, cost-effectiveness, and versatility of sand casting ensure that it will remain a preferred method for producing metal parts for years to come. The intersection of tradition and innovation in sand casting not only preserves its heritage but also secures its relevance in an ever-changing world.
Post time:Ноя . 19, 2024 18:26
Next:super sand magic