Understanding Metal Casting Sand Its Importance and Types
Metal casting is a vital process in manufacturing, wherein molten metal is poured into molds to create various components and products. One of the critical materials used in this process is casting sand. This article explores the significance of casting sand, its characteristics, and the different types available in the industry.
The Role of Casting Sand
Casting sand serves as the primary material to create molds in the metal casting process. Its primary function is to form the mold cavity that holds the molten metal until it solidifies into the desired shape. The quality of the sand directly affects the surface finish and dimensional accuracy of the final product. Thus, choosing the right type of sand is essential for achieving optimal results in casting.
Characteristics of Quality Casting Sand
For casting sand to be effective, it must possess certain key characteristics
1. Grain Size The sand grains should be of appropriate size to ensure good flowability and compaction, leading to accurate mold formation. 2. Refractoriness It must withstand high temperatures without breaking down, ensuring the mold retains its shape despite the heat from the molten metal.
3. Bonding Properties Good casting sand must have sufficient bonding capacity to hold its form when compacted, preventing sand from collapsing into the mold cavity.
5. Moisture Content The proper balance of moisture is crucial, as too much or too little can weaken the mold and affect the casting outcome.
metal casting sand
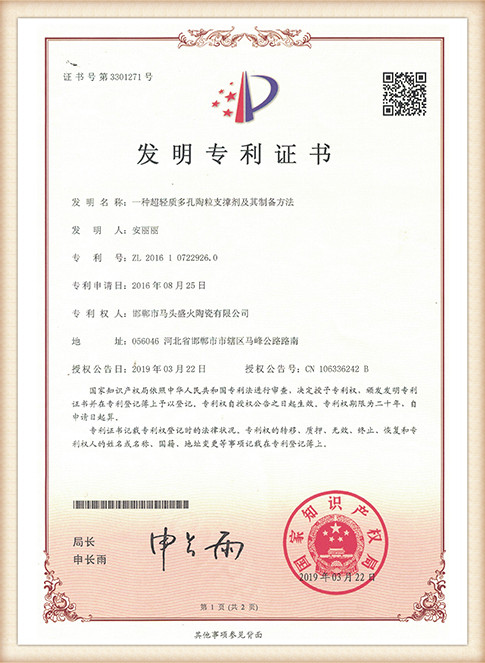
Types of Casting Sand
Various types of casting sand are used in the industry, each with specific properties suited for different applications
1. Silica Sand The most common type of casting sand, silica sand has high refractoriness and excellent permeability. It is widely used in ferrous and non-ferrous metal casting.
2. Green Sand This is a mixture of silica sand, clay, and water. It is called green because it contains moisture. Green sand molds are easy to make and maintain but require careful handling due to their weaker structure compared to dry molds.
3. Dry Sand This type refers to sand that has been dried and contains no moisture. It offers higher strength and is used for molds that require intricate designs.
4. Shell Molding Sand Comprised of a mixture of sand and thermosetting resin, this type creates thin shells around a pattern. It is excellent for producing complex shapes with high dimensional accuracy.
5. Investment Casting Sand Used in investment casting processes, this sand is often mixed with a binder to create precise molds. Investment casting is employed for intricate designs and high-quality surface finishes.
Conclusion
In conclusion, metal casting sand plays an integral role in the casting process, directly influencing the quality of the final product. Understanding the various types, their properties, and the critical characteristics of quality casting sand can lead to better decision-making in the foundry. By selecting the appropriate type of sand, manufacturers can enhance production efficiency, lower costs, and ultimately achieve superior results in metal casting. As industries continue to evolve, advancements in casting sand technology will likely lead to new possibilities in manufacturing.
Post time:Ноя . 02, 2024 09:27
Next:china sand casting