Advantages of the Sand Casting Process
Sand casting is one of the oldest and most versatile metal casting processes utilized in the manufacturing industry. This method involves the use of sand as a mold material to form complex shapes and structures from molten metal. Despite the emergence of various modern casting techniques, sand casting remains popular due to its numerous advantages. This article delves into the myriad benefits of the sand casting process, highlighting why it continues to be a preferred choice for manufacturers.
1. Cost-Effectiveness
One of the most significant benefits of sand casting is its cost-effectiveness. The primary materials used in the process, namely sand and suitable binders, are relatively inexpensive compared to other materials used in more advanced casting methods. Furthermore, the equipment required for sand casting, such as sand molds, is also affordable and less intricate. This affordability makes sand casting an ideal choice for small-scale productions or for companies that are just starting out.
2. Versatility
Sand casting is highly versatile and can accommodate a wide range of metals, including aluminum, copper, magnesium, and iron. This adaptability is beneficial for various applications in industries such as automotive, aerospace, and art. Moreover, sand casting can easily produce complex shapes and sizes, allowing manufacturers to create intricate designs that may be challenging to achieve with other casting methods.
3. Ability to Create Large Parts
The sand casting process is particularly well-suited for producing large parts and components. Unlike other casting techniques, which may have limitations on the size of the mold, sand casting can create molds of virtually any size. This capability makes it invaluable for industries that require substantial components, such as heavy machinery and infrastructure.
The surface finish of sand-cast products can be remarkably good, especially when using high-quality sand and advanced techniques. While not as smooth as die-cast products, the surface finish of sand castings can be enhanced through various finishing processes like grinding, polishing, or shot blasting. Additionally, sand casting allows for creative expressions with textures and patterns, making it favorable for artistic endeavors and decorative items.
advantages of sand casting process
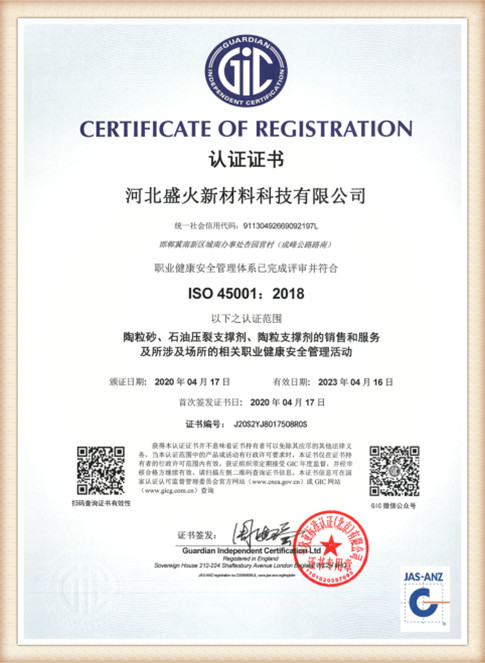
5. Quick Production Time
Sand casting offers relatively fast production times when compared to other casting methods. Patterns can be reused multiple times, enabling efficient production cycles. The sand used in the molds can be easily recycled and prepared for reuse in subsequent batches, minimizing waste and maximizing productivity. This quick turnaround is particularly advantageous in industries that require rapid prototyping and production runs.
6. Ease of Modification
Once a mold is created, modifications can be made easily should the design need adjustments or improvements. This flexibility minimizes the risk associated with new product development, as changes can be implemented without an overly complicated retooling process. This ease of modification makes sand casting ideal for startups and companies engaged in research and development.
7. Environmentally Friendly Options
Increasingly, the sand casting industry is adopting more environmentally friendly practices. Many foundries are now utilizing sustainable materials and recycling sand, reducing environmental impact significantly. The use of natural sand and the recycling of materials will likely continue, aligning with the growing global emphasis on sustainability and eco-friendly manufacturing practices.
8. Low Production Setup Costs
Establishing a sand casting operation requires a lower initial investment compared to other casting processes. Simple molds can be made without specialized tooling, allowing businesses to begin production relatively quickly and at a lower cost.
In summary, the advantages of the sand casting process—including cost-effectiveness, versatility, the ability to produce large parts, distinctive surface finishes, quick production times, ease of modification, environmentally friendly practices, and low setup costs—make it a staple in the manufacturing world. As industries continue to evolve, the relevance of sand casting remains strong, proving its resilience and adaptability in a constantly changing market. Understanding these benefits is crucial for manufacturers considering the most suitable casting method for their production needs.
Post time:Ноя . 24, 2024 10:55
Next:lost foam castings