3D Printing for Sand Casting Revolutionizing Traditional Manufacturing
In recent years, the manufacturing industry has undergone a transformative shift due to advances in technology. One of the most groundbreaking innovations is the integration of 3D printing into traditional processes, particularly in sand casting. This article explores how 3D printing is revolutionizing sand casting, enhancing efficiency, reducing costs, and offering unprecedented design freedom.
Understanding Sand Casting
Sand casting is one of the oldest and most widely used metal casting processes. It involves creating a mold from sand to shape liquid metal into desired forms. Traditionally, this process is time-consuming and labor-intensive, requiring skilled artisans to create complex patterns. Moreover, the production of patterns can take days or even weeks, which can be a significant setback for companies needing quick turnarounds.
The Role of 3D Printing
Enter 3D printing, which has emerged as a game-changer in the manufacturing landscape. By utilizing additive manufacturing techniques, designers can create intricate patterns directly from digital files. This approach drastically reduces the time and effort required to produce molds for sand casting. Instead of crafting a physical model from materials like wood or metal, manufacturers can simply design the required pattern using computer-aided design (CAD) software and print it in a matter of hours.
3D printing offers enhanced precision, allowing for complex geometries that are nearly impossible to achieve with traditional methods. This capability is particularly beneficial in industries such as aerospace and automotive, where lightweight and complex designs are paramount.
Benefits of 3D Printing in Sand Casting
1. Speed and Efficiency One of the most significant advantages of 3D printing is its speed. Creating a sand mold using traditional methods can take weeks, but with 3D printing, this time is reduced to just hours. Industries can respond more quickly to market demands, facilitate rapid prototyping, and optimize their production processes.
3d printing for sand casting
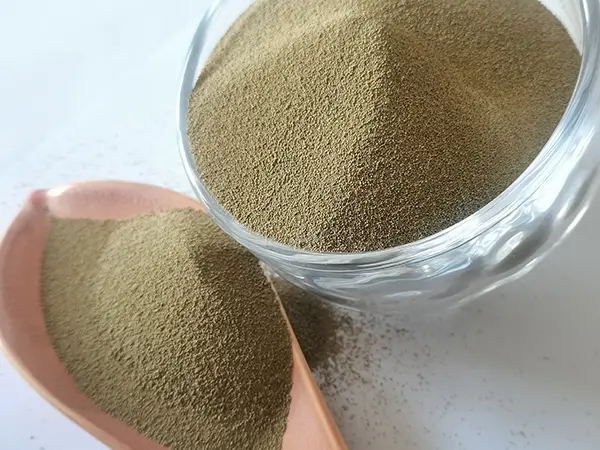
2. Cost Reduction The initial investment in 3D printers and materials can be substantial, but the long-term savings are significant. Companies can drastically reduce material waste since 3D printing is additive rather than subtractive. Additionally, by lowering labor costs associated with traditional pattern-making, organizations can improve their overall profitability.
3. Design Flexibility 3D printing allows for an unprecedented level of design freedom. Complex features such as internal geometries, cooling channels, or intricate surface textures can be easily incorporated into the design. This flexibility opens new avenues for innovative product development, enabling engineers to experiment with designs that were once considered impractical.
4. Customization In an era where personalization is key, 3D printing facilitates the customization of products. Manufacturers can produce small batches of unique designs without the need for extensive retooling or changeovers. This capability is particularly useful for industries that require tailored solutions, such as medical devices or specialized machinery.
5. Sustainability As industries move towards more sustainable practices, 3D printing aligns with eco-friendly initiatives. By reducing material waste and energy consumption, manufacturers can lower their carbon footprint. Furthermore, the ability to use recycled materials in the 3D printing process contributes to a more sustainable production model.
Challenges Ahead
Despite its advantages, the integration of 3D printing into sand casting is not without challenges. The initial costs of equipment and materials can be high, and there is a learning curve for personnel to become proficient in new technologies. Additionally, ensuring the quality and mechanical properties of 3D-printed molds requires ongoing research and development.
Moreover, as 3D printing technology continues to evolve, regulatory concerns regarding material safety and production standards will need to be addressed, ensuring that products consistently meet industry requirements.
Conclusion
The convergence of 3D printing and sand casting is a prime example of how technology can enhance traditional manufacturing processes. By improving efficiency, reducing costs, and enabling design freedom, 3D printing offers significant advantages that can help companies stay competitive in an increasingly demanding market. As the technology matures and integration hurdles are overcome, the future of sand casting, bolstered by 3D printing, looks promising—ushering in a new era of innovation in metal manufacturing.
Post time:Окт . 17, 2024 03:52
Next:why sand casting is preferred