Types of Sand Used in Sand Casting
Sand casting is a versatile and widely used manufacturing process in which molten metal is poured into a mold made from a mixture of sand and additives. The choice of sand is crucial, as it directly affects the quality and precision of the final product. In this article, we will delve into the types of sand commonly used in sand casting, their characteristics, and their suitability for different applications.
1. Green Sand
Definition Green sand is a mixture of silica sand, clay, and moisture. It is called green not because of its color, but because it is used in its natural state without any additional heat treatment.
Composition The typical composition of green sand includes about 70% silica sand, 15% clay (usually bentonite), and 15% water. The clay acts as a binder to hold the sand grains together, while the moisture provides workability.
Advantages Green sand is popular due to its excellent molding properties, reusability, and good dimensional accuracy. It can absorb moisture and expands without cracking, making it ideal for intricate designs.
Applications This type of sand is commonly used to cast ferrous and non-ferrous metals in various industries, including automotive and aerospace.
2. Shell Sand
Definition Shell sand casting involves the use of a resin-bonded sand, typically composed of fine silica sand and a thermosetting resin that hardens when heated.
Composition Shell sand is prepared by mixing sand with resin and curing it in a heated shell mold. The mold is created by applying the mixture onto a heated metal pattern.
Advantages One of the significant benefits of shell sand is its ability to produce excellent surface finishes and high dimensional accuracy. The rapid curing also allows for faster production cycles.
Applications Shell sand is often employed for casting small to medium-sized metal components where high precision is required, such as in the production of pump housings, turbocharger components, and intricate parts in machinery.
3. Resin Sand
Definition Resin sand is another form of sand casting that uses a mixture of sand and a resin binder
. Unlike shell sand, resin sand molds remain solid at room temperature until they are heated.Composition This type of sand typically combines silica sand with an organic resin (such as phenolic or furan resin), which hardens when mixed with a hardener.
what type of sand is used for sand casting
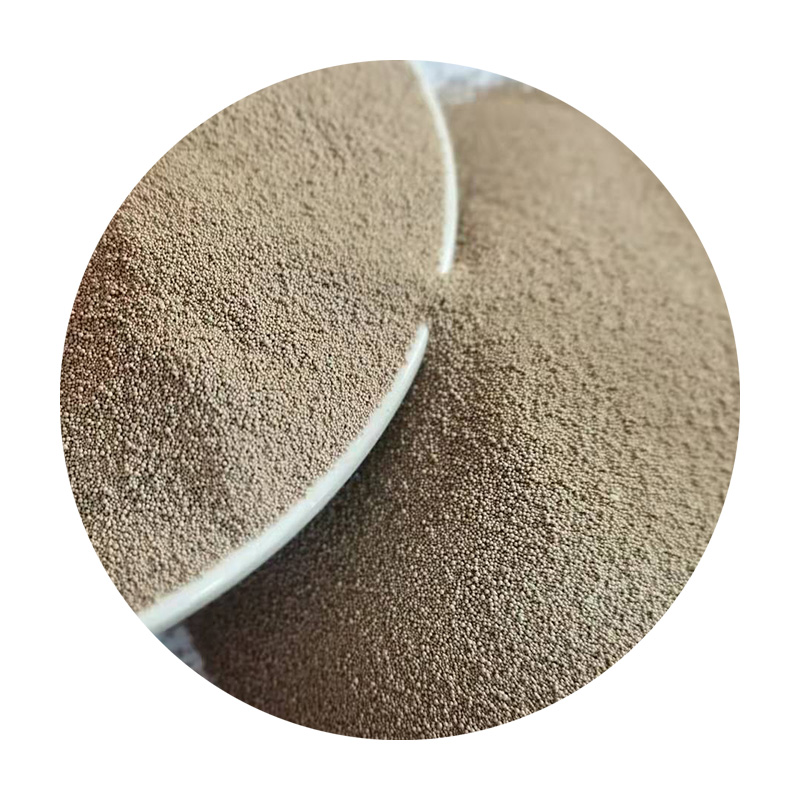
Advantages Resin sand offers exceptional strength and allows for detailed casting with smooth surface finishes. It has a longer shelf life and lower moisture absorption, leading to reduced defects in the castings.
Applications Resin sand is well-suited for casting complex shapes and is often used in the foundry industry for producing high-quality metal products, including valve bodies, housings, and artistic sculptures.
4. Coated Sand
Definition Coated sand is a specialized type of sand used primarily in high-performance applications. It is typically coated with a thin layer of resin or other binding materials.
Composition The sand is treated with a coating agent that enhances its properties, improving flowability and reducing the chances of defects during the casting process.
Advantages Coated sand exhibits excellent thermal stability and can withstand higher temperatures. It is also capable of producing very detailed and intricate castings with minimal finishing required.
Applications This sand is mainly used in industries where high-quality castings are paramount, such as aerospace and defense.
5. Zircon Sand
Definition Zircon sand is used less commonly in sand casting. It is made from zirconium silicate and is valued for its unique properties.
Composition Zircon sand can withstand high temperatures without deforming. It also exhibits good thermal conductivity and low expansion, making it ideal for intricate shapes.
Advantages Its use can lead to improved surface finish and reduced inclusions in the final product.
Applications Zircon sand is particularly useful in applications that require high precision and durability, such as core making for turbine blades and other critical components.
Conclusion
The type of sand chosen for sand casting can dramatically influence the overall quality, durability, and accuracy of the casted parts. Each type of sand has unique properties that make it suitable for specific applications. Whether it is green sand for general use, shell sand for high precision, or resin sand for intricate designs, selecting the right sand is key to achieving successful casting results. As the manufacturing industry continues to evolve, enhanced materials and methods will further refine the casting processes, ensuring even greater performance and efficiency in the future.
Post time:oct. . 17, 2024 08:55
Next:Understanding the Resin Sand Casting Process and Its Applications in Modern Manufacturing