What is Sand Casting?
Sand casting, also known as sand mold casting, is a versatile and widely-used metal casting process. It involves using sand as the mold material to shape molten metal into desired forms. This method dates back thousands of years, and its simplicity and effectiveness have made it a preferred choice in various industries, including automotive, aerospace, and artistic applications. In this article, we will delve into the intricacies of sand casting, discussing its process, advantages, disadvantages, and applications.
The Sand Casting Process
The sand casting process can be broken down into several key steps
1. Pattern Making The first step in sand casting involves creating a pattern, which is a replica of the object to be cast. Patterns are typically made from materials such as wood, metal, or plastic. The pattern must account for shrinkage and other factors that affect the final product.
2. Mold Creation The pattern is then used to create a mold in sand. The sand is mixed with a bonding agent, usually clay, and then compacted around the pattern. Once the sand is compacted, the pattern is carefully removed, leaving a hollow cavity in the sand that matches the shape of the intended casting.
3. Core Making (if necessary) For more complex shapes, cores may be created and placed inside the mold. Cores are additional sand structures that form internal cavities or features within the final casting.
4. Pouring Molten Metal Once the mold is prepared, molten metal—typically aluminum, copper, iron, or bronze—is poured into the mold cavity. The metal fills the space, taking the shape of the mold.
5. Cooling and Solidification After pouring, the molten metal cools and solidifies. This process can take anywhere from a few minutes to several hours, depending on the size and type of metal used.
6. Mold Removal Once the metal has cooled, the sand mold is broken away, revealing the cast object. This is often accomplished by shaking or knocking the mold apart.
7. Finishing The final step involves cleaning up the casting. This may include removing excess material, smoothing surfaces, and performing any necessary machining to achieve the desired specifications.
Advantages of Sand Casting
Sand casting offers several benefits that contribute to its popularity across various industries
- Cost-Effective The materials used in sand casting are relatively inexpensive, making it a cost-effective option for producing metal parts, especially in low to moderate production runs.
- Versatility Sand casting can accommodate a wide range of metals and alloys, as well as different sizes and shapes. This versatility allows it to be used for everything from small components to large machinery parts.
what is a sand casting
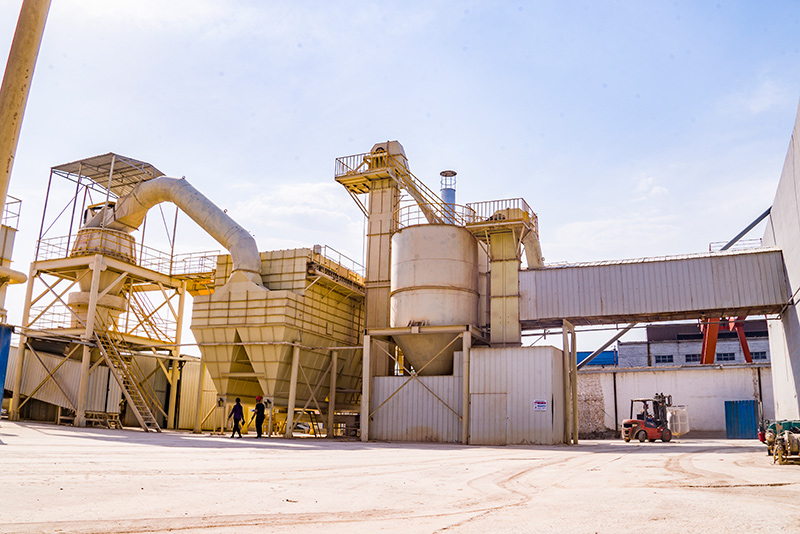
- Complex Geometries The process can create complex shapes and intricate designs that would be challenging or impossible to achieve with other casting methods
.- Ease of Production The sand casting process is relatively straightforward, allowing for quick setup and faster production times, especially for small batch production.
Disadvantages of Sand Casting
Despite its advantages, sand casting does have some drawbacks
- Surface Finish The surface finish of sand-cast components is typically not as smooth as that achieved through other methods, such as investment casting. This means additional finishing operations may be required.
- Dimensional Tolerance Sand casting can result in less precise dimensions compared to other casting techniques, which may require further machining, especially for components with tight tolerances.
- Labor-Intensive The process can be labor-intensive, especially when creating cores or more complex mold designs, which can increase production time and costs.
Applications of Sand Casting
Sand casting is used in a variety of applications, including
- Automotive Components Many automotive parts, such as engine blocks, transmission cases, and cylinder heads, are produced using sand casting.
- Aerospace Components Certain aerospace parts, particularly those made from high-strength alloys, are cast using this method.
- Artistic Creations Artists and sculptors often utilize sand casting to create intricate metal sculptures and decorative items.
Conclusion
In conclusion, sand casting is a time-tested and effective metal casting method that is widely used across various industries. Its affordable materials, versatility, and ability to produce complex geometries make it an attractive option for many applications. However, it is essential to consider its limitations, such as surface finish and dimensional tolerances, when choosing the most suitable casting method for a specific project. As technology advances, the sand casting process continues to evolve, maintaining its relevance in modern manufacturing and artistry.
Post time:dec. . 11, 2024 03:22
Next:Exploring the Benefits of Coated Sand Casting in Modern Manufacturing Techniques