Types of Sand in Foundry An Overview
In the foundry industry, sand is one of the primary materials used in the production of castings. The type of sand selected for a particular application plays a critical role in the quality of the finished product. Understanding the different types of sand used in foundries is essential for ensuring the desired properties in castings, optimizing production processes, and minimizing defects. This article provides an overview of the various types of sand commonly utilized in foundries, highlighting their characteristics, advantages, and applications.
1. Silica Sand
Silica sand is perhaps the most widely used type of sand in foundries. Comprised mainly of silicon dioxide (SiO2), silica sand is appreciated for its high melting point, thermal stability, and availability. It is commonly used in the production of molds and cores due to its ability to withstand high temperatures without breaking down. Additionally, silica sand can be processed to enhance its specific properties, making it suitable for various casting techniques such as green sand molding and resin sand molding.
One major advantage of silica sand is its ability to provide excellent surface finishes to castings, as it can easily conform to the details of the pattern. However, one must exercise caution when working with silica sand due to the potential health risks associated with respirable crystalline silica dust.
2. Chromite Sand
Chromite sand is derived from chrome ore and is widely used in foundries, particularly for steel and iron castings. Its unique composition provides several benefits, including excellent thermal stability and low thermal expansion, which make it ideal for high-temperature applications. Chromite sand is less prone to fusion at casting temperatures, thus reducing the risk of defects caused by sand sticking to the casting surfaces.
Additionally, chromite sand is known for providing good resistance to metal penetration, which is crucial for maintaining the integrity of complex patterns and intricate designs in molds. Its relatively high cost compared to silica sand is often justified by the superior quality it imparts to castings.
types of sand in foundry
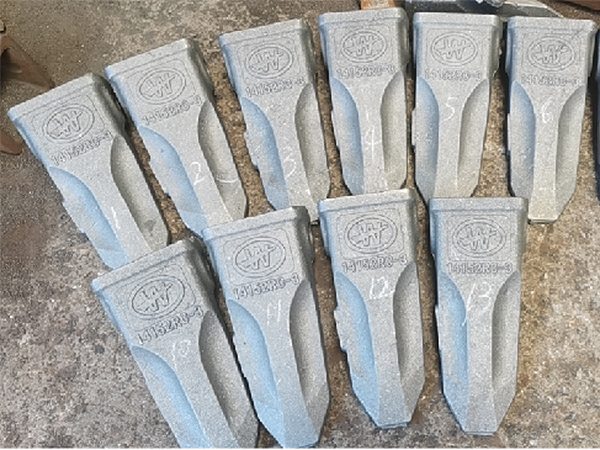
3. Zircon Sand
Zircon sand, obtained from zirconium silicate (ZrSiO4), is another premium material used in foundry applications. It is especially prized for its high melting point and chemical inertness. Zircon sand exhibits low thermal expansion, which is beneficial for precise mold dimensions. It is often employed in applications that require high integrity and dimensional stability, such as for casting turbine components or in the aerospace industry.
The primary drawback of zircon sand is its cost, which is significantly higher than that of silica sand. Nevertheless, its superior performance in high-stress applications makes it a preferred choice in specialized foundries.
4. Olivine Sand
Olivine sand is composed of the mineral olivine (Mg2SiO4) and is often regarded as a more eco-friendly alternative to traditional foundry sands. It has good thermal characteristics, low thermal expansion, and excellent resistance to molding deformation. Olivine sand is particularly effective in ferrous casting processes and is gaining popularity due to its sustainability and reusability.
The use of olivine sand can also mitigate the health risks associated with crystalline silica dust, making it a safer option for foundry workers.
Conclusion
Understanding the various types of sand used in the foundry industry is essential for producing high-quality castings while optimizing the foundry processes. Each type of sand has distinct advantages and applications, and the choice of sand should align with the specific requirements of the casting process. While silica sand remains the most popular due to its availability and cost-effectiveness, specialty sands like chromite, zircon, and olivine offer unique benefits that can enhance the performance of castings in demanding applications. By selecting the appropriate type of sand, foundries can improve production efficiency, reduce defects, and ultimately deliver superior products to their customers.
Post time:dec. . 19, 2024 14:04
Next:can i sand resin