Sand Casting Procedure A Comprehensive Overview
Sand casting, also known as sand mold casting, is one of the oldest and most widely used metal casting processes. The method involves the use of sand as the primary mold material, making it versatile and suitable for a range of materials including aluminum, iron, and bronze. This process features several distinct stages, each crucial for achieving the desired quality and integrity of the final product. Below is a comprehensive overview of the sand casting procedure.
1. Pattern Making
The first step in the sand casting process is creating a pattern. A pattern is a replica of the object to be cast, typically made from materials like wood, metal, or plastic. The pattern's dimensions must be slightly larger than the finished product to account for shrinkage that occurs during solidification. Patterns can be single, split, or complex depending on the casting design, and they often include various features, such as core prints, which are necessary for creating internal cavities.
2. Preparing the Mold
Once the pattern is ready, the next step is preparing the mold. The mold is created using two halves—often referred to as the cope (top) and drag (bottom). Fine sand, mixed with a binder (often clay) and water, is poured around the pattern in a mold box. The mixture is then compacted to form a solid mold. Afterward, the pattern is carefully removed, leaving the negative cavity that will receive the molten metal. In some cases, cores made of sand are also used to create internal features within the cast.
3. Melting the Metal
Next, the metal to be cast is prepared. Depending on the specifications, various alloys may be used. The metal is melted in a furnace, reaching temperatures that allow it to become liquid. Different metals require different melting points; for example, aluminum melts at around 660°C, while iron melts at approximately 1200°C. Ensuring the metal is uniformly heated is critical for avoiding defects in the final product.
4. Pouring
sand casting procedure
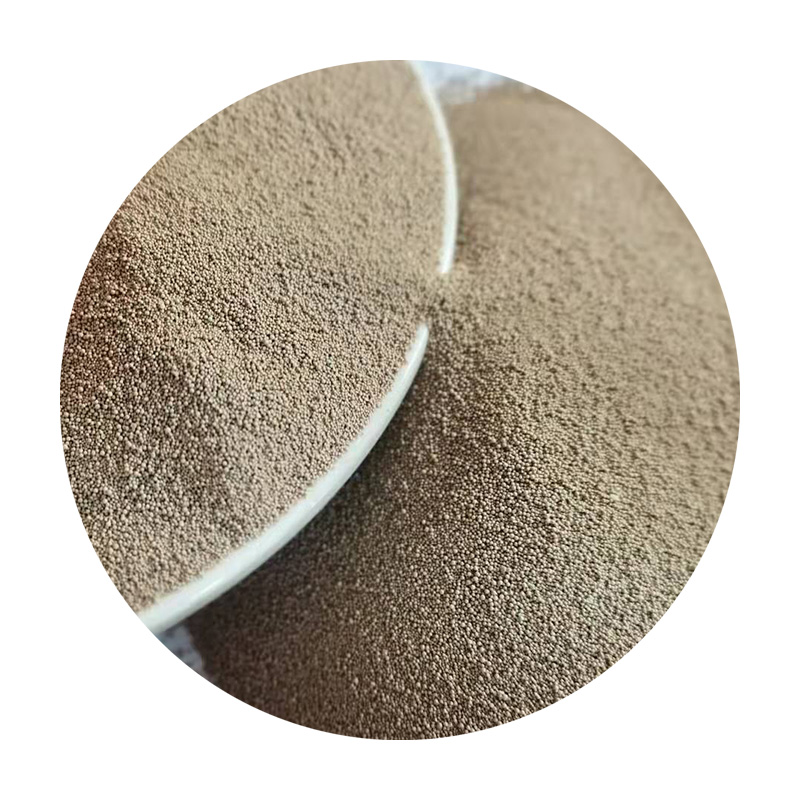
Once the metal has reached the appropriate temperature, it is poured into the mold. This process must be executed carefully to prevent defects such as air entrapment or oxidation. The molten metal is poured through a gating system, which controls the flow of the metal into the mold cavity. Proper pouring techniques are vital to ensure that the metal fills the entire mold without creating voids or cold laps.
5. Cooling and Solidification
After the metal is poured, it begins to cool and solidify. This phase is crucial as it determines the mechanical properties of the final product. Cooling too quickly can lead to cracking, while slow cooling may result in rough surfaces or unwanted microstructures. The cooling time varies based on the size and thickness of the casting, and regular monitoring is essential to avoid issues.
6. Mold Removal and Finishing
Once the metal has completely cooled and solidified, the mold is broken apart to remove the casting. This can be done manually or using specialized machinery. After removal, the casting often requires finishing operations to achieve the desired surface finish and dimensions. Common finishing processes include grinding, sandblasting, and machining.
7. Inspection
The final step in the sand casting procedure involves inspecting the casting for defects. This typically includes visual inspections, dimensional checks, and sometimes non-destructive testing methods, such as ultrasonic or radiographic examination. Ensuring quality at this stage is crucial for maintaining the durability and functionality of the final product.
Conclusion
Sand casting remains a vital and efficient method for producing metal components across various industries, including automotive, aerospace, and manufacturing. By understanding each stage of the sand casting process, from pattern making to inspection, manufacturers can achieve high-quality castings that meet strict tolerances and customer requirements. Whether for large-scale production or intricate custom parts, sand casting continues to be an indispensable technique in modern metallurgical engineering.
Post time:dec. . 07, 2024 15:15
Next:resin coated sand process