Sand Casting 101 An Overview of the Process
Sand casting, one of the oldest and most versatile metal casting techniques, has been used for centuries to create a wide variety of metal parts and components. This method involves using sand as the primary mold material, making it an affordable and flexible manufacturing process. In this article, we will explore the basics of sand casting, the steps involved, its advantages and disadvantages, and its applications.
The Process of Sand Casting
The sand casting process begins with the preparation of the mold. The mold is made of two halves, known as the cope and drag, which are pressed together to create a hollow cavity in the shape of the desired product. The sand used in this process is typically a mixture of silica sand, clay, and water, which gives it the necessary properties to hold its shape and resist deformation.
1. Mold Preparation To create the mold, the sand mixture is compacted around a pattern of the object that is to be cast. The pattern can be made from various materials such as metal, wood, or plastic. Once the sand is compacted, the pattern is removed, leaving a cavity that represents the shape of the part to be cast.
2. Core Making In cases where the casting has internal features or hollow sections, a core made of sand is also produced. The core is placed inside the mold cavity before pouring the molten metal.
3. Melting The next step involves melting the metal that will be poured into the mold. Various metals can be used in sand casting, including aluminum, iron, and bronze. The metal is typically melted in a furnace, reaching temperatures high enough to ensure it is in a liquid state.
4. Pouring Once the metal is molten, it is poured into the prepared mold through a sprue, a channel designed to direct the metal flow. The metal fills the cavity, taking the shape of the pattern and core.
5. Cooling After the mold is filled, the metal is allowed to cool and solidify. Cooling times can vary depending on the size of the casting and the type of metal used.
6. Mold Removal Once the metal has cooled, the sand mold is broken away to reveal the cast part. This can be done by hand or with the help of machines.
sand casting 101
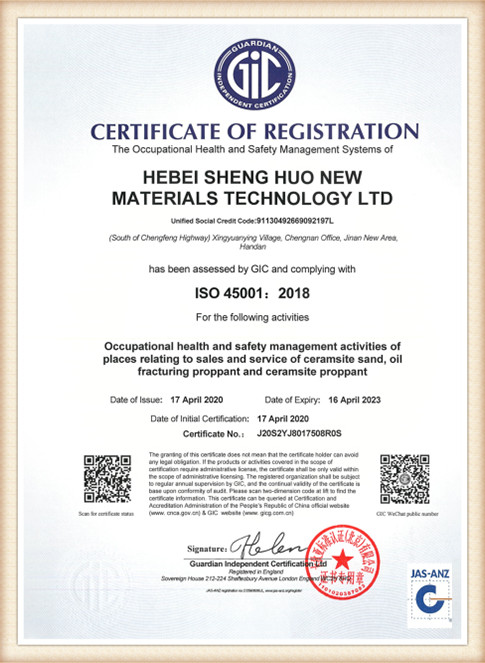
7. Finishing Operations Finally, the casting often undergoes finishing operations, which may include trimming excess material, grinding, and surface treatment to achieve the desired surface finish and dimensional accuracy.
Advantages and Disadvantages of Sand Casting
Sand casting offers several advantages
- Cost-Effectiveness The materials required for sand casting are relatively inexpensive, making it an economical choice for producing metal parts. - Flexibility The process allows for the casting of complex shapes and large sizes, which is not easily achievable with other methods. - Mold Reusability Although sand molds are typically destroyed after use, they can often be reused multiple times with some reconditioning.
However, there are also disadvantages
- Surface Finish Sand casting does not provide as smooth a surface finish as other methods, requiring additional finishing steps for aesthetic parts. - Dimensional Accuracy Castings may require machining to achieve strict tolerances, as sand casting can exhibit variations in dimensions. - Labor-Intensive The process can be labor-intensive, particularly in mold preparation and finishing, which can increase production time.
Applications of Sand Casting
Sand casting is widely used in various industries, including automotive, aerospace, and electronics, for producing components such as engine blocks, gear housings, and intricate parts with complex geometries. Its ability to accommodate a range of metals also allows manufacturers to select materials based on specific performance requirements.
In conclusion, sand casting remains a fundamental technique in metal manufacturing, offering a blend of affordability, flexibility, and capability to produce complex shapes. Despite some limitations, its widespread applicability continues to make it a popular choice for engineers and manufacturers seeking reliable casting solutions. As technology evolves, innovations in sand casting methods are likely to enhance its efficiency and precision even further, securing its place in modern manufacturing.
Post time:dec. . 20, 2024 15:56
Next:Current Market Trends for Foundry Sand Prices and Impacts on Industry