Properties of Foundry Sand
Foundry sand is a critical ingredient in the metal casting industry, serving as a mold material for producing metal parts and components. Various types of sand are employed in foundries, each with distinct properties that influence the quality and performance of the final product. Understanding these properties is essential for optimizing casting processes and ensuring the production of high-quality castings.
One of the primary properties of foundry sand is its grain size. The size and distribution of sand grains affect the permeability of the molded sand, which in turn influences the flow of gases during the casting process. Fine sand grains provide a smoother surface finish but may not allow sufficient airflow, leading to defects in the casting. Conversely, coarser grains improve permeability but can produce rough surface finishes. Therefore, the selection of appropriate grain size is crucial, balancing surface smoothness and gas permeability.
The shape of the sand grains also plays an important role in foundry applications. Ideally, foundry sand should have a well-graded distribution of particle shapes; spherical, angular, and sub-angular grains can each contribute differently to the mold's physical properties. Angular grains provide better interlocking and strength, while spherical grains can improve flowability and reduce the friction between particles. The combination of different shapes can enhance the overall performance of the sand in molding and casting processes.
Another essential property of foundry sand is its refractoriness, which refers to its ability to withstand high temperatures without melting or deforming. Foundry sands must have a high melting point to endure the heat generated during the casting process, particularly when molten metal is poured into the molds. Sand that possesses superior refractoriness ensures that the mold maintains its integrity and shape, preventing contamination of the mold the final product.
properties of foundry sand
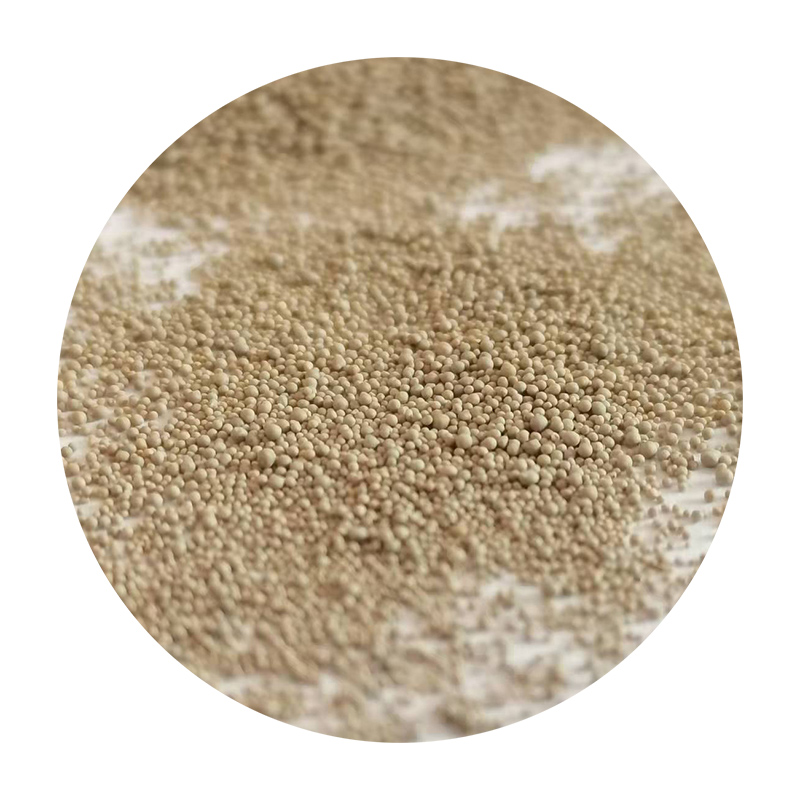
Furthermore, foundry sand must exhibit good bonding characteristics. This property is often influenced by the type of binder used in conjunction with the sand, such as clay, synthetic resins, or silica. A well-bonded sand mixture ensures that the mold retains its shape and strength during the pouring of molten metal. The binder type can also affect the risk of defects within the casting, such as sand inclusion or the presence of gas holes.
The moisture content of foundry sand is another critical factor impacting its properties. Proper moisture levels are vital for ensuring adequate cohesion among sand grains, which contributes to the mold’s strength. Too little moisture may make the sand insufficiently cohesive, causing the mold to crumble, while excessive moisture can lead to steam generation when metal is poured, resulting in defects. Therefore, foundries often conduct meticulous tests to determine the optimal moisture content before use.
In addition to these properties, foundry sand is evaluated based on its thermal conductivity. Sands with high thermal conductivity assist in the quick cooling of the metal, leading to finer grain structures and improved mechanical properties in castings. The choice of sand can significantly influence casting speed and overall efficiency in production.
In conclusion, the properties of foundry sand—such as grain size, shape, refractoriness, bonding characteristics, moisture content, and thermal conductivity—are essential considerations in the foundry industry. Selecting the right type of sand is crucial to ensure quality in casting processes and the production of superior metal components. As the industry continues to evolve, ongoing research and development will likely yield improved sand formulations and processing techniques that enhance the properties of foundry sand, further optimizing the casting process. Understanding these characteristics allows foundries to adapt to the growing demands for efficiency, precision, and quality in metal casting operations.
Post time:dec. . 07, 2024 13:32
Next:what is sand casting used for