Metal casting is a crucial manufacturing process used to create a wide range of metal components in various industries. Central to this process is the use of casting sand, an essential material that forms the mold into which molten metal is poured. The quality and characteristics of casting sand significantly impact the final product's integrity, surface finish, and overall dimensional accuracy.
Casting sand is typically composed of silica, which is known for its high melting point and excellent thermal stability. This makes it suitable for handling the high temperatures involved in metal casting, which can exceed 1,500 degrees Celsius (2,732 degrees Fahrenheit). The primary function of casting sand is to provide a mold that can endure the heat and pressure while allowing the molten metal to flow into the desired shape.
There are various types of casting sands, but the most common types are silica sand, resin-coated sand, and clay-based sand. Silica sand is favored for its cost-effectiveness and availability. It offers good permeability, allowing gases to escape during the pouring process, which helps to maintain the mold's integrity. However, silica dust poses health risks, necessitating the implementation of safety measures for workers handling it.
.
Clay-based sands are primarily used for their ability to retain moisture and provide flexibility. They contain natural clays, which improve the sand’s binding properties and give it a malleable consistency. While clay-sand molds can be labor-intensive to prepare, they have been traditionally used for centuries and remain popular in small-scale and artisan foundries.
metal casting sand
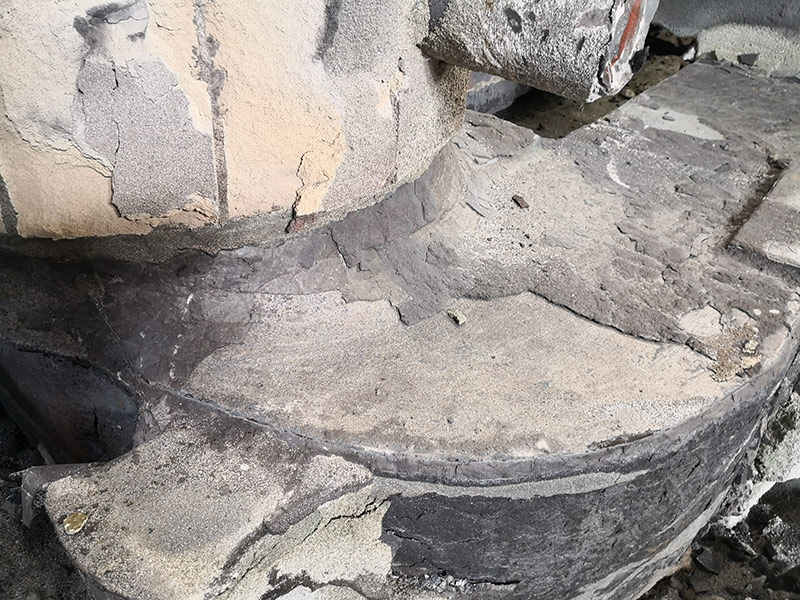
The choice of casting sand depends on various factors, including the type of metal being cast, the complexity of the part, and the required surface finish. The foundry must consider the thermal properties, resilience to deformation, and compatibility with the specific metal to achieve the desired outcome.
In addition to the chosen casting sand, the preparation and handling of the sand mix play a significant role in the casting process. Proper compaction, moisture content, and control of the sand's granulation are critical to ensuring a stable and durable mold.
As industries continue to evolve, advancements in casting sand technology are also being developed. Innovations such as synthetic sands and advanced binder systems are being explored to enhance performance, reduce environmental impact, and improve working conditions.
In conclusion, casting sand is an indispensable component in the metal casting industry, directly affecting the quality and efficiency of the manufacturing process. Its properties and types must be carefully selected to meet the specific needs of each casting project. With ongoing research and development, the future of casting sands promises further improvements, ensuring the advancement of metal casting technologies.
Post time:sept. . 22, 2024 22:25
Next:advantages and disadvantages of sand casting process