Foundry Sand Specifications Key Considerations for Optimal Casting Performance
In the field of metal casting, foundry sand plays a critical role in determining the quality and precision of the final product
. Understanding the specifications and characteristics of foundry sand is essential for foundry operators to achieve optimal casting performance and consistency.Foundry sand is primarily composed of silica, which is known for its high melting point, durability, and ability to withstand the rigors of the casting process. The most commonly used type of sand in foundries is silica sand, with a grain size that typically ranges from 0.1mm to 0.5mm. This size range is optimal for ensuring a balance between permeability, mold strength, and surface finish.
The chemical composition of foundry sand greatly affects its performance. Ideally, foundry sand should contain a minimal amount of impurities such as clay, silt, and dust, as these can negatively impact the casting process. Specifications often stipulate that silica sand should have a SiO2 content of at least 95%, ensuring high purity levels. Additionally, the presence of other oxides, such as Al2O3 and Fe2O3, should be controlled to prevent unwanted reactions during casting.
foundry sand specifications
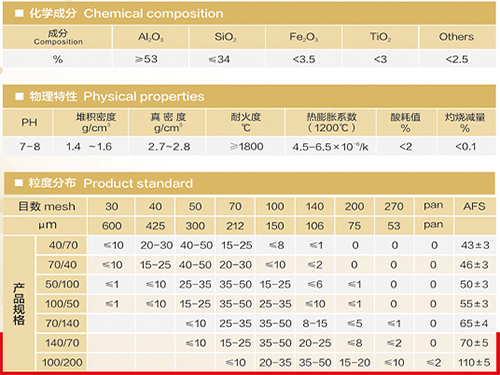
Another critical specification is the sand's permeability, which refers to its ability to allow air to pass through the mold. This property is essential for preventing defects such as gas porosity in castings. A permeability range of 80 to 120 darcies is typically desired, as it allows for adequate gas escape during the solidification of molten metal.
The thermal properties of the sand also play a significant role, as they affect the mold’s ability to withstand high temperatures during the casting process. Foundry sand should have a high thermal stability and low thermal expansion to minimize distortion and defects in the final casting.
Moisture content is another important specification; it should be carefully controlled, as excess moisture can lead to steam generation, which may compromise mold integrity and result in defects. Generally, an optimal moisture content of 2% to 4% is recommended.
In summary, adhering to stringent foundry sand specifications is pivotal for producing high-quality castings. By focusing on the chemical composition, grain size, permeability, thermal properties, and moisture content, foundries can enhance their operational efficiency and ensure the integrity of their finished products.
Post time:nov. . 20, 2024 14:15
Next:sand casting sand