Different Types of Foundry Sand
Foundry sand is a crucial material in the metal casting process, playing a vital role in producing high-quality castings. The primary function of foundry sand is to create a mold into which molten metal is poured, enabling the formation of intricate shapes and designs. Various types of foundry sand possess different properties, making them suitable for specific casting applications. Understanding these differences is key for foundry professionals to choose the right type of sand for their processes.
1. Silica Sand
Silica sand is the most commonly used type of foundry sand, primarily due to its availability and favorable properties. Composed primarily of silicon dioxide (SiO2), this type of sand exhibits high thermal stability and excellent durability. Silica sand can withstand high temperatures without decomposing, making it suitable for casting ferrous metals. Additionally, its round particle shape allows for better compaction, resulting in smoother mold surfaces and higher casting accuracy. Although silica sand is prevalent, there are concerns regarding silica dust exposure, which necessitates the implementation of safety measures in foundries.
2. Zircon Sand
Zircon sand, derived from the mineral zirconium silicate, is another important type of foundry sand, prized for its high thermal conductivity and low expansion property. As a result, zircon sand is particularly advantageous for casting non-ferrous metals, such as aluminum and copper alloys. Its ability to withstand high temperatures without deformation makes it ideal for producing intricate mold details. Additionally, zircon sand displays excellent resistance to metal penetration, helping to maintain mold integrity during the casting process. However, its higher cost compared to silica sand can be a limiting factor for some foundries.
3
. Olivine Sanddifferent types of foundry sand
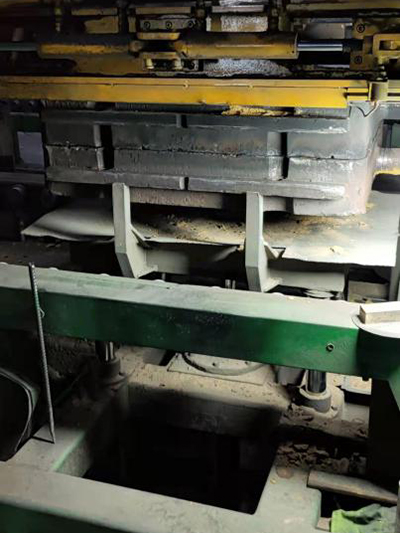
Olivine sand is a naturally occurring sand made up of the mineral olivine, which is rich in magnesium and iron. This type of sand is gaining popularity in foundries due to its superior properties. Olivine sand has a high melting point and excellent thermal stability, making it suitable for high-temperature applications. Its unique chemical composition reduces the occurrence of casting defects, such as gas porosity. Furthermore, olivine sand is less prone to environmental regulations since it does not contain free silica. Despite its advantages, the limited availability of olivine sand can pose challenges in some regions.
4. Resin-Coated Sand
Resin-coated sand is another innovative type of foundry sand that combines traditional sand with a resin binder. This process enhances the sand's properties, resulting in increased strength and better dimensional accuracy of the molds. The resin coating allows for quicker curing times, which can significantly improve production efficiency. Resin-coated sand is particularly beneficial for creating complex shapes and thin-walled castings, making it an excellent choice for the automotive and aerospace industries. However, the processing of resin-coated sand entails additional operational costs, which can impact overall foundry expenses.
5. Clay-Based Sand
Clay-based sand, often found in the form of bentonite, is widely used in the foundry industry for its excellent binding properties. When mixed with silica sand, clay enhances the cohesiveness of the mold, increasing its strength and resistance to deformation during the pouring process. Clay-based molds can maintain their shape under high temperatures, making them suitable for ferrous and non-ferrous metal castings. The main drawback of clay-based sand is the potential for moisture retention, which can lead to issues such as mold collapse if not properly managed.
Conclusion
The choice of foundry sand can significantly influence the quality, efficiency, and economic viability of the casting process. Each type of foundry sand—whether silica, zircon, olivine, resin-coated, or clay-based—offers distinct advantages and limitations suited to specific applications. Foundries must consider factors such as casting material, mold complexity, production volume, and environmental regulations when selecting the appropriate sand. By understanding the characteristics and applications of different types of foundry sand, manufacturers can optimize their processes and deliver high-quality castings to meet the demands of various industries.
Post time:dec. . 25, 2024 17:36
Next:Advantages of Sand Casting in Modern Manufacturing Processes