The Difference Between Sand Casting and Die Casting
Casting is a widely used manufacturing process that involves pouring molten material into a mold to create a desired shape. Among the various casting methods, sand casting and die casting are two of the most popular techniques. Each method has its unique advantages, disadvantages, and applications. Understanding the differences between sand casting and die casting is essential for engineers and manufacturers when choosing the appropriate method for a specific project.
Sand Casting
Sand casting is one of the oldest and most versatile casting processes. It involves creating a mold from a mixture of sand, clay, and water. The manufacturing process begins with the creation of a pattern that reflects the desired final object. This pattern is used to form a cavity in the sand mixture. The mold is then assembled, and molten metal is poured into the cavity. After the metal has cooled and solidified, the sand mold is broken away, revealing the final casting.
One of the most significant advantages of sand casting is its ability to produce large and complex shapes. The flexibility of creating various mold sizes and geometries makes it an ideal choice for prototyping and low-volume production. Additionally, sand casting can accommodate a wide range of metals, including aluminum, iron, and brass.
However, sand casting also has its drawbacks. The surface finish of sand-cast products is usually rougher compared to other casting methods, which may require additional machining processes for improved aesthetics or performance. Furthermore, the sand mold experiences lower dimensional accuracy, and the production cycle can be longer, as it involves multiple steps such as drying and breaking the mold.
Die Casting
Die casting, on the other hand, is a modern method that uses high pressure to force molten metal into a steel mold, or die. This technique is typically used for non-ferrous metals such as aluminum, zinc, and magnesium. Die casting molds are designed for high-volume production, making it a preferred method for manufacturing large quantities of parts with high precision.
difference between sand casting and die casting
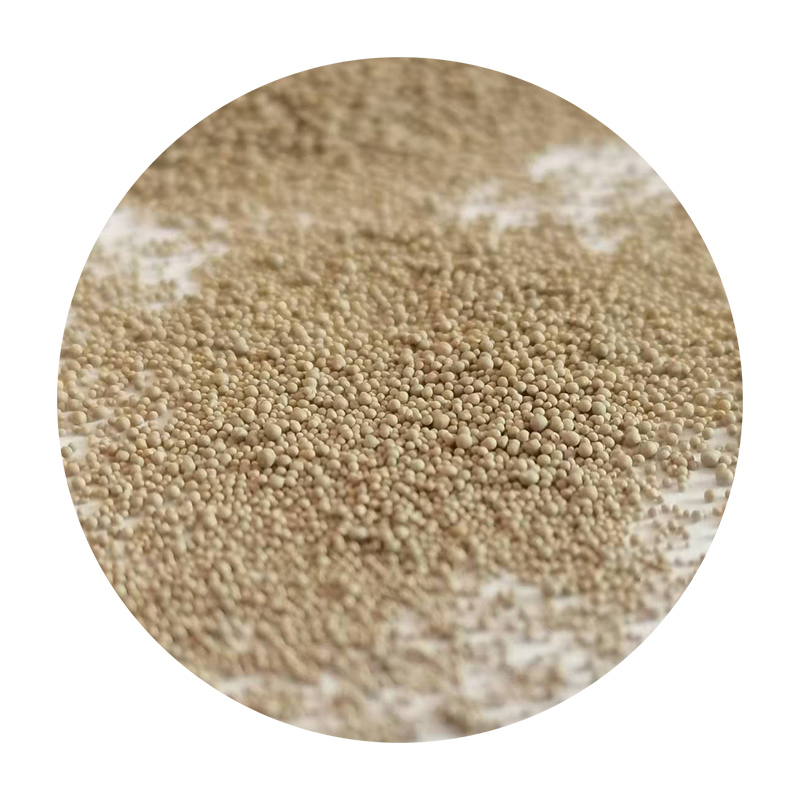
One of the primary benefits of die casting is its superior surface finish and dimensional accuracy. Because the molten metal is injected into a pre-heated mold at high pressure, the final product often requires minimal machining. The fast cycle times associated with die casting lead to enhanced productivity and cost-efficiency for mass production. Additionally, die casting molds can be reused hundreds of thousands of times, making it a long-term economical option.
Despite these advantages, die casting also has its limitations. The initial setup cost of die casting molds can be relatively high, making it less cost-effective for small production runs. Moreover, the complexity of the parts that can be produced through die casting is somewhat restricted compared to sand casting. Therefore, while die casting is suitable for producing intricate designs, it may not be the best choice for larger items or those requiring extreme dimensional changes.
Key Differences
The primary differences between sand casting and die casting can be summarized as follows
1. Mold Material Sand casting uses a mixture of sand and clay, while die casting utilizes hard, steel molds. 2. Process Sand casting involves gravity or low-pressure pouring of molten metal, whereas die casting employs high-pressure injection. 3. Production Volume Sand casting is better suited for low to medium production runs, while die casting is ideal for high-volume production. 4. Surface Finish and Accuracy Die casting typically yields parts with superior surface finishes and tighter tolerances compared to sand casting. 5. Material Compatibility Sand casting can accommodate a wider range of metals, whereas die casting is primarily used for non-ferrous metals.
Conclusion
In conclusion, both sand casting and die casting are valuable manufacturing processes that serve different purposes based on the specific needs of a project. Sand casting excels in versatility and the capacity to produce large, complex parts, while die casting stands out for its precision, efficiency, and surface quality. Understanding these differences allows manufacturers to select the most appropriate casting method for their production requirements, ultimately leading to better outcomes and optimized operations. Whether opting for sand casting or die casting, it is crucial to consider factors such as material type, production volume, and desired accuracy to make an informed decision.
Post time:nov. . 06, 2024 00:00
Next:Tips for Properly Sanding and Finishing Ceramic Surfaces Efficiently and Effectively