The Art and Science of Sand Casting
Sand casting is one of the oldest and most versatile forms of metal casting. This process, which dates back thousands of years, involves pouring liquid metal into a mold made from sand. Due to its cost-effectiveness and simplicity, sand casting continues to be a popular choice across various industries, including automotive, aerospace, and art.
The Process of Sand Casting
The sand casting process begins with the creation of a mold. The mold is formed by packing sand around a pattern that replicates the shape of the object to be created. Typically, the sand used is a mixture of silica sand, clay, and water. The clay acts as a bonding agent, while the water provides the necessary moisture to make the mold more pliable.
Once the pattern is positioned in the sand, it is often coated with a releasing agent to prevent the sand from sticking to the pattern. After the pattern is surrounded by sand, the sand is compacted to ensure it holds its shape. The next step is to remove the pattern, creating a cavity in the sand where the molten metal will be poured. The mold is then assembled, ensuring that the cavities line up perfectly and that there are no gaps.
The metal chosen for casting can vary depending on the desired properties of the final product. Common metals include aluminum, bronze, steel, and iron. The chosen metal is heated until it reaches a liquid state, typically in a furnace. Once the metal is molten, it is carefully poured into the mold. Gravity plays a crucial role in this phase; the molten metal flows into the cavity, filling every detail of the mold.
After pouring, the metal needs time to cool and solidify. The cooling period depends on the type of metal and the size of the casting. Once cooled, the sand mold is broken away to reveal the cast object. This removal process is where the name “sand casting” derives its significance. The sand is either shaken off or blasted away, leaving behind the newly formed metal shape.
Advantages of Sand Casting
describe sand casting
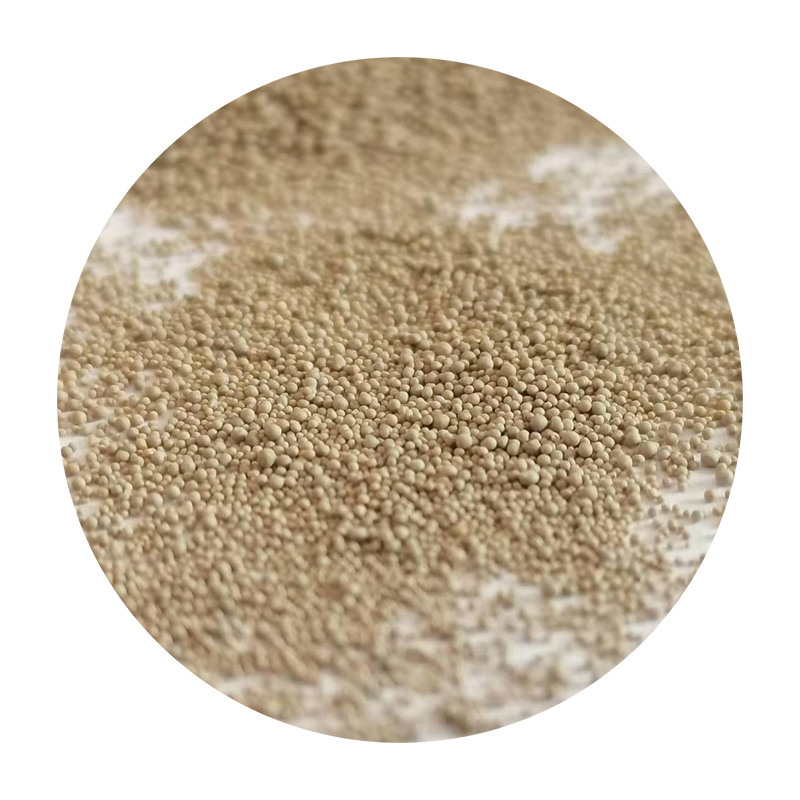
Sand casting offers numerous advantages. Firstly, it can accommodate complex shapes that might be challenging or impossible to produce using other methods. Additionally, sand casting is suitable for both small and large production runs, making it adaptable for different project requirements.
Another major advantage is the cost-effectiveness of the materials involved. Sand is relatively cheap and widely available, lowering the production expenses compared to other casting methods that require more specialized materials. Moreover, the mold can be easily modified, allowing manufacturers to make adjustments quickly without significant extra costs.
Sand casting also allows for the casting of large pieces, which is particularly beneficial in industries requiring big components, such as automotive and industrial machinery. Large castings can be created in a single pour, minimizing the need for assembly or joining multiple pieces.
Limitations of Sand Casting
Despite its many advantages, sand casting has some limitations. The surface finish of sand-cast products is typically rougher than those produced by other casting processes, which may require additional machining to achieve a smoother finish. Additionally, due to the nature of the sand mold, it is not ideal for producing high-precision castings where tight tolerances are necessary.
Another drawback is the slow production rate compared to other modern methods, such as die casting. This may result in longer lead times for large-scale production. Also, sand casting might not be suitable for very intricate designs, as the sand can be challenging to manipulate to obtain fine details.
Conclusion
In summary, sand casting is a time-honored technique that combines art and science to create various metal objects, ranging from everyday tools to intricate artistic sculptures. Its advantages of cost-effectiveness and versatility make it a popular choice in numerous industries, even amid the rise of advanced manufacturing technologies. While it has its limitations, the process of sand casting remains a relevant and valuable method in the metalworking world, celebrating a rich history while continuing to evolve with contemporary needs. As long as there is a demand for unique and durable metal products, sand casting will hold a significant place in manufacturing.
Post time:nov. . 08, 2024 13:37
Next:Understanding the Role and Properties of Foundry Sand in Metal Casting Processes