Casting Sand for Metal A Crucial Element in Metalworking
Casting is one of the oldest metalworking techniques known to humanity, dating back thousands of years. Central to this process is casting sand, a vital component that enables the formation of metal objects. Understanding casting sand, its types, properties, and applications provides insight into its significant role in the foundry industry.
What Is Casting Sand?
Casting sand is a specially graded sand used to create molds in metal casting. Its primary purpose is to form a negative shape of the intended metal object, into which molten metal can be poured. Once the metal solidifies, the mold is broken away to reveal the finished product. The characteristics of casting sand directly impact the quality and precision of the final cast.
Types of Casting Sand
There are several types of casting sands, each with distinct properties tailored to specific applications
. The most common include1. Silica Sand The most widely used casting sand, silica sand consists primarily of silicon dioxide. It has excellent thermal stability and durability. Its grain size and shape can be adjusted to suit different casting techniques, making it a versatile choice for various metals.
2. Green Sand Comprising silica sand, clay, and water, green sand is a popular choice for ferrous (iron and steel) and non-ferrous metals. It retains moisture, which allows the sand particles to adhere to each other, creating a sturdy mold. This type of sand is highly favored in iron foundries due to its ease of use and reusability.
3. Shell Sand This type of sand is used to create thin shells for molds, often employed in more complex casting applications. Shell sand is mixed with a resin that is then cured through heat, resulting in a high-strength mold that can capture intricate details.
casting sand for metal
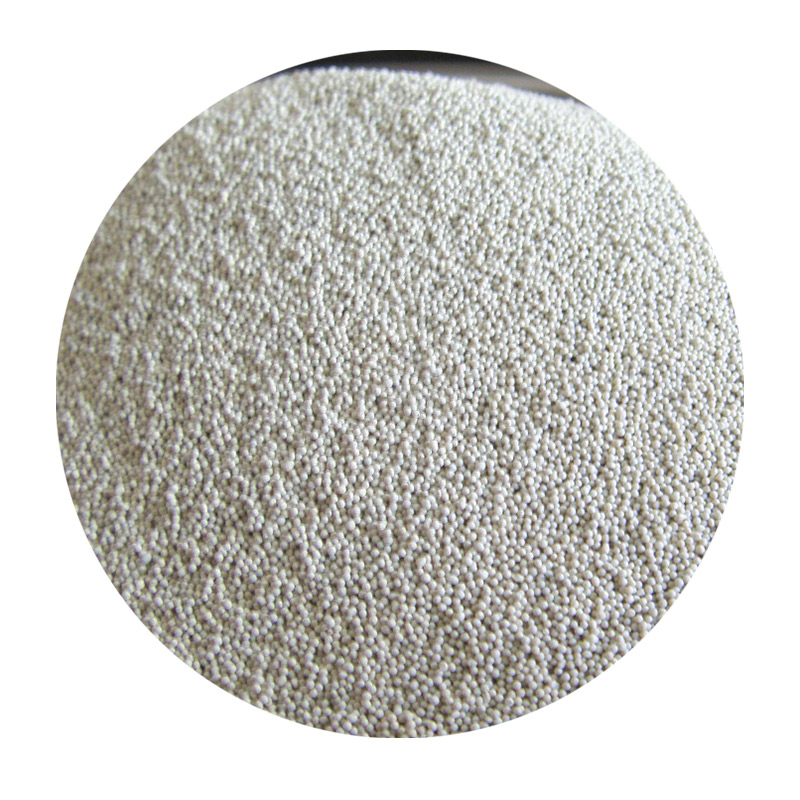
4. Lost Foam Sand Used in lost foam casting, this sand is designed to work with polystyrene patterns that vaporize when molten metal is poured in. This method allows for smooth finishes and complex geometries but requires specific sand qualities to ensure a successful cast.
Properties of Casting Sand
The effectiveness of casting sand is determined by its various properties, including grain size, shape, and composition.
- Grain Size Finer sands can produce smooth surface finishes on castings, while coarser grains allow for better airflow during pouring, reducing defects. - Permeability Casting sand must allow gases to escape during metal pouring. High permeability minimizes the risk of defects such as blowholes. - Plasticity The ability of the sand to retain its shape while also being pliable enough to be manipulated determines the mold’s durability.
Applications in Industry
Casting sand plays a pivotal role in various industries, including automotive, aerospace, and art metalworking. In the automotive sector, sand casting is used to produce engine blocks, transmission cases, and other critical components. The aerospace industry employs casting for lightweight yet strong components that are essential for aircraft performance.
Moreover, casting sand technology continues to evolve, with advancements aimed at improving sustainability. Innovations like sand recycling programs and the development of eco-friendly binders are gaining traction, reflecting a move toward more responsible manufacturing practices.
Conclusion
In conclusion, casting sand is a fundamental element in the metalworking industry, integral to producing quality castings. As technology advances, the significance of casting sand remains steadfast, with ongoing improvements ensuring it meets the evolving demands of modern manufacturing. Whether in foundries or research labs, understanding casting sand’s properties and applications will continue to be essential for anyone involved in metalworking.
Post time:oct. . 06, 2024 07:01
Next:sand for metal casting