Advantages and Disadvantages of the Sand Casting Process
Sand casting is a widely used metal casting process that utilizes sand as the primary mold material. It is favored in various industries due to its unique characteristics, yet it also comes with its own set of drawbacks. Understanding both the advantages and disadvantages of sand casting can help manufacturers make informed decisions regarding its implementation in production.
Advantages of Sand Casting
1. Cost-Effectiveness One of the most significant advantages of sand casting is its low cost. The materials used in this process, primarily sand and a bonding agent, are inexpensive and readily available. This makes it an ideal choice for low to medium-volume production runs, especially for small businesses and startups.
2. Versatility Sand casting can accommodate a wide range of metals, including aluminum, iron, and copper-based alloys. This versatility allows manufacturers to produce complex shapes and designs that would be difficult or impossible with other casting methods.
3. Large Components Sand casting is particularly effective for producing large parts. Its ability to create molds that can easily accommodate sizable components makes it invaluable in industries such as aerospace and automotive, where large castings are often required.
4. Ease of Use The sand casting process is relatively straightforward. Once the mold is created, the metal can be poured in, making the process accessible to operators with varying levels of experience. This simplifies training and can reduce labor costs.
5. Good Dimensional Tolerance For certain applications, sand casting can achieve acceptable dimensional tolerances. While it may not provide the precision of some other casting processes, it is often sufficient for many industrial applications.
advantages and disadvantages of sand casting process
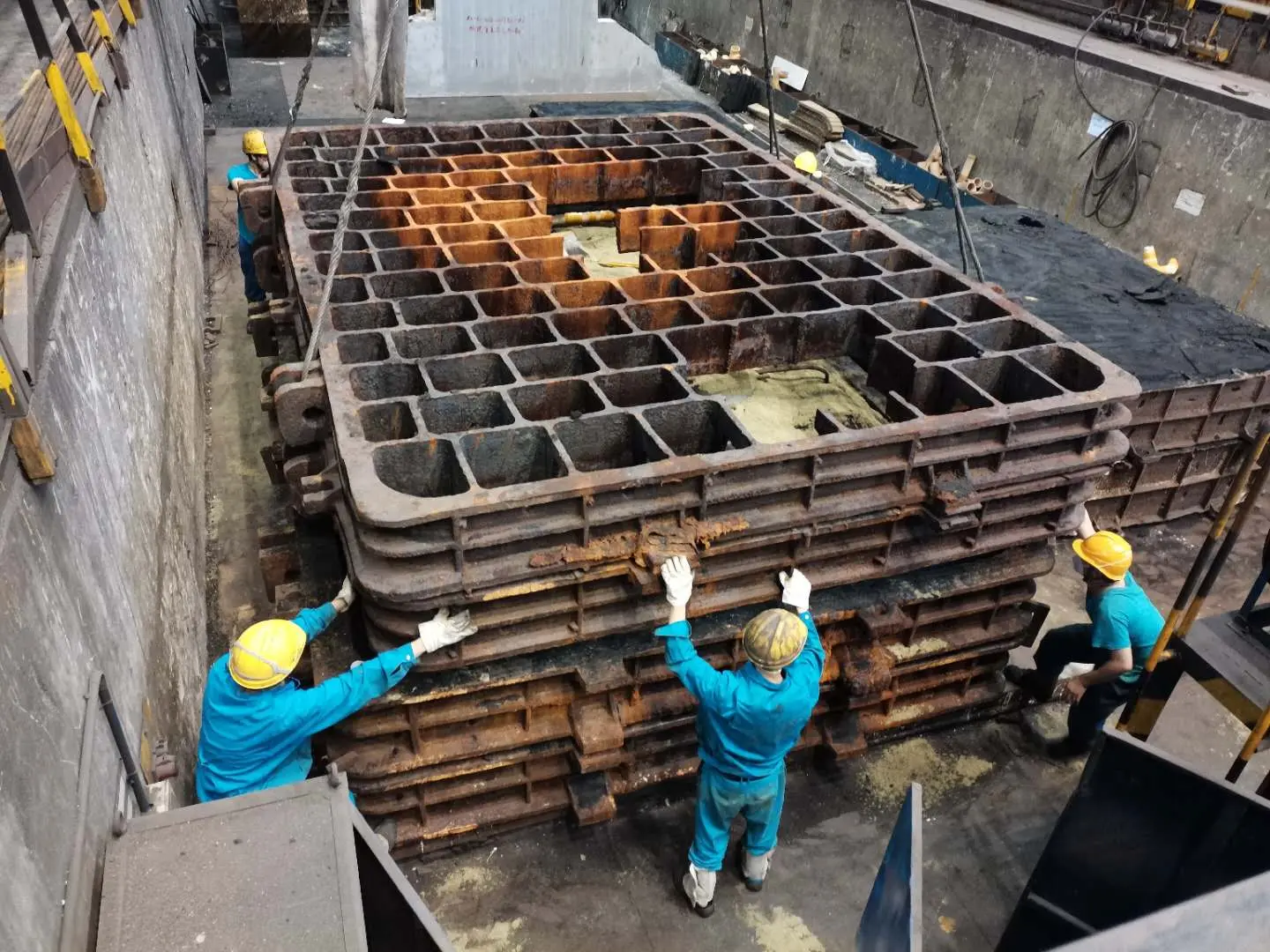
Disadvantages of Sand Casting
1. Surface Finish Quality One of the notable drawbacks of sand casting is the surface finish it produces. Castings often have rough surfaces that may require additional machining or finishing processes, which can increase production costs and time.
2. Labor-Intensive Although the process is relatively easy to learn, sand casting can be labor-intensive. The creation of molds, especially for complex designs, can require significant manual effort, which can impact production efficiency.
3. Limited Detail and Accuracy While sand casting is versatile, it is not suitable for producing extremely intricate and detailed parts. The nature of sand molds limits the level of detail that can be achieved, making it less ideal for precision applications.
4. Environmental Concerns The materials used in sand casting, especially silica sand, can pose environmental hazards if not managed properly. Additionally, the process can produce waste and emissions that require careful handling and disposal.
5. Production Time Although the setup time for sand casting can be relatively short, the cooling time for metal can be significant, especially for thicker sections. This might lengthen the overall production time compared to other casting methods such as die casting.
Conclusion
In conclusion, sand casting is a versatile and cost-effective method suitable for many applications, particularly when producing large and complex parts. However, manufacturers must carefully consider its disadvantages, such as surface finish quality, labor intensity, and environmental impact. By weighing these factors, businesses can determine whether sand casting is the right choice for their specific production needs, balancing efficiency and quality in their manufacturing processes.
Post time:aug. . 31, 2024 18:16
Next:g2 सुपर रेती।