3D Sand Casting Transforming Manufacturing with Innovation
In the world of manufacturing, the quest for efficiency, accuracy, and innovation has led to the development of various advanced techniques. One such technique that has gained prominence in recent years is 3D sand casting. This innovative method combines traditional sand casting processes with modern 3D printing technology to create high-quality metal parts with exceptional precision.
Understanding Sand Casting
To appreciate the impact of 3D sand casting, it's essential to understand traditional sand casting. Sand casting is one of the oldest manufacturing processes, dating back thousands of years. It involves creating a mold from a mixture of sand and a binding agent, into which molten metal is poured to create a desired shape. While effective, traditional sand casting can be time-consuming, particularly during the mold-making process, which often requires the use of complex patterns and multiple tooling.
The Rise of 3D Printing
The advent of 3D printing technology has revolutionized various industries by enabling rapid prototyping and custom manufacturing. With 3D printing, digital designs can be transformed into physical objects layer by layer, making it possible to create complex geometries that would be difficult or impossible to achieve with traditional methods. The integration of 3D printing into the sand casting process heralds the dawn of 3D sand casting.
How 3D Sand Casting Works
In 3D sand casting, the process begins with a digital model of the part to be created, which can be designed using computer-aided design (CAD) software. This model is then used to create a mold using 3D printing technology. The mold is typically made from a special type of sand mixture that can hold its shape once printed. The printed mold is then used in a similar manner to conventional sand molds. Once the mold is prepared, molten metal is poured into it and allowed to cool, after which the solidified part is removed.
3d sand casting
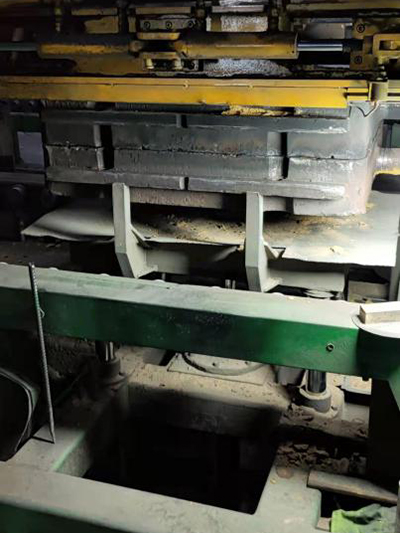
Advantages of 3D Sand Casting
One of the most significant advantages of 3D sand casting is its ability to produce complex geometries. Traditional sand casting often requires multiple parts and assembly, while 3D sand casting can create intricate designs in a single piece, reducing assembly time and potential points of failure. Moreover, the digital nature of 3D design allows for rapid modifications. If changes are needed for a specific part, adjustments can be made swiftly without the delays associated with traditional tooling methods.
Additionally, 3D sand casting is more environmentally friendly compared to traditional methods. The combination of 3D printing with sand casting reduces waste, as the additive process utilizes only the material required for the mold. This efficiency not only minimizes material costs but also reduces the ecological footprint of the manufacturing process.
Applications Across Industries
3D sand casting has found applications across various industries, from automotive and aerospace to art and architecture. Manufacturers can produce components with optimized weight-to-strength ratios, which is crucial in sectors such as automotive where fuel efficiency is paramount. In aerospace, the ability to create complex parts that are both lightweight and robust can lead to improvements in overall performance and safety.
Conclusion
In conclusion, 3D sand casting represents a significant leap forward in manufacturing technology. By merging the age-old technique of sand casting with state-of-the-art 3D printing, this method allows for the creation of complex, high-quality parts while streamlining the production process. As industries continue to seek innovative solutions to meet modern challenges, 3D sand casting is poised to play a crucial role in the future of manufacturing.
Post time:nov. . 19, 2024 19:20
Next:sand castings manufacturer