Why is Sand Casting Used?
Sand casting is one of the oldest and most versatile metal casting processes, widely used across various industries, from automotive to aerospace and even in art and sculpture. The reasons for its popularity are numerous, ranging from its cost-effectiveness to its capability of producing complex geometries. Below, we explore the key reasons why sand casting remains a preferred choice in manufacturing.
1. Cost-Effectiveness
One of the most significant advantages of sand casting is its cost-effectiveness. The raw materials used, primarily sand, are relatively inexpensive and readily available. The casting process does not require expensive machinery or complex setups, making it an attractive option for small production runs and prototyping. Additionally, because sand can be reused multiple times, the overall costs of the operation are further reduced, making it a practical choice for many manufacturers.
2. Versatility in Material Selection
Sand casting is highly versatile when it comes to the types of metals that can be used. Various metals, including aluminum, zinc, magnesium, and iron, can be effectively cast using this method. This flexibility allows manufacturers to select the material that best fits the performance requirements of the final product. The ability to cast ferrous and non-ferrous metals expands its utility across different industries and applications.
3. Ability to Create Complex Shapes
The sand casting process enables the production of intricate shapes and designs that might be difficult or impossible to achieve with other casting methods. The use of sand as a mold material allows for complicated geometries and fine detailing, which is especially advantageous in sectors that require high precision. This capability encourages innovation in design, leading to the development of lighter and more efficient components.
4. Large Part Production
Another key advantage of sand casting is its ability to produce large parts. Industries such as automotive and heavy machinery often require components that can be several feet in size. Sand casting molds can be built to accommodate these larger dimensions, allowing manufacturers to create significant pieces with ease. This aspect is particularly vital for producing components like engine blocks, frame parts, and other large machinery.
why is sand casting used
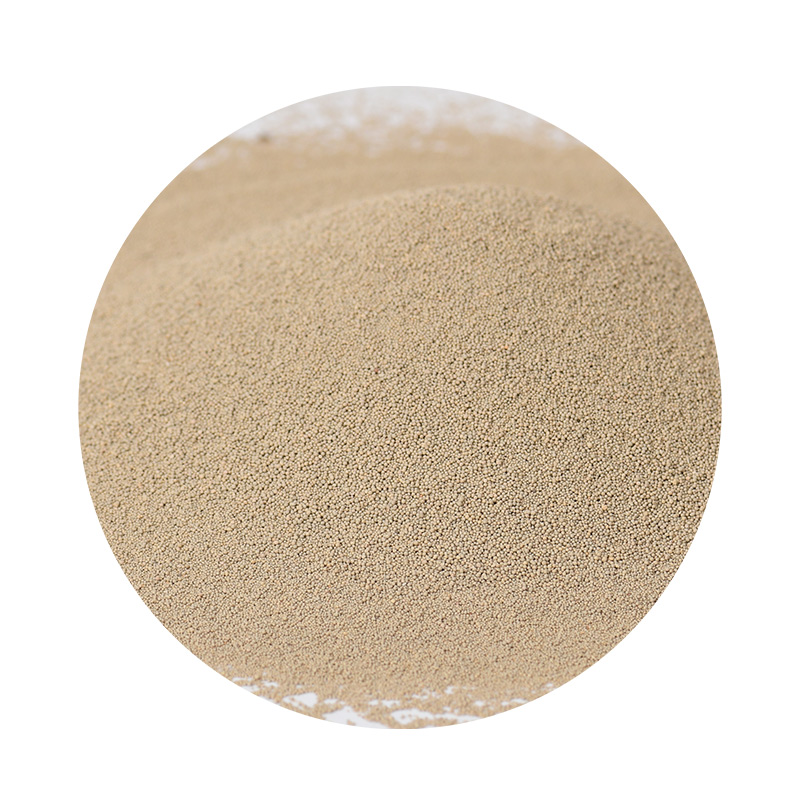
5. Short Lead Times
The lead time for creating sand molds is significantly shorter than for many other manufacturing processes. Once the pattern is made, the sand can be packed around it to create molds quickly. This expedited process means that manufacturers can respond to market demands and production requirements more rapidly, which is increasingly important in a fast-paced business environment.
6. Minimal Finishing Needed
In many cases, sand-cast parts require less machining compared to parts made with other casting processes. Depending on the finish and tolerances required, some sand-cast components can be used directly after casting, reducing the time and cost associated with additional finishing processes. This efficiency is a compelling factor that contributes to the overall value proposition of sand casting.
7. Easy Modification and Adaptation
Given that patterns can be relatively simple to produce, modifications to existing designs can be made without extensive cost implications. This adaptability is essential for prototype development, as it allows companies to experiment with new ideas and iterate designs based on testing and feedback. Industries that prioritize innovation often leverage this flexibility to refine their products continuously.
8. Environmentally Friendly Options
In recent years, advances in sand casting technology have introduced more environmentally friendly practices. Techniques such as using water-soluble binders and recyclable sand have emerged, reducing the ecological footprint associated with traditional sand casting. As environmental concerns grow, such innovations position sand casting as a sustainable manufacturing option.
Conclusion
Sand casting remains a stalwart in the world of manufacturing due to its myriad advantages ranging from cost-effectiveness to design versatility. Whether for creating complex automotive components, large machinery parts, or detailed sculptures, the benefits of sand casting make it a go-to choice across multiple sectors. As technology advances and the industry continues to seek sustainable alternatives, sand casting is likely to retain its relevance and importance in the manufacturing landscape for years to come.
Post time:Dez . 30, 2024 17:42
Next:Essential Stages in the Sand Casting Process for Metal Casting Efficiency