Sand Casting Mass Production An Overview
Sand casting, one of the oldest and most versatile manufacturing processes, continues to play a critical role in modern mass production. This method involves pouring molten metal into a sand mold, where it solidifies into the desired shape. The widespread use of sand casting is attributed to its cost-effectiveness, flexibility in design, and ability to produce complex geometries. In this article, we will explore the principles of sand casting, its advantages, and the advancements that have optimized the mass production process.
The Principles of Sand Casting
The sand casting process begins with preparing a mold from a mixture of sand and a bonding agent, often clay. The mold is created in two halves, known as the cope and the drag. The pattern, a replica of the final product, is pressed into the sand to create cavities. Once the mold halves are assembled, molten metal is poured into the cavity. After cooling, the mold is broken apart to retrieve the solidified casting.
The choice of sand is critical. Silica sand is commonly used due to its high melting point and abundance. The sand must be capable of retaining its shape and withstanding the heat of the molten metal. Various additives are used to enhance certain properties, such as permeability and strength, which are essential to achieving high-quality casts.
Advantages of Sand Casting
One of the primary advantages of sand casting is its adaptability. The process can accommodate a wide range of metals, including aluminum, iron, and magnesium, making it suitable for diverse applications across various industries, such as automotive, aerospace, and machinery manufacturing. Its capacity for producing intricate shapes and designs without the need for costly tooling makes it particularly attractive for prototypes and custom one-off designs.
Furthermore, sand casting is scalable. Whether producing a single piece or thousands of units, the method can easily be adjusted to meet production demands. This flexibility is a significant asset in today's fast-paced market, where the ability to pivot quickly in response to consumer needs can determine a company's success.
sand casting mass production
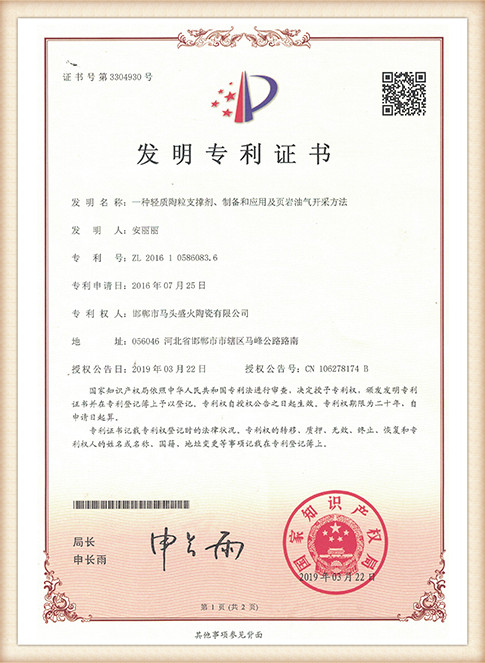
Advancements in Sand Casting
Recent advancements in technology have significantly improved the efficiency and quality of sand casting processes. For instance, the implementation of computer-aided design (CAD) and computer-aided manufacturing (CAM) systems has streamlined the design phase, allowing for rapid prototyping and precise mold creation. These tools enable engineers to simulate the casting process, identify potential defects, and refine designs before physical production begins, reducing waste and time.
Automated machinery has also enhanced the sand casting process. Robots can handle tasks such as mixing sand, pouring metal, and even finishing components. Automation reduces human error and increases production rates, leading to more consistent product quality. Moreover, the integration of real-time monitoring systems helps manufacturers track the casting process, enabling quick adjustments to maintain optimal conditions.
Environmental Considerations
As with any manufacturing process, sand casting does raise environmental concerns. Traditional sand casting generates a significant amount of waste, particularly in the form of used sand and spent materials. However, many manufacturers are now adopting sustainable practices, such as recycling sand and using eco-friendly binding agents. Innovations in sand reclamation technology allow for the reprocessing of used sand, reducing the demand for fresh materials and minimizing environmental impact.
Additionally, the ability of sand casting to produce net-shaped parts can lead to reduced energy consumption and material waste in downstream machining processes. By focusing on producing more precise shapes, manufacturers can limit the amount of excess material that must be removed, enhancing overall sustainability.
Conclusion
Sand casting remains a cornerstone of mass production due to its unique advantages and adaptability to modern manufacturing needs. With advancements in technology, the process has evolved to become more efficient and environmentally friendly, positioning it well for the challenges of the future. As industries continue to seek innovative solutions to meet growing demands, sand casting will undoubtedly maintain its relevance, showcasing its enduring legacy in the world of manufacturing. In an age where customization and rapid production are crucial, sand casting offers a reliable method that balances quality, cost, and efficiency.
Post time:Set . 29, 2024 02:01
Next:Exploring Innovative Uses of Sand Casting Techniques in Various Industries