Sand for Casting An Essential Component in Metalworking
Casting is one of the oldest manufacturing processes, dating back thousands of years, and sand has played a crucial role in its development and success. Sand casting, in particular, is a widely-used technique that allows for the production of complex shapes and designs with relative ease and efficiency. In this article, we will explore the importance of sand in casting, the types commonly used, and the benefits it brings to the metalworking industry.
The Role of Sand in Casting
Sand serves as a mold material in the casting process, where it is compacted around a model to form a cavity that reflects the desired shape of the final product. The primary task of the sand is to withstand the heat of the molten metal while providing sufficient strength and durability to maintain the mold’s shape. Moreover, sand must exhibit good permeability to allow gases generated during metal pour to escape, preventing defects in the finished casting.
Types of Sand Used in Casting
The most common type of sand used in casting is silica sand, composed primarily of silicon dioxide. Silica sand is favored due to its high melting point and its thermal stability, which are essential for withstanding the extreme temperatures associated with molten metals. Additionally, resin-coated sand has become increasingly popular in modern foundries. This type of sand is coated with a resin that enhances its binding properties, leading to improved surface finish and precision in the final casting.
Another type of sand used is olivine sand, which is magnesium iron silicate. Olivine is known for its superior thermal properties and lower expansion rate, making it an excellent choice for specific casting applications. There are also specialty sands like zircon sand and chromite sand, which are used for specialized requirements due to their unique chemical and physical properties.
sand for casting
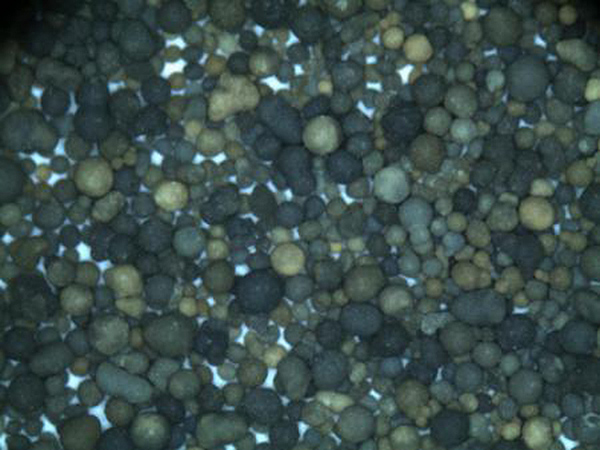
Advantages of Sand Casting
Sand casting offers numerous advantages that make it a preferred method in many industries. One of the most significant benefits is versatility; sand molds can be easily shaped to accommodate complex geometries, making it suitable for producing a wide variety of components, from small parts to large industrial applications.
Another advantage is the cost-effectiveness of sand casting. The materials used, primarily sand, are abundant and inexpensive. This allows manufacturers to produce large quantities of castings without incurring prohibitive costs. Furthermore, the sand can often be reused for multiple casting processes, minimizing waste and reducing production costs.
The relatively simple setup required for sand casting makes it accessible to both large-scale manufacturers and small artisans. The process does not necessitate complex machinery or setups, allowing for quick adjustments and prototypes, which is especially valuable in industries that demand rapid prototyping and development.
Conclusion
In conclusion, sand plays an indispensable role in the casting process, serving as a primary material for molds that enable the effective creation of metal components. With its diverse types, each offering unique advantages, sand casting remains a cornerstone of the metalworking industry. As technology advances, innovations in sand casting processes continue to emerge, promising even greater efficiencies and capabilities in the future. Whether for small custom projects or large-scale industrial production, the significance of sand in casting cannot be overstated.
Post time:Ago . 30, 2024 21:35
Next:what materials are used for sand casting