The Art and Science of Resin Sanding Achieving Flawless Surface Finishes
Resin sanding is an essential technique in the world of resin art and craft, particularly when creating items such as jewelry, tabletops, and decorative pieces. This process involves smoothing out the resin surface after it has cured, ensuring that the final product is not only visually appealing but also safe and comfortable to handle. Understanding the intricacies of resin sanding can significantly enhance the quality of your projects.
Understanding Resin
Before delving into the sanding process, it's essential to understand what resin is. Epoxy resin, a popular choice among artists and craftsmen, is a synthetic compound comprised of two main components the resin itself and a hardener. When mixed together, they undergo a chemical reaction that transforms the liquid mixture into a solid, durable material. This resin is valued for its glossy finish and versatility, making it suitable for a variety of applications. However, once it hardens, the surface may have inconsistencies like bubbles, waves, or uneven areas that need to be addressed.
Why Sanding is Necessary
Sanding is a critical step in achieving a professional finish on your resin projects. Cured resin often has imperfections that not only detract from its aesthetic appeal but may also affect its functionality. By sanding the surface, you can eliminate these flaws along with any unwanted texture. This process also prepares the surface for further finishing techniques or coatings, such as varnishes or sealants, which can enhance durability and gloss.
Tools and Materials Needed
To achieve the best results in resin sanding, gather the following tools and materials
1. Sanding Blocks or Sponges These provide a good grip and allow for even pressure application. 2. Sandpaper Start with a coarser grit (like 80 or 120) to remove larger imperfections, then gradually move to finer grits (like 400, 600, or even up to 2000) for smoothing. 3. Water Wet sanding can help reduce dust and achieve a finer finish. 4. Safety Gear Always wear a mask and goggles while sanding to protect against dust and debris.
resin sanding
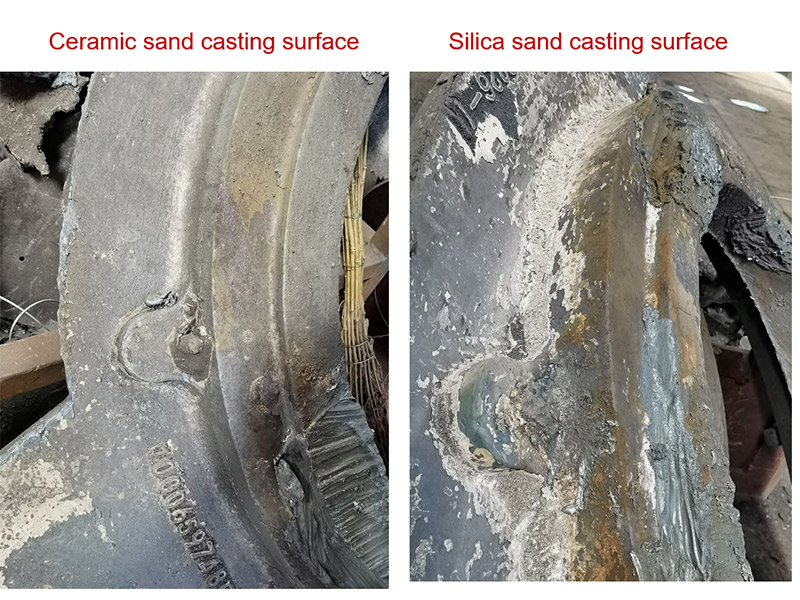
The Sanding Process
1. Initial Assessment After the resin has cured (typically 24 to 72 hours depending on the resin used), inspect the surface for imperfections like bubbles or unevenness.
2. Coarse Sanding Start with the coarser grit sandpaper. Use a sanding block or sponge to apply even pressure, moving in small circular motions. Be cautious not to apply too much pressure, as this could cause the resin to become uneven. Focus on the areas needing the most attention.
3. Progress to Finer Grits Once the major imperfections are addressed, switch to a finer grit sandpaper. Continue sanding using confidence and a consistent motion until achieving a smoother texture. This step is crucial as it begins to prepare the surface for polishing.
4. Wet Sanding For the final sanding stage, wet sanding can be particularly effective. Dampen the sandpaper and the surface before sanding. This method minimizes dust, helps keep the surface cool, and results in a much smoother finish.
5. Final Touches After sanding, clean the surface with a damp cloth to remove any remaining dust. At this point, you may choose to apply a polish to enhance the glossiness or a topcoat for added protection.
Conclusion
Resin sanding may seem daunting at first, but mastering this technique is vital for creating high-quality resin art. The careful selection of tools, the understanding of the process, and attention to detail can lead to stunning results. As you gain experience in resin sanding, you’ll find that your skills will not only improve but also elevate the overall quality and presentation of your resin projects. Happy crafting!
Post time:Dez . 17, 2024 05:14
Next:can you sand a 3d print