Lost Foam Casting An Innovative Approach to Metal Casting
Lost foam casting (LFC) is an advanced metal casting technique that has gained considerable attention in the manufacturing industry for its efficiency, precision, and cost-effectiveness. This process combines the traditional methods of sand casting with modern technologies, resulting in intricate and high-quality metal parts that meet the demands of today’s complex applications.
At its core, lost foam casting involves creating a foam pattern, which is a replica of the desired final product. This pattern is typically made from polystyrene, a lightweight and versatile material. The process begins with the creation of the foam pattern, which is coated with a thin layer of fine sand mixed with a binder. Once coated, the foam pattern is then placed in a mold made of sand. The key innovation of this method lies in what happens next the mold is subjected to hot metal pouring, which evaporates the foam pattern, leaving a hollow cavity that mirrors its shape.
One of the greatest advantages of lost foam casting is its ability to produce highly detailed and complex shapes with minimal tooling costs. Traditional casting methods often require expensive mold patterns, which can be time-consuming to produce. In contrast, the lost foam process allows for rapid prototyping and the ability to make design changes on the fly, significantly speeding up production times. This flexibility makes it an attractive option for industries that require quick turnarounds, such as automotive and aerospace.
Another significant benefit of lost foam casting is its ability to reduce waste. In conventional sand casting, the patterns are usually made from metal or wood, which can lead to substantial waste during the machining process. Since the foam pattern is evaporated, there’s no leftover material to remove. Furthermore, the precision with which the molds are created means there is often less need for post-casting machining, further minimizing material loss.
lost foam casting
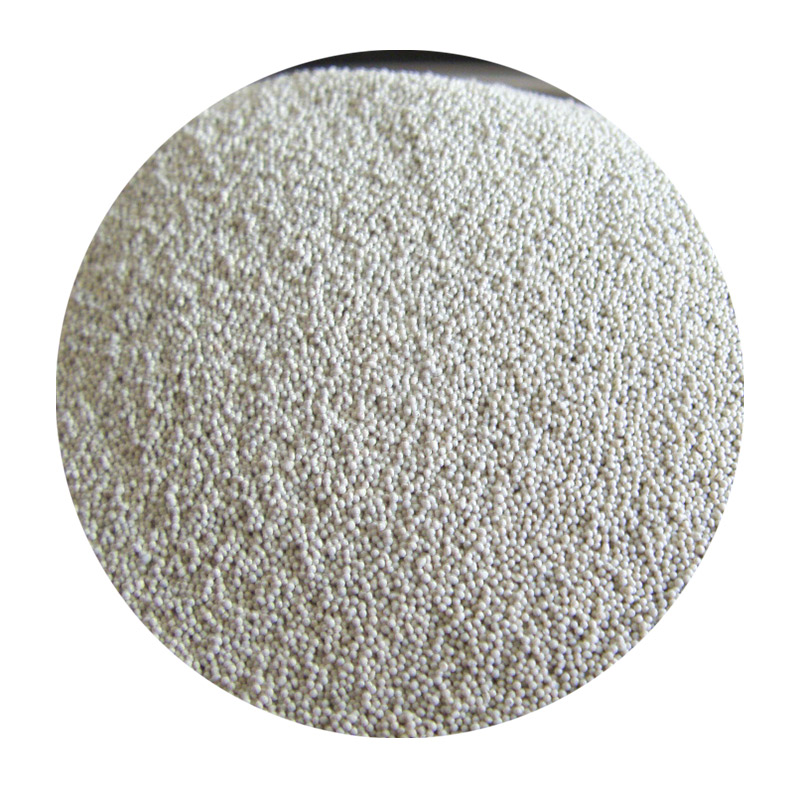
Lost foam casting also opens the door for using more challenging materials. The ability to produce high-quality parts from various alloys, including aluminum, iron, and steel, makes it suitable for a wide range of applications. This versatility allows designers and engineers to explore new possibilities and innovations in product development without the constraints of traditional casting methods.
One of the challenges associated with lost foam casting is the control of the molten metal flow. Since the foam evaporates during pouring, if the metal enters the mold too quickly, it can lead to defects such as gas pockets or irregularities in the final product. However, advancements in technology and better process controls have helped mitigate these issues, making the process more reliable.
Moreover, as industries increasingly prioritize sustainability, lost foam casting fits snugly into this movement. Its efficiency, reduced waste, and lower energy consumption compared to traditional methods align with the goals of modern manufacturing. Companies are now more inclined to adopt lost foam casting as a step toward more sustainable production practices.
In conclusion, lost foam casting represents a significant leap forward in the field of metal casting. Its unique approach, blending conventional techniques with cutting-edge technology, allows for the creation of intricate, high-quality components while minimizing waste and production costs. As industries continue to evolve, the demand for such innovative casting methods is poised to grow, solidifying lost foam casting’s role as a key player in modern manufacturing. Whether in automotive engineering, aerospace, or other sectors, this method offers a promising future for efficient and sustainable production.
Post time:Dez . 26, 2024 04:39
Next:Exploring the Benefits and Applications of Fine Casting Sand in Modern Foundries