3D Printed Sand Casting Revolutionizing the Metal Casting Industry
In recent years, the manufacturing sector has witnessed an extraordinary transformation driven by the advent of additive manufacturing technologies. One such innovative approach that is making significant waves is 3D printed sand casting. This technique not only streamlines the casting process but also enhances design flexibility, reduces lead times, and minimizes material waste—characteristics that are vital in today’s fast-paced industrial landscape.
3D Printed Sand Casting Revolutionizing the Metal Casting Industry
One of the most compelling advantages of 3D printed sand casting is its design flexibility. Unlike traditional methods, which require complex and often costly patterns for intricate shapes, 3D printing allows for the creation of complex geometries that were previously unachievable. This capability empowers designers and engineers to innovate freely, leading to products that are lighter, stronger, and more efficient.
3d printed sand casting
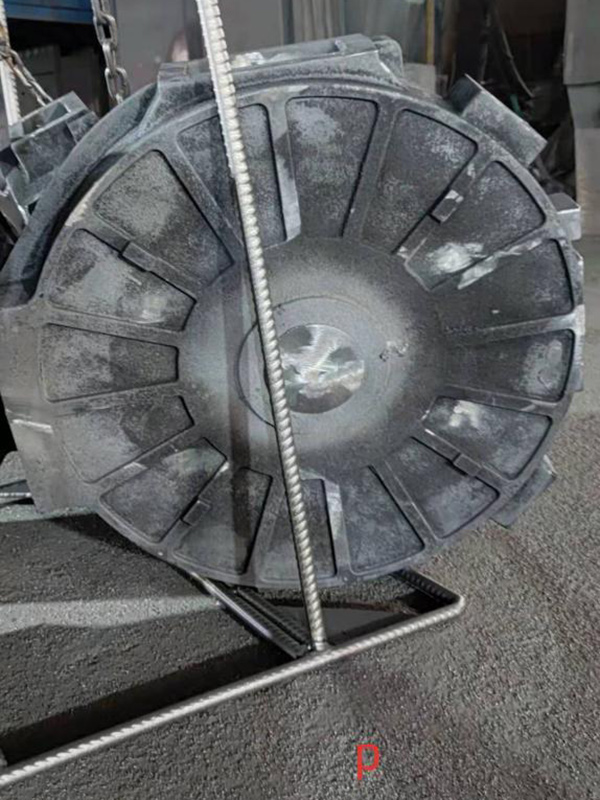
Additionally, 3D printed sand molds can significantly reduce lead times. In a traditional sand casting process, creating a mold can take days or even weeks, with hours spent on setup and production. In stark contrast, 3D printed molds can be produced in a matter of hours. This reduction in time not only accelerates the prototyping process but also enables manufacturers to react quickly to market demands, thereby gaining a significant competitive edge.
Environmental sustainability is another critical aspect where 3D printed sand casting shines. Traditional sand casting often results in a considerable amount of waste material. However, 3D printing optimizes the use of sand, minimizing excess and allowing for the recycling of unused material. In an era where environmental concerns are paramount, this sustainable approach is a significant advantage for manufacturers looking to reduce their carbon footprint.
Furthermore, 3D printed sand casting has applications across various industries, including aerospace, automotive, and art. For instance, aerospace components, which require high precision and lightweight structures, can benefit immensely from this technology. Manufacturers can create custom, complex parts that meet stringent performance criteria without the typical restrictions of conventional methods.
In conclusion, 3D printed sand casting is poised to transform the landscape of the metal casting industry. With its ability to foster design innovation, decrease production times, and promote sustainability, this technology represents a pivotal step forward. As industries continue to adopt and refine 3D printing techniques, the future of manufacturing looks more efficient, adaptable, and environmentally friendly than ever before.
Post time:Set . 22, 2024 03:03
Next:sintering sand