Steps in Sand Casting
Sand casting, one of the oldest and most versatile metal casting processes, is widely used for producing complex metal parts and components. This technique is favored in both small-scale and large-scale manufacturing due to its ability to create intricate designs and accommodate a wide variety of metals. Here, we explore the essential steps involved in the sand casting process, highlighting its significance in modern manufacturing.
1. Pattern Making
The first step in the sand casting process is pattern making. A pattern is typically made from a material like wood, plastic, or metal, and it replicates the shape of the final product, accounting for any necessary allowances for shrinkage, machining, and finishing. The pattern is crucial as it creates the cavity in the sand mold where the molten metal will be poured. Patterns can be one-piece or multi-piece depending on the complexity of the part being produced.
2. Mold Preparation
Once the pattern is ready, the next step is to prepare the mold. This involves packing sand around the pattern to create a mold. The sand used in this process, often mixed with a binding agent, must have the right consistency to hold the shape of the mold. After the sand is packed around the pattern and removed, the mold halves are joined together, and any necessary runner and riser systems are added to facilitate the flow of molten metal and compensate for shrinkage during solidification.
3
. Melting the MetalWith the mold prepared, the next step is melting the metal. Depending on the metal being used—such as aluminum, iron, or brass—different furnaces and techniques may be employed to reach the required temperature. The molten metal must be thoroughly mixed to ensure uniform composition and remove any impurities. Once the metal reaches the appropriate temperature, it is ready to be poured into the mold.
4. Pouring the Metal
steps in sand casting
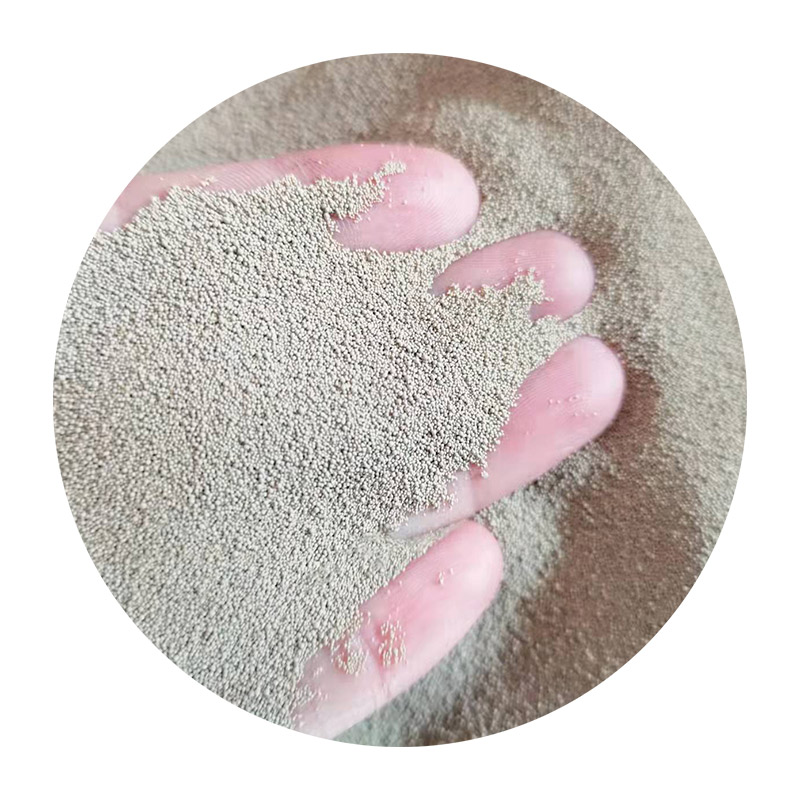
The actual pouring of the molten metal into the mold is a critical step that requires precision. The metal is poured through the gating system created in the mold and must fill the cavity completely to avoid defects. Timing and temperature are crucial during this stage, as pouring too quickly or at an incorrect temperature can lead to issues such as cold shuts or porosity.
5. Cooling and Solidification
After pouring, the mold is left to cool, allowing the molten metal to solidify. The cooling time can vary based on the thickness of the casting and the type of metal used. During this phase, solidification occurs, and the metal takes on the shape of the cavity created by the pattern. It is essential to control the cooling rate to minimize internal stresses and avoid cracking.
6. Mold Removal
Once the metal has fully solidified, the next step is to remove the mold. This involves breaking the sand mold apart carefully, usually done with a hammer or mechanically, depending on the size of the casting. The pattern is also retrieved, and if a multi-piece pattern was used, each part will be taken out separately.
7. Cleaning and Finishing
After the casting is removed from the mold, it typically requires cleaning to remove any sand or debris. This can be done through methods such as sandblasting or shot blasting. Finishing processes may include machining, grinding, or polishing to achieve the desired surface finish and dimensional accuracy of the part.
Conclusion
The sand casting process is a meticulous operation that encompasses several critical steps from pattern making to finishing. While the basic principles have remained unchanged for centuries, advancements in technology continue to enhance its efficiency and effectiveness. As a result, sand casting remains a popular choice in various industries, providing a reliable method for producing high-quality metal components that meet the demands of modern engineering.
Post time:Nov . 15, 2024 06:55
Next:resin coated sand manufacturer