Understanding Sand Casting with Resin A Modern Approach to an Ancient Technique
Sand casting is one of the oldest manufacturing processes known to humanity, dating back thousands of years. Despite its ancient origins, the techniques and materials used in sand casting have evolved significantly. One of the most notable advancements in this field is the introduction of resin in the sand casting process, enhancing both efficiency and output quality. This article will explore the workings of resin sand casting, its benefits, its applications, and how it is transforming the traditional casting landscape.
What is Sand Casting?
At its core, sand casting is a process where sand is used as a mold material to create metal castings. The sand is typically mixed with a bonding agent to hold its shape while forming a mold. Once a mold is made, molten metal is poured into the cavity created by the mold, where it solidifies and takes the desired shape. The mold is broken apart to retrieve the finished product.
The conventional method utilizes a mix of silica sand, clay, and water as the main ingredients. While this process is effective, it can sometimes lead to issues such as poor surface finish, extended lead times, and the need for complex finishing operations.
Introducing Resin in Sand Casting
Resin sand casting (also known as “resin-bonded sand casting”) incorporates synthetic resins into the sand mixture. Instead of using traditional clay as the binder, this method utilizes a resin system that combines sand with organic resins. The most common types of resin used include phenolic and furan resins due to their favorable properties.
The process begins with mixing sand with the resin and a hardening agent. This mixture is then compacted into a mold, often using a technique called the cold-box or hot-box method. In the cold-box process, the resin is activated by a catalyst introduced into the mix just before molding. Alternatively, the hot-box method activates the resin with heat once it has been shaped into a mold. Both techniques are designed to produce a high-quality, durable mold that can withstand the rigors of high-temperature molten metal.
Advantages of Resin Sand Casting
The integration of resin in sand casting offers several advantages over the traditional method
sanding casting resin
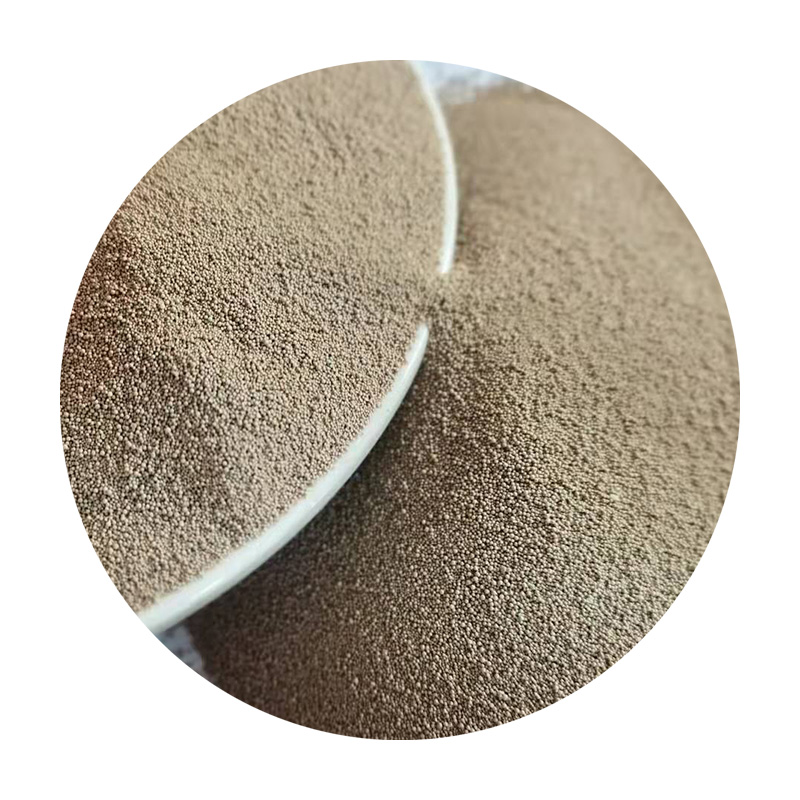
1. Improved Surface Finish Resins provide a smoother surface finish than clay-bonded sand. This results in castings that require less post-processing work, reducing manufacturing time and costs.
2. Enhanced Mold Strength Resin-bonded molds exhibit greater strength and stability, allowing for thinner-walled castings and more intricate designs without the risk of mold failure.
3. Faster Production Times The curing process of resin is quicker than that of traditional sand molds. As a result, manufacturers can achieve shorter lead times, which is essential in today’s fast-paced market.
4. Reduced Gas Evolution Traditional clay molds can generate gases during the pouring of molten metal, leading to defects in the casting. Resin molds often produce less gas, minimizing the chances of casting defects.
5. Versatility Resin sand casting is compatible with a wider range of metals, including alloys that are more challenging to cast using traditional methods.
Applications of Resin Sand Casting
The applications of resin sand casting are broad and varied. This method is particularly suited for producing complex casting shapes commonly found in industries such as automotive, aerospace, and machinery. It is often employed for making engine components, gears, and valves, where precision and surface finish are critical.
Furthermore, the ability to create intricate designs makes resin sand casting ideal for artistic applications, including sculptures and decorative items. The technique’s flexibility enables artisans and designers to realize their creative visions without the constraints often posed by traditional casting methods.
Conclusion
Resin sand casting represents a significant advancement in the casting industry, merging time-honored techniques with modern materials to improve the quality and efficiency of metal component production. As technology continues to evolve, the adoption of resin in sand casting will likely increase, opening new horizons for creativity and innovation in manufacturing. With its array of benefits and diverse applications, resin sand casting is poised to shape the future of casting in an increasingly competitive environment.
Post time:Nov . 15, 2024 19:47
Next:foundry sand density