Sand Casting Procedure An Overview
Sand casting, also known as sand mold casting, is one of the most widely used manufacturing processes for metal parts. This versatile technique allows for the production of complex shapes with good dimensional accuracy and excellent surface finish. The following is an overview of the sand casting procedure, which can be broken down into several key steps.
1. Pattern Making
The first step in the sand casting process is the creation of a pattern. A pattern is a replica of the final product to be cast, often made from materials like wood, plastic, or metal. The pattern must account for allowances for shrinkage, machining, and any possible distortions that may occur during the casting process. Patterns can be single-piece or multi-piece, depending on the complexity of the shape and the design.
2. Mold Preparation
Once the pattern is prepared, the next step is to create the mold. The mold is typically made by mixing sand with a binding agent, which helps to hold the shape during the pouring of molten metal. The sand is packed tightly around the pattern to create a mold cavity. This process may be performed manually or with the use of machines, depending on the scale of production.
After the mold has been formed around the pattern, the next step is to carefully remove the pattern from the sand mold. This step requires precision, as any damage to the mold can result in defects in the final cast product. Typically, the molds are designed to incorporate two halves, allowing for easy extraction of the pattern.
sand casting procedure
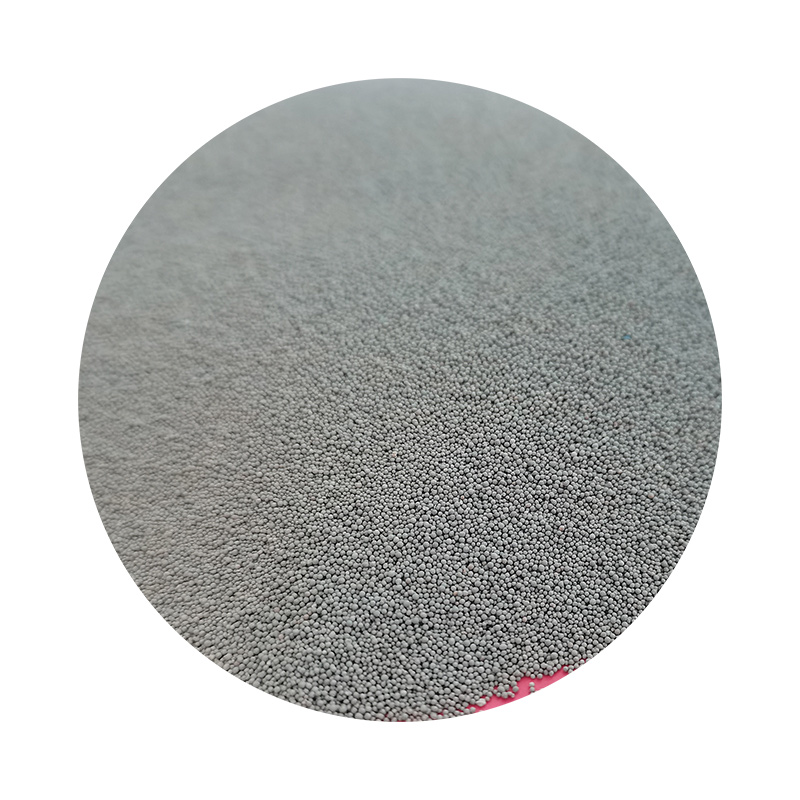
4. Pouring the Metal
With the mold prepared and the pattern removed, the next phase is ready to begin pouring molten metal into the mold cavity. The metal is heated to a temperature above its melting point and maintained in a molten state until it is ready to be poured. The pouring process must be done swiftly and smoothly to prevent defects such as cold shuts and inclusions in the finished casting.
5. Cooling and Solidification
Once the molten metal is poured into the mold, it begins to cool and solidify. The cooling time can vary significantly depending on the type of metal used and the thickness of the casting. After sufficient cooling, the mold is opened to reveal the cast part. This step may involve breaking the sand mold, which is intended to be disposable in many applications.
6. Finishing Processes
The final step involves finishing processes. These may include cleaning, grinding, machining, and any other operations necessary to achieve the desired surface finish and dimensional tolerances. Finishing is crucial to ensure that the final product meets the required specifications and is free from any imperfections.
Conclusion
Sand casting is a time-tested method that provides manufacturers with a cost-effective solution for producing a wide variety of metal parts. With careful attention to the procedures outlined above, high-quality castings can be achieved, fulfilling the needs of numerous industries, from automotive to aerospace. Understanding each step in the sand casting procedure is essential for anyone involved in metal casting, ensuring the production of durable and precise components.
Post time:Sep . 18, 2024 12:15
Next:वाळी सेरामिक