How to Make Foundry Sand
Foundry sand is an essential material used in the metal casting process, serving as a mold for molten metal to take shape. Its unique properties contribute to the production of high-quality castings and are crucial in the manufacturing of various metal products. Understanding how to make foundry sand involves knowing the right materials, the process of preparation, and its applications. This guide will take you through these critical aspects.
What is Foundry Sand?
Foundry sand primarily consists of silica (SiO2) sand, which is chemically stable and resistant to heat. It provides a smooth surface finish to metal castings and is capable of withstanding high temperatures, making it perfect for metalworking industries. While silica is the dominant component, foundry sand can also contain additives like clay and water, which help bind the sand particles together and enhance mold strength.
Materials Needed
To make foundry sand, you will need the following materials
1. Silica Sand Fine-grained silica sand is the main ingredient. 2. Clay Bentonite clay is commonly used as a binding agent. 3. Water Necessary for mixing the components to achieve the desired consistency. 4. Additives Depending on specific requirements, other additives such as coal dust or other proprietary binding agents may be mixed in.
Step-by-Step Process
1. Selecting the Right Sand Start by choosing the appropriate type of silica sand. The size and shape of the sand grains are critical; they should be spherical in shape and fine enough to pack well. Clean, high-grade silica sand is ideal for producing stable molds.
how to make foundry sand
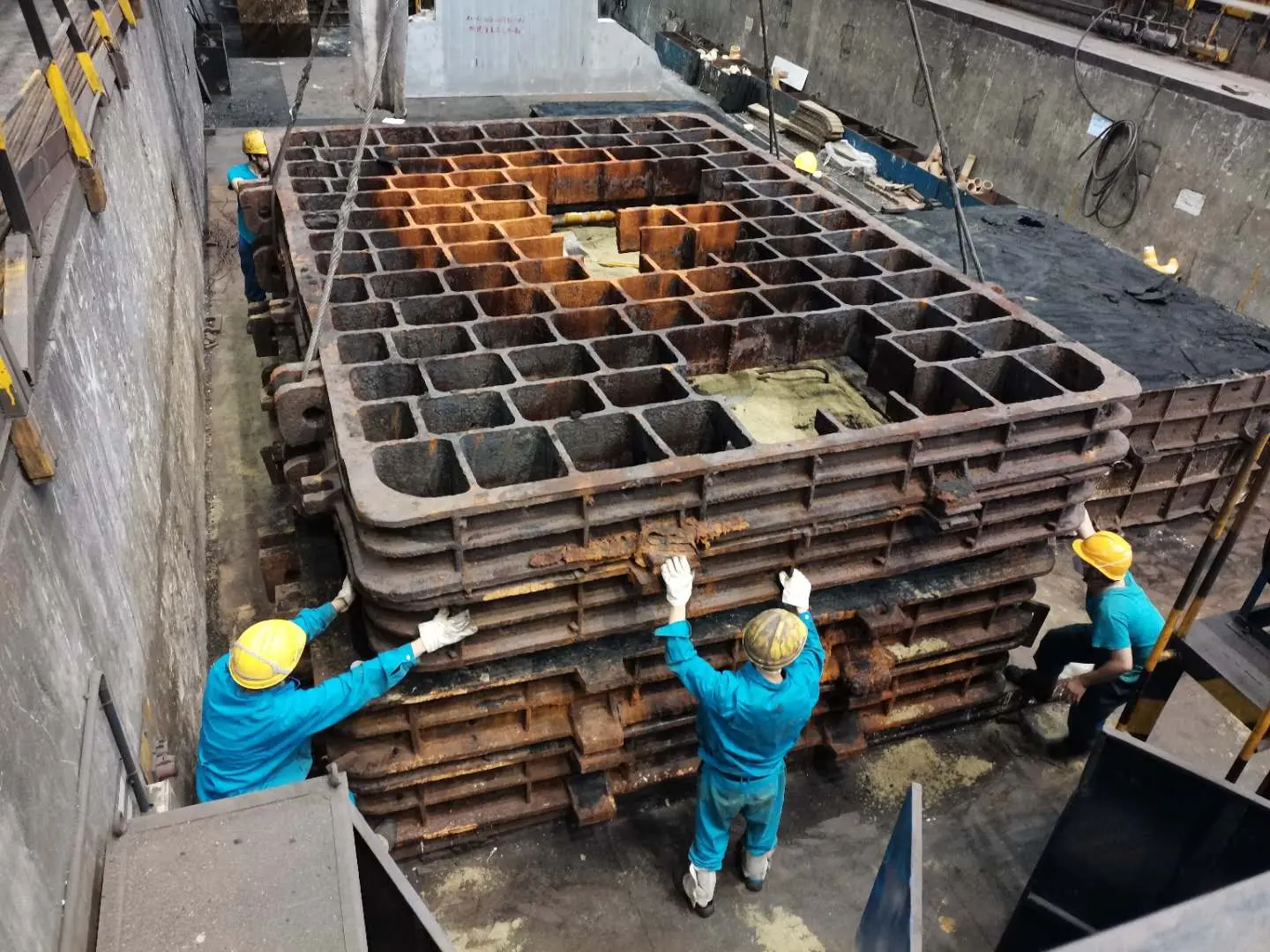
2. Preparing the Mixture - Proportioning The typical mixture contains about 90-95% sand and 5-10% clay. The exact proportions may vary based on the specifications of the foundry process and the type of metal being cast. - Mixing In a large mixing container, combine the sand and clay.
3. Adding Water Gradually add water to the sand-clay mixture while continuously mixing. Aim for a moisture content of around 2-5% by weight. The right amount of water is crucial, as too little will not adequately bind the sand, while too much will make the mixture too wet and cause it to lose its strength.
4. Homogenizing the Mixture Mix the ingredients thoroughly until a uniform consistency is achieved. This process can be done manually or with a mechanical mixer. The goal is to ensure that the clay is evenly distributed throughout the sand to enhance its binding properties.
5. Testing the Sand Before using the foundry sand, conduct a test to ensure it has the right properties. You can perform a compressive strength test and a permeability test to evaluate the mold’s integrity and how well it allows gases to escape during the casting process. Adjust the proportions of sand, clay, or water as necessary based on the test results.
Applications of Foundry Sand
Foundry sand is used in various applications, including
- Metal Casting It's the most common application, providing molds for a variety of metals including iron, aluminum, and steel. - Reclamation Used foundry sand can often be reclaimed and reused in the production of new molds, making it a sustainable option in manufacturing. - Construction Some foundries repurpose used sand for construction applications, such as fill material or as an ingredient in cement.
Conclusion
Making foundry sand is a straightforward process that involves selecting the right materials, preparing a proper mixture, and testing the outcome to ensure optimal performance in metal casting. By understanding the components and processes involved, you can contribute to high-quality production in foundry operations. Whether for professional use or a DIY project, mastering the creation of foundry sand can enhance your casting practices and ensure successful outcomes in metalworking endeavors. With proper attention to detail and a commitment to quality, foundry sand can be produced efficiently and effectively for various industrial applications.
Post time:Dec . 31, 2024 20:34
Next:Optimizing Sanding Techniques for Resin Projects and Enhancing Surface Finishes