The Differences Between Die Casting and Sand Casting
In the realm of manufacturing and metalworking, two prominent processes often come into discussion die casting and sand casting. Both techniques are used to create metal parts, but they serve different purposes and are suited for varying applications. Understanding the key differences between these two methods is vital for industries that rely on precision and efficiency.
1. Definition and Process
Die Casting is a manufacturing process where molten metal is forced into a mold cavity under high pressure. This method primarily uses non-ferrous metals, such as aluminum, zinc, and magnesium. The molds, known as dies, are often made from steel or other durable materials that can withstand the casting pressures and temperatures involved. Die casting is characterized by the production of parts with excellent dimensional accuracy and surface finish.
Sand Casting, on the other hand, is one of the oldest casting methods still widely used today. In this process, a mold is created from a mixture of sand, clay, and water. The sand is packed around a pattern to form a cavity, which is then filled with molten metal. Unlike die casting, sand casting can accommodate a wide range of metals, including iron, steel, copper, and aluminum. This method is more flexible, allowing for the creation of larger and more complex shapes.
2. Material Suitability
While both die casting and sand casting can be used to manufacture metal parts, they are limited by the types of materials that can be effectively cast. Die casting is primarily used for non-ferrous metals and is favored for applications that require a high level of detail and finished surface quality, such as automotive components, electronic housings, and medical devices.
In contrast, sand casting offers greater versatility in terms of material options. It can effectively process ferrous and non-ferrous metals, making it suitable for a broader range of applications, including larger machinery parts, architectural elements, and heavy-duty components. This flexibility often makes sand casting the preferred choice for custom, one-off productions or small batch runs.
3. Cost Implications
One of the significant differences between the two processes is the cost associated with each. Die casting typically has higher initial setup costs due to the necessity for high-quality dies, which can be expensive to manufacture. However, once the die is created, die casting can produce a high volume of parts quickly and efficiently, making it cost-effective for large production runs.
difference between die casting and sand casting
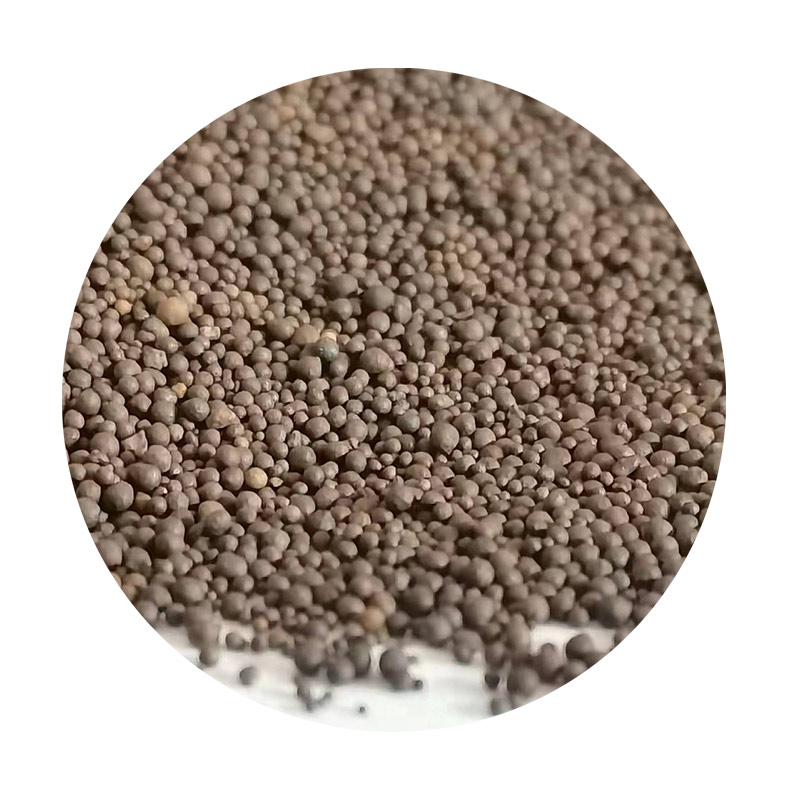
On the other hand, sand casting has lower initial costs as it does not require expensive molds. This makes sand casting an economical option for smaller production runs or prototyping. However, the casting process itself can be slower than die casting, and while it may be cost-effective for smaller quantities, the per-unit cost may increase significantly for larger volumes due to labor intensity and longer cycle times.
4. Precision and Surface Finish
Precision is another critical difference between die casting and sand casting. Die casting is known for its high dimensional accuracy, often with tolerances of ±0.1 mm or better, making it ideal for intricate designs that require tight specifications. Furthermore, the surface finish of die-cast parts is typically smoother, reducing or eliminating the need for extensive post-processing.
In contrast, sand casting generally produces a rougher surface finish and lower tolerances, which can necessitate additional machining or finishing to meet specific requirements. This factor can be pivotal depending on the application of the final product, especially in industries where precision is paramount.
5. Environmental Impact and Waste
Both casting techniques have environmental implications, but they differ in terms of waste production. Sand casting can generate more waste material, as excess sand and imperfections in the mold can lead to scrap metal. However, the sand used in the casting process is often recyclable.
Die casting tends to produce less waste, as the method is more efficient in metal usage and yields a higher percentage of usable parts. Nevertheless, the energy consumption in die casting can be higher due to the pressures and temperatures involved.
Conclusion
In summary, while die casting and sand casting serve the common goal of manufacturing metal components, they do so through different processes, suited to distinct applications. Die casting shines in its precision and surface quality for high-volume production of non-ferrous metals, while sand casting offers versatility in materials and lower startup costs, making it beneficial for custom or low-volume casting needs. Ultimately, the choice between die casting and sand casting will depend on specific project requirements, production volume, material needs, and budget considerations.
Post time:Oct . 12, 2024 09:27
Next:sand used for sand casting