Why Sand Casting is Preferred
Sand casting, one of the oldest and most versatile metal casting processes, is favored in many industries for several compelling reasons. The technique, which involves creating a mold from a sand mixture and pouring molten metal into it, has become the preferred choice for producing complex and intricate metal components. Here are some of the key reasons that underline the popularity of sand casting.
Cost-Effectiveness One of the primary advantages of sand casting is its cost-effectiveness, especially for large-scale production runs. The materials used in sand casting, particularly the sand itself, are relatively inexpensive. In addition, the initial setup costs for sand molds are lower compared to other casting methods, such as die casting or investment casting. This makes sand casting an attractive option for both small and large businesses looking to optimize their production costs without sacrificing quality.
Why Sand Casting is Preferred
Ability to Handle Large Parts One of the standout features of sand casting is its ability to produce large components. The sand molds can be built to accommodate substantial sizes, making this method ideal for manufacturing large components that would be difficult or impossible to produce using other casting techniques. Industries that often require large castings, such as construction, waste management, and heavy machinery, frequently turn to sand casting as their production method of choice.
why sand casting is preferred
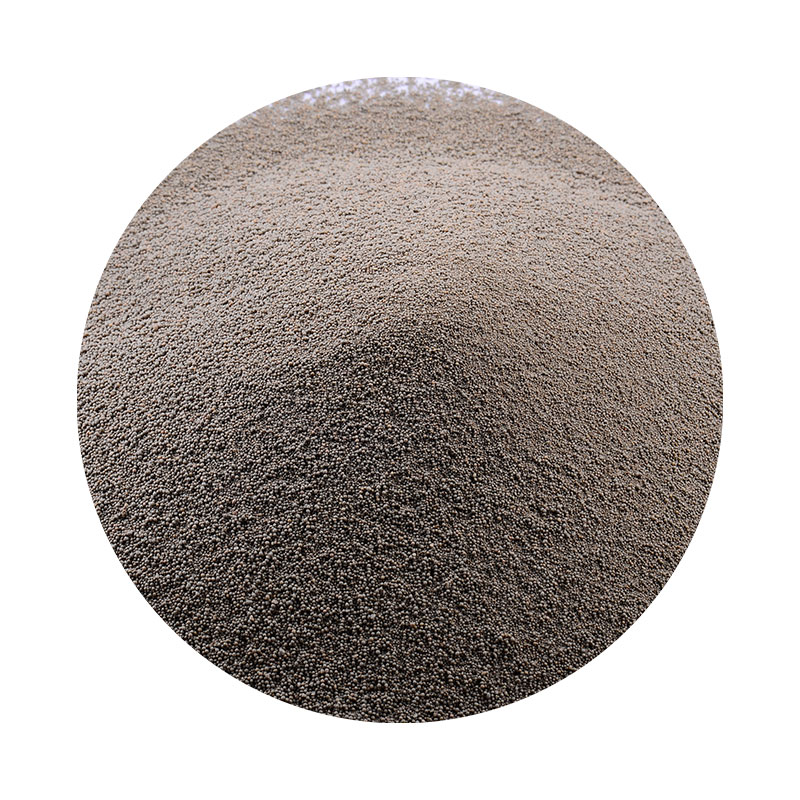
Ease of Use The sand casting process is relatively simple and straightforward, allowing for a quick learning curve for workers. The procedures are well established, and the equipment needed is generally less complex than that required for other casting methods. This ease of use can lead to shorter lead times for production and a reduced likelihood of operational errors, ultimately resulting in higher efficiency.
Thermal Properties Sand has excellent thermal properties, which allows it to withstand high temperatures without breaking down. This characteristic is crucial in metal casting as it ensures that the mold will maintain its integrity throughout the pouring process. Moreover, the sand mold's thermal conductivity helps with the cooling of the molten metal, enabling faster production cycles while maintaining the quality of the final product.
Eco-Friendliness Increasingly, industries are looking for sustainable practices, and sand casting tends to have a lower environmental impact compared to some other methods. Most foundries use recyclable sand, which can be reused multiple times, minimizing waste. Additionally, advancements in sand casting technology, such as the development of more sustainable bonding agents and additives, have contributed to its eco-friendliness.
Conclusion In summary, sand casting remains an essential manufacturing process due to its cost-effectiveness, flexibility, ability to handle large parts, ease of use, thermal properties, and eco-friendliness. As industries continue to evolve and demand more customized and high-quality components, sand casting stands out as a reliable and innovative solution. With ongoing advancements in technology and techniques, the future of sand casting looks promising, ensuring its continued relevance in the world of manufacturing. Whether for artisans creating custom works or industries producing large machinery parts, sand casting will likely remain a preferred choice for years to come.
Post time:paź . 15, 2024 13:53
Next:3d sand printerpris