Materials Used in Sand Casting
Sand casting is one of the oldest and most widely used methods for metal casting, where molten metal is poured into a mold formed by sand. This technique is especially popular for producing complex shapes and large components. The effectiveness of sand casting lies not only in the casting process itself but also in the materials used to create the mold and the casting. Here’s an overview of the essential materials involved in sand casting.
1. Sand
The most crucial component of the sand casting process is the sand itself. The primary type of sand used in this process is silica sand, which consists mainly of silicon dioxide (SiO₂). Silica sand is favored due to its excellent thermal stability and resistance to high temperatures. When combined with binders, it forms a strong mold that can withstand the molten metal's weight and temperature.
In addition to silica sand, other types of sand can be used, such as olivine, zircon, and chromite sand. Each type has its unique properties. For example, zircon sand is known for its high melting point and low thermal expansion, making it ideal for intricate molds where dimensional accuracy is critical.
2. Binders
To hold the sand particles together and create a stable mold, binders are used. The most common binder in sand casting is clay, particularly bentonite clay, which has excellent binding properties. When mixed with sand and water, bentonite helps form a cohesive mold that can retain its shape even under the stress of pouring molten metal.
In addition to clay, chemical binders (like phenolic resins) are increasingly used in modern sand casting processes like resin sand casting. These binders provide a shorter setting time and allow for more precise casting, especially for complex shapes.
3
. Additiveswhat materials are used for sand casting
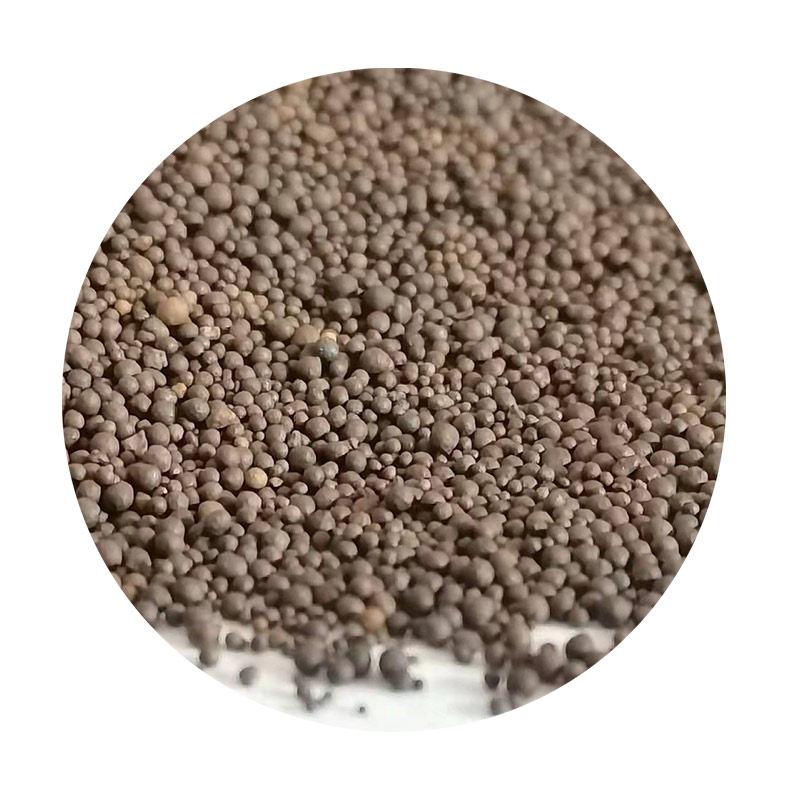
Additives are often included in the sand mixture to enhance specific properties. For instance, water is added to the sand-clay mixture to improve its moldability and ensure that the green sand (the mixture of sand and clay) can be easily shaped. Other additives may include surfactants to improve the flow characteristics or other materials to control permeability and strength.
Some foundries also use additives to improve the surface finish of castings or to inhibit defects like gas porosity and shrinkage. These additives can play a significant role in determining the final quality of the casting.
4. Core Materials
Often, sand casting requires cores made from sand to create internal features in the casting. Cores are typically made by mixing sand with binders and then shaping them to the desired form. Core materials can be designed to dissolve or collapse during the casting process, leaving behind the desired hollow features.
Cores are commonly made from the same sand mixture as the mold but often require special treatment to ensure they can resist the molten metal’s heat and maintain their integrity until the metal solidifies.
5. Melting Material
The type of metal used for casting significantly impacts the process and the materials involved. Common metals used in sand casting include aluminum, iron, and bronze, each requiring specific handling and pouring methods. The choice of metal affects the mold materials, as some metals can generate gases that can react with certain sands or binders, potentially compromising the quality of the casting.
Conclusion
In summary, sand casting is a versatile and robust manufacturing process that relies heavily on the materials used for making molds and cores. Silica sand serves as the primary component, while binders such as clay and chemical resins play a critical role in ensuring the stability and integrity of the mold. Additives enhance performance, and the choice of metal influences the overall process. Understanding these materials and their interactions is essential for optimizing the sand casting process and achieving high-quality castings. As technology evolves, the development of new materials and techniques will continue to enhance the capabilities and efficiency of sand casting, meeting the demands of modern manufacturing.
Post time:gru . 31, 2024 16:24
Next:Techniques for Sanding 3D Prints to Achieve a Smooth Finish