Wet Sanding Ceramics A Comprehensive Guide
When it comes to finishing ceramics, wet sanding is one of the most effective methods to achieve a smooth, glossy surface. This technique not only enhances the aesthetic appeal of ceramic pieces but also adds durability to the finished product. Whether you are a professional potter or a hobbyist looking to refine your craft, understanding the wet sanding process can elevate your ceramic works to a new level.
What is Wet Sanding?
Wet sanding involves the use of water as a lubricant while sanding the surface of ceramics. The main purpose of this method is to minimize dust and reduce the possibility of scratching the ceramic surface. By keeping the work area wet, particles of sandpaper and ceramic dust are suspended in the water, making cleanup easier and providing a finer finish. This technique is ideal for preparing surfaces for glazing or for smoothing out imperfections from the firing process.
The Tools Required
1. Sanding Pads Choose high-quality sanding pads specifically designed for wet sanding. These pads come in various grits, ranging from coarse to fine. Coarse grits (like 180-320) are used for the initial sanding, while finer grits (500-2000) are employed for the finishing touches.
2. Water Container A small bucket or a spray bottle filled with water is necessary to keep the surface moist during the sanding process.
4. Protective Gear Although wet sanding produces less dust than dry sanding, wearing a mask and goggles is still advisable to protect yourself from any particulate matter.
The Wet Sanding Process
1. Prepare the Ceramic Piece Start by inspecting your ceramic piece for rough spots, imperfections, or any sharp edges that need smoothing. Ensure that the piece is fully cured and that any previous glaze has been removed.
wet sanding ceramics
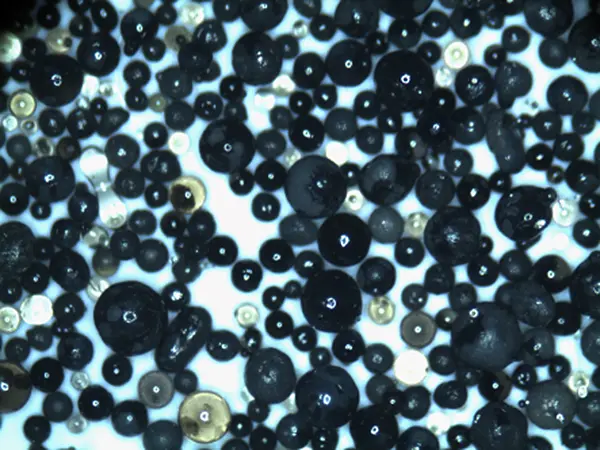
2. Choose the Right Grit Begin with a coarse grit sanding pad to remove major imperfections. Dip the sanding pad in water and apply it to the ceramic surface with light, even pressure. It’s crucial to keep the pad moist but not overly saturated. You can apply water directly on the ceramic or on the pad itself.
3. Sand the Surface Use circular or back-and-forth motions as you work on the surface. Do not apply too much pressure, as ceramics can be fragile and may crack if over-sanded. Change the water and rinsing the ceramic piece frequently to keep the surface clean.
4. Progress to Finer Grits After achieving a relatively smooth surface with the coarse grit, switch to a finer grit pad. Repeat the same process, ensuring the surface remains wet. As you move to finer grits, you will notice a more polished look emerging.
5. Final Steps For the ultimate sheen, finish with the finest grit sanding pad. After completing the sanding process, rinse the piece thoroughly with water to remove any debris or residue. Allow it to dry completely before applying any glaze or finish.
Benefits of Wet Sanding
- Reduced Dust One of the primary advantages of wet sanding is the reduction of dust, which not only benefits the artisan’s health but also keeps the workspace clean.
- Enhanced Finish Wet sanding provides a much smoother finish compared to dry sanding. This is particularly important for pieces intended for glazing, as a smooth surface allows for better adhesion of the glaze.
- Control Over the Process The lubrication provided by water allows for better control during sanding, making it less likely to unintentionally damage the ceramic piece.
Conclusion
Wet sanding is a valuable technique in the ceramics industry that significantly enhances the quality of the finished product. By using the right tools and following the proper techniques, you can achieve a professional-looking finish on your ceramic pieces. Whether you are preparing a work for glaze or simply refining its surface, wet sanding is an essential skill that will benefit every ceramics enthusiast. As you practice this technique, you will gain confidence in your ability to create stunning ceramic pieces that showcase your artistry.
Post time:lis . 10, 2024 05:02
Next:Innovative Techniques in 3D Printing for Efficient Sand Casting Processes